17.02.2022
группа: 412
Предмет: Техника и технология ручной дуговой сварки (наплавка, резка) неплавящимися электродами в защитном газе.
Тема урока: Технология сварки меди и ее сплавов. Трудности при сварке меди. В 1991 году
изобретена и впервые опробована технология Friction stir welding (сварка
трением с перемешиванием). С помощью данной технологии создают прочное
неразъёмное соединение любых цветных металлов, включая трудносвариваемые
алюминий, магний, титан и высоколегированные стальные сплавы.
Преимущества
перед сваркой плавлением делают FSW востребованным методом в автомобильной
промышленности, на производстве ракетоносителей, самолетов, поездов и т.д.
Все бы
хорошо, но даже сварка меди обойдётся минимум в 600 тысяч евро. Такое
оборудование вряд ли доступно рядовому сварщику автосервиса или домашнему
мастеру.
Что же
делать? Прибегнуть к старому доброму аргонодуговому способу (TIG), который при
должном опыте позволит добиться отличного результата в работе с цветными
металлами.
Как выполняется аргонодуговая сварка меди: правила, принципы и особенности
технологии
Сегодня
разработаны и активно используются несколько технологий для образования
неразъёмного соединения медных деталей. Метод сварки меди аргоном считается
одним из самых эффективных. Соединение заготовок в среде инертного газа
позволяет работать с крупными и мелкими частями с образованием надёжного шва.
Температура
плавления меди и её сплавов достаточно низкая. Чистый металл переходит в жидкое
состояние при 1083 0С, бронза при 950 0С. Это создаёт некоторые сложности при
работе с расплавом. Для тонких деталей высока вероятность прожига, в
толстостенных заготовках металл быстро становится текучим и выплёскивается из
ванны.
Высокая
теплопроводность (в 2 раза выше в сравнении с алюминием) требует
предварительного прогрева заготовок до температуры 350–600 0С с помощью газовой
горелки. Приём снижает риски возникновения дефектов в месте контакта частей.
Температура подбирается опытным путём в зависимости от толщины кромок и чистоты
основного металла.
Сварку выполняют вольфрамовым электродом. Неплавящийся рабочий инструмент
хорошо проваривает металл с образованием ровного и прочного шва. В линейке
различают две марки:
·
ЭВЛ: лантанированные
элементы производят с добавлением оксида лантана 1,1–1,4%. Считается
универсальным рабочим инструментом для сварки аргоном.
·
ЭВИ:
итерированные электроды относятся к одним из самых стойких в ряду неплавящихся.
Их применяют для самых ответственных участков сварки. В качестве добавки к
вольфраму используют 1,8–2,2% оксида иттрия — соединение улучшает стабильность
катодного пятна на участке поджига дуги, что в конечном итоге повышает её
стабильность в расширенном интервале рабочих токов.
Сварка меди аргоном
выполняется с использованием ЭВИ–электродов на постоянном токе. Среда защитного
газа необходима, чтобы убрать процесс образования оксида меди в реакции
взаимодействия с кислородом воздуха. В отличие от чистого металла диоксид
относится к тугоплавким соединениям (1380 0С). Его образование затрудняет
сварку и ухудшает качество шва.
Использование аргона
Метод tig
сварки меди в защитной среде аргона позволяет практически полностью подавить
образование оксида. В процессе работы не происходит разбрызгивания металла с
разлётом искр, что позволяет использовать технологию даже в жилых помещениях.
Защитный газ обеспечивает надёжное соединение тонких заготовок с толщиной
частей 0,5 мм.
Опытные
сварщики добавляют к аргону азот в соотношении 75% к 25%. В таких условиях
сварка аргоном приводит к возрастанию стабильности дуги, добавление азота
улучшает характеристики сварочной ванны, способствуя более глубокому провару
деталей.
Подготовка металла
Прежде чем
варить медь, необходимо обеспечить чистоту сварного соединения. На процесс
сварки меди аргоном влияет качество металла в месте стыка, поэтому необходима
тщательная зачистка поверхностей абразивным материалом. После грубой подготовки
участок обезжиривают растворителем.
Кромки
толщиной более 5 мм предварительно разделывают. Без этого приёма невозможно
выполнить сварку меди аргоном, технология не позволит равномерно по всей
глубине поварить металл из–за его высокой теплопроводности.
Для изделий толщиной в пределах 5–12 мм подходит метод односторонней
разделки. Угол скоса зависит от следующих критериев:
·
Толщины
свариваемых заготовок: чем больше параметр, тем шире должен быть угол открытия.
·
Диаметра
электрода: для стержня необходимо обеспечить достаточный доступ к корню шва.
·
Метода
работы: для сварки меди в среде аргона достаточно обеспечить угол 40–50 0С.
Заготовки
толщиной более 12 мм разделывают по каждой из сторон.
Режим аргонодуговой сварки.
Настройки
под аргонодуговой аппарат подбирают к толщине свариваемых деталей и в
зависимости от диаметра используемого электрода:
Толщина медных кромок, мм
Ø электрода, мм
Сварочный ток, А
Расход защитного газа, л/мин
1,2
2,5–3,0
120–130
От 7 до 8,5
1,5
2,5–3,0
140–150
От 7 до 8,5
2,5
3,5–4,0
220–230
От 7,5 до 10
3,0
3,5–4,0
230–240
От 7,5 до 10
Кроме
неплавящихся вольфрамовых электродов аргоновая сварка меди ведётся с
использованием присадочной проволоки. Расходник помогает устранить небольшое
количество кислорода, которое всё–таки проникает в сварочную зону.
Желательно
выбирать проволоку, близкую по составу к свариваемому металлу. Обычно берут
материал с включением марганца. Добавка эффективно связывает проникающий
кислород, устраняя появление тугоплавкого оксида. Вместе с тем включения
марганца ухудшают качество шва, снижая однородность и прочность соединения. Для
того чтобы улучшить результат сварки, желательно использовать проволоку с
добавками редкоземельных элементов. Материалы, также как и марганец, полностью
удаляют кислород из сварочной зоны, но при этом сами не остаются в сварном шве.
Плохо то, что это один из самых дорогих расходников, применение которого для
бытовых операций, как правило, не оправданно.
В домашней
практике часто используют обычные медные провода, тщательно зачищая поверхность
от защитного лака и обезжиривая. Желательно, чтобы температура плавления
расходника была немного ниже, чем у соединяемого металла.
Полезные советы для сварки меди аргоном
·
Толстостенные
детали (более 12 мм) можно сваривать без присадочной проволоки за счёт
наплавления металла заготовок.
·
В процессе работы
горелку следует вести плавно зигзагами, заходя поочерёдно на одну и другую
сторону линии соединения. Приём позволяет выполнить расплавление более
равномерно, что улучшает качество шва.
·
Тонкие
детали сваривают прерывистым укороченным шагом — способ позволяет избежать
прожога материала.
·
На концевых
участках ванны используют функцию заварки кратера. Если опция не предусмотрена
в аппарате, дугу плавно отводят вручную, используя метод постепенного
удлинения.
·
Присадочную
проволоку всегда располагают перед горелкой.
·
Медные трубы
сваривают прерывистым швом на небольших токах.
Технология
аргонодуговой сварки позволяет выполнять соединение как в вертикальном, так и в
горизонтальном направлении. Техника работы и подбор сварочных токов осваиваются
на опыте, поэтому при недостатке навыка желательно попрактиковаться на ненужных
частях и только после этого приступать к сварке ответственных деталей.
Изучить: 1. Процесс
выполнения сварки меди.
2. Подготовка металла к сварке.
3. Режимы сварки.
17.02.2022
группа: 412
Предмет: Техника и технология ручной дуговой сварки (наплавка, резка) неплавящимися электродами в защитном газе.
Тема урока: Техника сварки деталей из алюминиевых сплавов.Способы
сварки алюминия и его сплавов.
Для алюминия
и его сплавов возможно применение почти всех промышленных способов сварки
плавлением и давлением. Ручную дуговую сварку покрытыми электродами в настоящее
время используют редко, хотя она в принципе возможна. Наибольшее
распространение для изготовления сварных конструкций приобрела дуговая сварка в
инертных газах. Автоматическую дуговую сварку с использованием флюсов применяют
для крупногабаритных конструкций, электрошлаковую - для металла больших толщин.
Для получения сварных швов с высокими механическими характеристиками используют
также электроннолучевую и лазерную сварку.
Дуговая
сварка в среде инертных газов наиболее распространена при изготовлении конструкций
из алюминиевых сплавов ответственного назначения. Осуществляется как
неплавящимся вольфрамовым электродом, так и плавящимся. Используемые инертные газы:
аргон высшего и первого сорта по ГОСТ 10157-79, гелий высокой чистоты и смесь
аргона с гелием. Выбор конкретного способа сварки определяется толщиной
металла, конструкцией изделия и масштабом производства.
Дуговая
сварка неплавящимся вольфрамовым электродом. В качестве неплавящегося электрода применяют
вольфрам с добавками лантана, иттрия и других элементов. Использование чистого
вольфрама не рекомендуется. Отмеченные примеси придают электроду повышенную
стойкость, обеспечивают большую плотность тока и другие преимущества.
Питание дуги
осуществляется от источника переменного тока, что обеспечивает разрушение
оксидной пленки за счет эффекта катодного распыления. Использование дуги
переменного тока связано с тем, что при сварке постоянным током обратной полярности
из-за возможного расплавления вольфрамового электрода допустим сварочный ток
небольшой величины, а при сварке постоянным током прямой полярности затруднено
удаление оксидной пленки.
Сварку
вольфрамовым электродом выполняют вручную, механизировано или автоматически.
При сварке в среде гелия напряжение повышается на 7... 10 В, при этом дуга
укорачивается, а сила тока снижается на 10... 15 %. Расход газа при
использовании гелия увеличивается в
1,8...2,2
раза. Ручная сварка ведется на меньших значениях тока в один или несколько
проходов в зависимости от толщины.
Дуговая
сварка вольфрамовым электродом в среде инертных газов является наиболее
универсальным способом сварки, который позволяет выполнять сварку в различных
пространственных положениях и труднодоступных местах. При этом достигается
высокая прочность и пластичность сварных соединений, близкие к прочности и
пластичности основного металла.
Сварка
вольфрамовым электродом диаметром 2...6 мм целесообразна для узлов алюминия и
его сплавов толщиной до 12 мм. Металл толщиной до 3 мм сваривают за один проход
на стальной подкладке; при толщине металла 4...6 мм сварку выполняют с двух
сторон, а начиная с толщины 6...7 мм применяют разделку кромок (V- или
Х-образную). Соединение с отбортовкой кромок целесообразно для металла толщиной
0,8...2 мм. Присадочный металл выбирают в зависимости от марки сплава: для
технического алюминия - проволоку марок АО, АД или АК, для сплавов типа АМг -
проволоку той же марки, но с
увеличенным
(на 1___1,5 %) содержанием магния для компенсации его
угара.
Диаметр проволоки составляет 2...5 мм. Рекомендуемые режимы ручной сварки
приведены в табл. 14.
Рекомендуемые
режимы ручной дуговой сварки вольфрамовым электродом
Таблица 14
Толщина
металла, мм
Диаметр,
мм
Сила тока,
А
вольфрамового
электрода
присадочной
проволоки
в аргоне
в гелии
1...2
2
1...2
50...70
30...40
3...4
3
2...3
100...130
60...90
4...6
4
3
160... 180
ПО...130
6...10
5
3...4
220...300
160...240
11...15
6
4
280...360
220...300
Для
обеспечения надежной газовой защиты в зависимости от режима сварки
устанавливают оптимальный расход газа (от 4 до 12 л/мин при ручной сварке и до
30 л/мин при автоматической). Чрезмерный расход газа приводит к его
турбулентному истечению и засасыванию воздуха в зону дуги, т. е. к нарушению
газовой защиты, а при малом истечении газа (или чрезмерно большой скорости
сварки) защита зоны сварки будет недостаточной. Подачу защитного газа включают
с помощью аппаратуры управления за 3...5 с до возбуждения дуги, а выключение
подачи - через 5...7 с после обрыва дуги.
При
выполнении сварки алюминия и его сплавов вручную особое внимание уделяется
технике сварки. Угол между присадочной проволокой и электродом должен быть
примерно 90°. Присадка подастся короткими возвратно-поступательными движениями.
Недопустимы поперечные колебания вольфрамового электрода. Длина дуги -
1,5...2,5 мм. Вылет электрода от торца наконечника горелки - 1___1,5 мм. Сварку
обычно ведут справа налево («левый» способ), чтобы снизить перегрев свариваемого
металла.
Для сварки
алюминия и его сплавов малых толщин целесообразно применять импульсную дугу
переменного тока. При ее использовании удается сваривать алюминиевые сплавы
толщиной от 0,2 мм. Стыковые соединения металла толщиной 0,2... 1 мм сваривают
на стальных подкладках с формирующей канавкой, используя присадочную проволоку
диаметром 0,6...0,8 мм. При этом коробление изделия снижается на
40.. . 60%.
Сварка
плавящимся электродом. Плавящийся электрод применяют при дуговой сварке алюминиевых сплавов
толщиной более 4 мм. Сварку выполняют на постоянном токе обратной полярности
при силе тока, обеспечивающей струйный перенос электродного металла, проволокой
1.5.. .2.5
мм. В связи с недостаточно высокой жесткостью алюминиевой проволоки сварка
проволокой диаметром менее 1,2... 1,5 мм затруднительна. Сварку ведут в чистом
аргоне либо в смеси аргона и гелия (до 70 % Не). При этом газовую смесь
предпочитают при сварке металла больших толщин.
Изучить: 1. Процесс сварки алюминия.
2. Режимы
сварки алюминия.
3. Сварка
алюминия плавящимся электродом.
17.02.2022
группа: 412
Предмет: Техника и технология частично механизированной сварки (наплавка) плавлением в защитном газе.
Тема урока: Характеристика алюминиевых, никелевых, титановых сплавов. Особенности технологии сварки (наплавки).Характеристика
алюминиевых, никелевых, титановых сплавов.
Сварка
алюминиевых и магниевых сплавов. Наличие оксидной пленки на поверхности алюминия
препятствует сплавлению свариваемых кромок между собой, а также основного и
присадочного металлов. Для предотвращения попадания оксидной пленки в сварной
шов необходимо перед сваркой удалять оксидную пленку химическими растворителями
с поверхности основного и присадочного металлов.
Вследствие
высокой теплопроводности и теплоемкости металла следует использовать для
сварки алюминиево-магниевых сплавов мощные источники теплоты с
высокой степенью концентрации тепловой энергии. Высокий коэффициент линейного
расширения сплавов способствует короблению изделий при нагреве. Сварку
конструкций из алюминиево-магниевых сплавов нужно вести в жестких зажимных
приспособлениях - кондукторах.
Сварку
конструкций выполняют покрытыми электродами, по слою флюса, в защитных газах
неплавящимся или плавящимся электродами, а также можно применять электрошлако-
вую сварку. Сварку покрытыми электродами выполняют при толщине металла менее 4
мм. При сварке неплавящимся электродом уровень качества сварного соединения
выше, чем при сварке плавящимся электродом, но при этом производительность
процесса сварки ниже.
Сварка
титановых сплавов. Вследствие
малой теплопроводности титановых сплавов на образование сварного соединения
требуется меньшее количество теплоты, чем при сварке малоуглеродистой стали.
Параметры режима сварки титановых сплавов близки к параметрам режима сварки
аустенитных сталей. Титановые сплавы немагнитны, поэтому нет опасности
магнитного дутья, но в то же время для сварки нельзя применять магнитные
стенды. В расплавленном состоянии титановые сплавы имеют высокую жидкотекучесть
и обладают высоким коэффициентом поверхностного натяжения, поэтому сварные
соединения склонны к прожогам. К сборке стыков из титановых сплавов предъявляют
более жесткие требования, чем при сварке других конструкционных материалов.
В связи с
высокой химической активностью титана при повышенных температурах и особенно в
расплавленном состоянии основной трудностью при сварке плавлением является
обеспечение надежной защиты от атмосферы не только сварочной ванны и корня шва,
но и остывающих участков сварного соединения, нагретых до температуры свыше 350
°С. Сварные конструкции обычно изготавливают дуговой сваркой в защитных
инертных газах.
В
зависимости от конфигурации и размеров свариваемых узлов применяют три типа
защиты зоны сварки инертным газом:
- ? общую защиту в камере с
контролируемой атмосферой;
- ? защиту только сварного
соединения с использованием местных камер;
- ? струйную защиту зоны сварки,
осуществляемую непрерывным обдуванием сварочной ванны и остывающих
участков сварного соединения перемещением сварочной горелки.
Камеры с
контролируемой атмосферой обеспечивают наиболее надежную защиту сварного
соединения. Применение таких камер особенно целесообразно в серийном
производстве в том случае, когда конструкция имеет сложную конфигурацию, а швы
располагаются в труднодоступных местах. Сварку в камерах выполняют вручную и в
автоматическом режиме, при этом сварщик может находиться как вне камеры, так и
в ней в специальном скафандре. Камеры с размещенными в них деталями,
подлежащими сварке, сначала вакуумиру- ют, а затем заполняют инертным газом.
Местные
защитные камеры используют с предварительным вакуумированием или без него. В
последнем случае вытеснение воздуха обеспечивается продувкой такой камеры
5-10-кратным объемом инертного газа. Разновидностью местных защитных камер
являются накидные малогабаритные камеры. Такие камеры предназначены, главным
образом, для автоматической сварки неповоротных стыков трубчатых конструкций.
Наибольшее
распространение имеет сварка неплавящимся электродом на воздухе. Для
обеспечения надежной защиты зоны сварки разработаны специальные горелки с
соплами с удлиненной насадкой, подкладки и другие приспособления. Аргонодуговую
сварку выполняют на постоянном токе прямой полярности.
Для сварки
титановых сплавов малой толщины (менее 1,5-2 мм) находит применение
импульсно-дуговая сварка неплавящимся электродом. При этом снижается перегрев
металла, уменьшаются сварочные деформации и несколько повышается пластичность
швов. Для сварки титановых сплавов толщиной более 3 мм можно применять сварку
под слоем флюса. Сварку ведут на остающейся металлической подкладке, на медной
технологической подкладке или на флюсовой подушке. Высокое качество сварки
титана и его сплавов обеспечивает применение электронно-лучевой сварки и
дуговой сварки в вакууме.
Трудности полуавтоматической сварке титана.
Титан и его сплавы обладают высокой химической активностью,
что обусловливает необходимость предохранения от окисления даже участков
околошовной зоны при нагревании до 250-300 градусов. Поскольку в околошовной
зоне часто наращивается зерно, необходимо выбирать подходящий токовый режим.
Газовые примеси (в первую очередь, водорода),
растворенные в основном и присадочных металлах, вызывают образование пор и
холодных трещин.
Из-за низкой вязкости расплавленного металл велик
риск образования прожогов.
Подготовка к полуавтоматической сварке.
Раскрой на заготовки
и подготовка кромок чаще всего проводятся механическими способами. Если изделия
являются толстостенными, можно провести разделительную резку и подготовку
кромок газотермическими методами, но затем надо обязательно обработать кромки
механически на глубину как минимум 3-5 мм. Для зачистки кромок на ширину 15-20
мм используются металлические щетки, шаберы и прочие приспособления.
Обязательным является последующее обезжиривание кромок. Если перед сваркой
проводилась вальцовка, ковка, штамповка или другие виды термообработки,
необходимо очистить поверхности гидропескоструйным или дробеструйным аппаратом
(подробнее см. Очистка поверхности металла перед сваркой). После этого они
подвергаются химической обработке: рыхлению оксидной пленки; травлению;
осветлению.
После того, как свариваемая поверхность химически
обработана, свариваемые кромки на 20 мм промываются бензином и протираются
ацетиленом или этиловым спиртом. Сварочная пленка на предварительном этапе
подвергается вакуумному отжигу, а затем – обезжириванию Сварка проводится в
специальных приспособлениях, либо на прихватках, выполненных ручной
аргонодуговой сваркой W-электродом. Когда свариваемые поверхности уже готовы к
работе, к ним нельзя прикасаться незащищенными руками.
Выбор режимов
полуавтоматической сварки титана.
При
полуавтоматической сварке титана используется постоянный ток обратной
полярности. При выборе режимов учитывается толщина металла, склонность сплава к
росту зерна и подверженность термическому циклу. Чтобы максимально уменьшить
рост зерна, стоит выбирать режимы с повышенными скоростями и незначительной
погонной энергией. Поскольку титан имеет высокое электрическое сопротивление,
сварка проводится с небольшими вылетами электрода. Однако при работе с
использованием невысоких токовых режимов есть риск непровара корня шва. Чтобы
избежать этого, корень стоит выполнить ручной аргонодуговой сваркой
W-электродом, а остальную разделку – сваркой плавящимся электродом. Основное
положение – нижнее. Если используется сварка с глубоким проплавлением на
повышенных токовых режимах, необходимо использовать гелиево-аргоновую газовую
смесь (80% + 20%). Для увеличения пластичности, прочности и устойчивости к
образованию трещин сварочные швы требуют дополнительной термической обработки,
выбрав режим в зависимости от состава сплава.
Техника
полуавтоматической сварки титана.
При механизированной
сварке титана плавящимся электродом в инертных газах особые сложности связаны с
обеспечением надежной защиты зоны нагрева. Поэтому, если применяется этот метод
сварки, работа проводится в специальных камерах, где контролируется атмосфера.
Сварка в монтажных условиях проводится импульсно-дуговым способом, что
обеспечивает более высокую производительность, чем альтернативный вариант –
ручная сварка неплавящимся электродом при одновременном снижении погонной
энергии в 2-2,5 раза. В некоторых случаях используется вакуумная сварка титана
и его сплавов, главным преимуществом которой является чистота металла шва, в
котором не образуются примеси из неметаллических элементов и газов. Режим
сварки и ее техники необходимо выбрать так, чтобы обеспечить устойчивое горение
дуги с минимумом разбрызгиваний. Для этого необходим струйный перенос
электродного металла. Важно выбрать оптимальное соотношение сварочного тока,
скорости подачи электродной проволоки, дугового напряжения и вылета электрода.
Газовая защита.
Одним из важнейших
условий получения качественного соединения при сварке титановых сплавов
является обеспечение надежной газовой защиты: сварного шва; участков основного
металла, которые нагреты до 250-300 градусов. Можно выбрать один из трех
вариантов газовой защиты: струйная – с задействованием специальных
приспособлений; местная – в герметичных камерах малого объема; общая – в
камерах с контролируемой атмосферой (УБС-1, ВКС-1, ВУАС-1).
Рис. 1 Защитная камера для сварки титана Дополнительные
защитные устройства изготавливаются из нержавеющей стали. Необходимо, чтобы
были предусмотрены газовые линзы и рассекатели. К газовой горелке прикрепляется
специальная насадка для защиты кристаллизующейся сварочной ванны. Ее ширина
должна быть 40-50 мм, а длина – 60-120 мм в зависимости от режима сварки. При
сварке кольцевых поворотных и неповоротных стыков, а также трубчатых
конструкций используются местные или малогабаритные камеры.
Рис. 2. Вспомогательное оборудование для защиты зоны сварки
Качество защиты можно определить по внешнему виду металла шва. Если его
поверхность является серебристой или светло-желтой, защиту можно считать
достаточной. Сварной шов желто-голубого цвета свидетельствует о нарушениях
защиты, хотя в некоторых случаях такие швы вполне допустимы. О некачественном
шве свидетельствует синевато-серый и темно-синий цвет.
Изучить: 1. Характеристика
цветных сплавов.
2. Подготовка к полуавтоматической сварке.
3. Газовая защита сварочной ванны.
17.02.2022
группа: 412
Предмет: Техника и технология частично механизированной сварки (наплавка) плавлением в защитном газе.
Тема урока: Характеристика меди и ее сплавов. Особенности технологии сварки (наплавки).Сварочные
характеристики меди.
Для меди, характерны такие ее технические характеристики, как высокая
стойкость по отношению к воздействию различных химических веществ, сохранение
высоких механических свойств в условиях глубокого холода, высокие показатели
теплопроводности и электропроводности.
Необходимо учитывать следующие особенности меди и ее сплавов, влияющие на
технологию сварки.
1. В связи с высокой температурой и теплопроводностью, затрудняющими
локальный разогрев, требуются более концентрированные источники нагрева и
повышенные режимы сварки. Однако в связи со склонностью меди к росту зерна при
сварке многослойных швов металл каждого прохода для измельчения зерна
проковывают при температурах 550-800° С.
2. Легкая окисляемость меди при высоких температурах приводит к засорению
металла шва тугоплавкими окислами. Закись меди растворима в жидком металле и
ограниченно — в твердом. С медью закись образует легкоплавкую эвтектику Сu—Сu2О (температура плавления 1064° С), которая
сосредоточивается по границам зерен и снижает пластичность меди, что может
привести к образованию горячих трещин.
3. При сварке латуней возможно испарение цинка. Образующийся окисел цинка
ядовит, поэтому при сварке требуется хорошая вентиляция. Испарение цинка может
привести к пористости металла шва. Это осложнение удается преодолеть
предварительным подогревом металла до температуры 200-300° С и повышением
скорости сварки, уменьшающим растекание жидкого металла и испарение цинка.
4. Медь в расплавленном состоянии поглощает значительные количества
водорода. В околошовной зоне диффузионно-подвижный водород взаимодействует с Сu2О, располагающейся но границам зерен;
образующиеся пары воды, которые не растворяются в меди и не могут из нее выйти,
создают в металле значительные напряжения, приводящие к образованию большого
числа микротрещин. Это явление получило название водородной болезни меди.

5. Высокий коэффициент линейного расширения (в 1,5 раза больше, чем у
стали) может вызвать при сварке повышенные температурные и остаточные
сварочные напряжения и деформации. Для уменьшения деформации конструкции сварку
ведут в жестком закреплении, по прихваткам. При повышенной толщине металла
регулируют величину зазора.
6. Повышенная жидкотекучесть расплавленной меди и ее сплавов (особенно
бронзы) затрудняет сварку в вертикальном и потолочном положениях, поэтому чаще
всего сварку ведут в нижнем положении. Для формировании корня шва без дефектов
необходимы подкладки.
Для меди и сплавов на ее основе могут быть
использованы все основные способы сварки плавлением. Сварка в защитных
газах позволяет получать сварные соединения с наиболее высокими свойствами
(механическими, коррозионными и т. д.), так как металл шва содержит минимальное
количество примесей. Сварку выполняют неплавящимся (вольфрамовым) и плавящимся
электродами. Используют вольфрамовые лантанированные или иттрированные
электроды диаметром до 6 мм. В качестве присадочного металла при сварке
плавящимся электродом пригодна проволока из меди и ее сплавов, которые по
составу идентичны основному металлу, но содержат раскислители. При сварке
используют инертные по отношению к меди газы: аргон, гелий (чистотой 99,9%),
азот. При неплавящемся электроде сварку выполняют на переменном токе или на
постоянном токе прямой полярности. При сварке плавящимся электродом используют
постоянный ток обратной полярности.
Подготовка под сварку
металла и электродной проволоки
Проволоки, листы, плиты, трубы и другие полуфабрикаты
из меди должны иметь сертификаты, определяющие их марку и химический состав. На
заводе работники ОТК проверяют поступившие медь на соответствие свойств и
состава сертификатам, ГОСТам или техническим условиям.
Медные листы и плиты в процессе хранения укладывают в
горизонтальное положение без провисания с прокладкой между ними алюминия меди
или мягких пород дерева, исключающих образование на меди вмятин и других
повреждений.
В меди, предназначенной для изготовления ответственных
сварных конструкций перед запуском в производство необходимо проконтролировать
содержание кислорода, которое не должно превышать 0,01 %. Кроме того, требуется
определить содержание висмута и свинца с помощью химического анализа или
качественной пробы. Для этого испытывают стандартные образцы на разрыв при
температуре 550°С. Если относительное удлинение составляет более 5%, медь можно
применять для изготовления сварных конструкций ответственного назначения.
Режут металл на гильотинных ножницах или плазменной
дугой, а кромки под сварку разделывают механическим путем на строгальном или
фрезерном станке.
Перед сваркой поверхность меди тщательно очищают от
загрязнений металлической щеткой (до блеска) или промывают 10%-ным раствором
каустической соды. После чего выполняют обезжиривание бензином, уайт-спиритом
или другим растворителем.
Сварочную
проволоку перед
употреблением подвергают очистке травлением. Для этого применяют водный раствор
азотной кислоты (75 см3/л) или смесь серной и соляной кислоты в
соотношении 100:1 с последующей промывкой в воде, затем в щелочи, после чего
снова в чистой проточной воде. После промывки проволоку сушат горячим воздухом.
Медные электроды перед сваркой прокаливают, что снижает вероятность проявления
водородной болезни.
Сборка под
сварку. При
сборке под сварку тщательно подгоняют стык по всей длине в приспособлениях,
обеспечивающих надежное поджатие свариваемых кромок. Однако при этом должен
быть исключен натяг, вызывающий дополнительные напряжения в металле. Смещение
кромок и зазор между ними для большинства медных конструкций допускается не
более 10 % толщины свариваемого металла, но не более 2 мм.
В процессе сборки прихватки производят таким образом,
чтобы их высота не превышала 1/3 глубины разделки или катета шва. При сварке по
таким прихваткам образуется качественный сварной шов, не требующий подрубки
прихваток перед сваркой. Длина прихваток должна равняться толщине свариваемого
металла, а расстояние между ними не превышать L = (15...20)δ при толщине
свариваемого металла до 10 мм. При сварке меди большей толщины расстояние между
прихватками составляет L = (6...8)δ. Перед прихваткой свариваемый металл
предварительно подогревают. Зависимость температуры подогрева от толщины меди представлена
ниже.
Толщина меди, мм
6-10
10-20
20-40
40 и более
Температура нагрева,- °С
200-250
250-300
300-400
400-500
При охлаждении ниже 200°С и повторном предварительном
нагреве свариваемого изделия прихватки могут разрушиться, поэтому в перерывах
между технологическими операциями изделие не должно охлаждаться ниже
температуры 200-250°С.
Прихватки выполняют ручной дуговой сваркой покрытыми
электродами, ручной дуговой сваркой неплавящимся электродом в среде защитных
газов или полуавтоматической сваркой плавящимся электродом в среде защитных
газов. При ручной дуговой сварке прихватки выполняют на постоянном токе
обратной полярности.
Силу
сварочного тока выбирают по зависимости:
I=(60…70)dэ
где dэ – диаметр электрода, мм.
Для предупреждения проплавления металла, при
необходимости, с обратной стороны стыка устанавливают формирующие графитовые,
магнезитовые или медные водоохлаждаемые подкладки. В зависимости от
конструктивных особенностей свариваемых деталей можно применять остающиеся
подкладки в виде лент, полос или проволоки.
Механизированная сварка плавящимся
электродом (полуавтоматическая сварка) меди.
При сварке меди и ее сплавов основной трудностью
является получение сварных швов без пор, окисных включений и трещин.
Образование пор в металле шва может быть представлено зависимостью изменения
растворимости водорода в меди от содержания в ней кислорода. Согласно диаграмме
взаимной растворимости кислорода и водорода при снижении в металле кислорода
меньше определенного значения расплавленный металл склонен к активному
поглощению водорода. В этом случае в процессе сварки при высокой влажности
защитных газов и окружающего дугу воздуха, повышенном содержании водорода в
металле и электродной проволоке или их загрязнении .органическими веществами,
металл шва насыщается водородом.
Если содержание водорода в металле превышает его
растворимость, в процессе кристаллизации сварочной ванны образуется
перенасыщенный раствор водорода в меди, который приводит к образованию пор, а
при наплавке больших толщин металла и к трещинам. На поры и трещины такого
происхождения активные раскислители влияния не оказывают и не предотвращают их
образование. В целях борьбы с порами и трещинами такого происхождения в
активную зону дуги вводят небольшие доли кислорода.
Для получения металла шва высокого качества содержание
кислорода в смеси с инертными по отношению к меди газами должно быть
достаточным для полного связывания водорода в зоне дуги и предотвращения этим
попадания его в сварочную ванну, и недостаточным для образования в шве закиси
меди.
В случае если водорода в меди меньше критического
значения по диаграмме взаимной растворимости, медь может усваивать кислород в
значительных объемах. В этом случае водород, попадающий из зоны дуги в ванну,
восстанавливает закись меди. Образующиеся при этом в металле шва пары воды
способствуют образованию пор и трещин. В этом случае для борьбы с кислородом в
меди применяют активные раскислители: фосфор, марганец, кремний, титан,
цирконий и другие активные к кислороду элементы.
Для меди характерно отсутствие внутреннего окисления и
весьма интенсивное образование окислов на ее поверхности при высоких
температурах. Толщина образуемых окислов тем больше, чем выше температура
нагрева и больше при ней время выдержки. Поэтому нагрев меди в процессе сварки
и особенно предварительный ее подогрев приводят к окислению поверхности металла
с образованием закиси меди значительной толщины.
При нарушении технологии сварки расплавленный металл
затекает вперед движения дуги, заплавляя окислы меди на свариваемых кромках. В
этом случае окислы меди остаются в шве в виде неметаллических включений. В
зависимости от массы попавших в наплавленный металл окислов в швах образуются
несплавления или черноты, располагающиеся между швом и основным металлом или
между отдельными валиками или слоями.
Для предотвращения образования таких дефектов процесс
сварки в среде защитных газов выполняется таким образом, чтобы дуга частично
горела на расплавленном металле ванны, а часть дуги располагалась на окисленной
поверхности свариваемых кромок. Под воздействием температуры дуги окислы меди
на свариваемых кромках диссоциируют и в сварочную ванну не попадают.
Такая технология может быть выполнена только при
строгом соответствии требованиям силы тока, скорости подачи электродной
проволоки, ее диаметра, скорости сварки, напряжения на дуге, наклона электрода
и соблюдении других параметров режима и технологических приемов сварки.
В этом случае ручная дуговая сварка неплавящимся
электродом в среде защитных газов предпочтительна слева направо, а
полуавтоматическая сварка плавящимся электродом в газовой среде - справа
налево. При сварке неплавящимся электродом горелка должна располагаться для
сварки углом назад на 40-45° от металла, а присадочный металл подаваться с
хвостовой части ванны под углом 30-35° к свариваемому металлу. В процессе
полуавтоматической сварки угол наклона горелки от металла при расположении
углом вперед должен составлять 75-80°.
Так же располагается горелка или
электрод при автоматической сварке как в среде защитных газов, так и подслоем
флюса. Ввиду высокой тепло- и температуропроводности изделия из меди подвергают
предварительному подогреву и повышенной погонной энергии сварки. Температура
предварительного подогрева зависит от массы и химического состава свариваемого
изделия, условий сварки и ее погонной энергии, выдержки между наплавляемыми
валиками, применяемой защитной среды и других факторов. В процессе сварки
предварительно нагретое изделие остывает, а теплота, вводимая в процессе
сварки, способствует его восстановлению до заданной температуры. Такой
оптимальный вариант на практике встречается весьма редко.
При сварке изделий большой массы тепла дуги
недостаточно для поддержания заданной температуры нагрева. В этом случае
основной металл не смачивается наплавленным металлом и образуются несплавления
шва. Если температура нагрева изделия будет выше оптимальной, расплавленный
металл становится жидкотекучим и затекает вперед дуги. Это снижает глубину
проплавления и образует в шве наплывы и непровары. Для поддержания заданной
температуры в этом случае процесс сварки периодически прекращают, охлаждая
изделие до заданной температуры. Чтобы получить сварные швы высокого качества и
обеспечить необходимую производительность процесса, температура изделий при
сварке не должна отличаться более чем на ±50°С от оптимального значения. Такие
условия обеспечивают угол смачивания 70-90°, что позволяет получать высокое
качество сварных швов (см. рисунок 4).
Рисунок 4 - Влияние температуры предварительного подогрева на угол
смачивания при сварке меди
В зависимости от конструктивных особенностей
свариваемого изделия из меди технология сварки должна обеспечивать выполнение
всех сварочных операций не более чем за три- четыре предварительных подогрева
свариваемого изделия.
Если изделие остыло ниже температуры 100-150°С,
очередной предварительный подогрев его считают следующим циклом нагрева. При
несоблюдении таких условий в зоне сплавления и в сварных швах возможно
появление трещин, заметно снижаются также механические свойства сварных
соединений.
Горелки подогрева должны быть направлены на 70-100 мм
по обе стороны стыка, а их пламя при перемещении горелок не должно попадать на
кромки.
Для металла толщиной более 20 мм сварку начинают и
заканчивают на технологических планках размером 100×100 мм с формой разделки и
толщиной металла, соответствующей спариваемому металлу. Если предусмотрен
припуск на механическую обработку в начале и конце шва, технологические планки
можно не применять. При отсутствии технологических планок кратер в конце шва
заваривают без перемещения горелки вперед. В случае вынужденных перерывов
сварки кратер ранее выполненного шва после предварительной вырубки и зачистки
перекрывают на 15-30 мм. Допускается выплавка кратера дугой с последующей
беспрерывной его заваркой. Автоматическую и полуавтоматическую сварку меди и ее
сплавов в среде защитных газов производят плавящимся электродом, а
автоматическую и ручную дуговую сварку - неплавящимся электродом.
Дуговая сварка неплавящимся электродом применяется для
сварки меди толщиной до 10 мм. Медь большей толщины сваривают плавящимся
электродом автоматической или полуавтоматической сваркой. При автоматической
сварке меди и ее сплавов плавящимся электродом для защиты дуги используют
аргон, гелий или азот. Полуавтоматическая сварка применяется для сварки мелких
узлов, прихватки изделий перед сваркой, приварки технологических планок и
ремонта дефектных участков сварных швов.
При
неизменном режиме сварки (Iсв = 400...450 А, Uд = 32...34 В, Vcв = 14...16 м/ч,
температура предварительного подогрева меди 400-450°С) примесь к аргону азота
увеличивает глубину провара и массу ванны от 4 г при сварке в аргоне до 9 г при
сварке в азоте. Такое изменение состава защитной среды уменьшает удельную
энтальпию металла сварочной ванны от 2156×10-3 Дж/кг при сварке
в аргоне до 1960х10-8 Дж/кг при сварке в азоте. Добавка к аргону гелия повышает
массу ванны до 6 г, а удельная энтальпия ее по сравнению с защитой дуги аргоном
уменьшается до 2055×10-3Дж/кг.
Таким образом, при неизменных параметрах режима
тепловложение в металл ванны составляет (Дж) в аргоне 3684,4, в гелии 5275,4 и
в азоте 7536,2. Приведенные данные показывают, что с энергетической стороны в
качестве защитной среды лучше применять азот, затем гелий и аргон. В результате
более высокого тепловложения в металл при сварке меди в среде азота
увеличивается глубина провара, что позволяет снизить температуру
предварительного подогрева свариваемых изделий и повысить эффективный КПД
процесса.
Для получения сварных швов без пор и других дефектов к
защитным газам добавляют небольшие доли кислорода. Кислород, поступающий в зону
дуги с защитным газом, расходуется на потери в окружающее пространство, на
взаимодействие с водородом диссоциации влаги защитного газа и окружающего
воздуха, на взаимодействие с водородом, поступающим в зону дуги с электродным и
свариваемым металлом, на окисление свариваемого металла и его легирующих
добавок, на образование озона и других химических соединений.
Водород, находящийся в атмосфере дуги, взаимодействует
с кислородом смеси в первую очередь, а оставшийся после этого кислород
затрачивается на окисление металла. Поэтому добавка кислорода, необходимая для
взаимодействия с водородом в зоне дуги и устранения этим причин образования пор
в металле шва, считается полезной и не должна превышать допустимых норм.
Смеси
защитных газов, удовлетворяющие таким требованиям:
Ar + до 2% O2;
N2 + до 4% O2;
He + до 2% O2;
25-35% He + до 4% O2 + Ar остальное;
25-35% N2 + до 4% O2 + Ar остальное.
Механизированная
сварка плавящимся электродом (полуавтоматическая сварка) выполняется на постоянном токе
обратной полярности. Режимы полуавтоматической сварки приведены в табл /p/pице
2.
Таблица 2 -
Режимы механизированной сварки плавящимся электродом (полуавтоматческой сварки)
меди
Диаметр сварочной проволоки, мм
Сила сварочного тока, А
Напряжение на дуге, В
1,2
140-160
20-22
1,6
200-240
22-24
2,0
280-340
26-28
Изучить: 1. Сварочная характеристика меди.
2.Подготовка
материала к сварке.
3. Особенности сварки меди.
15.02.2022
группа: 412
Предмет: Техника и технология частично механизированной сварки (наплавка) плавлением в защитном газе.
Тема урока: Характеристика среднелегированных и высоколегированных сталей. Особенности технологии сварки (наплавки).Сварка
углеродистых сталей
Углеродистая сталь – сплав железа и углерода с
незначительным содержанием полезных примесей: кремний и марганец, вредных
примесей: фосфор и сера. Концентрация углерода в сталях данного типа составляет
0,1-2,07%. Углерод выступает в качестве основного легирующего элемента. Именно
он определяет сварочно-механические свойства этого класса сплавов.
В зависимости от величины содержания углерода
выделяют следующие группы углеродистых сталей:
менее 0,25% – низкоуглеродистые;
0,25-0,6 % – среднеуглеродистые;
0,6-2,07 % – высокоуглеродистые.
Потребность в высокоуглеродистых сталях возникает
при проведении ремонтных работ, при производстве пружин, режущих, бурильных,
деревообрабатывающих и других инструментов, высокопрочной проволоки, а также в
тех изделиях, которые должны обладать высокой износостойкостью и прочностью.
Технология
сварки высокоуглеродистых сталей
Сваривание возможно, как правило, с предварительным
и сопутствующим подогревом до 150-400°С, а также последующей термообработкой.
Обусловлено это склонностью данного типа сплавов к хрупкости, чувствительностью
к горячим и холодным трещинам, химической неоднородностью шва.
К
сведению! Исключения возможны, если использовать специализированные электроды
для разнородных сталей.
После подогрева необходимо произвести отжиг, который
нужно проводить до тех пор, пока изделие не остынет до температуры 20°С.
Важным условием является недопустимость
осуществления сварки на сквозняках и при температуре окружающей среды ниже 5°С.
Для повышения прочности соединения необходимо
создавать плавные переходы от одного до другого свариваемого металла.
Хорошие результаты достигаются при сваривании узкими
валиками, с охлаждением каждого наплавленного слоя.
Исполнителю следует также соблюдать правила,
предусмотренные для соединения среднеуглеродистых сплавов.
Особенности
сварки высокоуглеродистых сталей
Рабочую поверхность необходимо очистить от
загрязнений различного рода: ржавчина, окалина, механические неровности и
грязь. Присутствие загрязнений может привести к образованию пор.
Охлаждать конструкции из высокоуглеродистых сталей
нужно медленно, на воздухе, для нормализации структуры.
Предварительный подогрев ответственных изделий до
400°С позволяет достичь необходимого показателя прочности.
Виды
сварки высокоуглеродистых сталей
1. Оптимальным вариантом проведения сварочного
процесса является ручная дуговая сварка с помощью покрытых электродов. Работа с
высокоуглеродистыми сталями обладает большим количеством специфических
характеристик. Поэтому сварка высокоуглеродистой стали проводится специально
разработанными электродами, например, НР-70. Сваривание осуществляется
постоянным током обратной полярности.
2. Сварка под флюсом также используется для
соединения сплавов данного типа. Равномерно покрыть флюсом рабочую зону в
ручном режиме довольно сложно. Поэтому, в большинстве случаев, используется
автоматическая технология. Расплавленный флюс образует плотную оболочку и
предотвращает воздействие вредных атмосферных факторов на сварочную ванну. Для
сваривания под флюсом используются трансформаторы, выдающие переменный ток.
Данные аппараты позволяют создавать устойчивую дугу. Главное достоинство
данного метода – небольшие потери металла вследствие малого разбрызгивания.
Важно отметить, что не рекомендуется применять метод
газовой сварки. Процесс характеризуется выгоранием большого количества
углерода, в результате чего образуются закалочные структуры, которые
отрицательно сказываются на качестве шва.
Однако, если свариванию подвергаются рядовые конструкции,
то применение данного способа возможно. Соединение производится на нормальном
или незначительном пламени, мощность которого не превышает 90 м3 ацетилена в
час. Изделие нужно подогреть до 300°С. Сварка осуществляется левым способом,
что дает возможность уменьшить время нахождения металла в расплавленном
состоянии и продолжительность его перегрева.
Сварка
углеродистой стали
Сварка коррозионностойких и углеродистых сталей
является ярким примером соединения разнородных материалов.
Предварительный и сопутствующий нагревы изделий до
температуры примерно в 600°С позволят получить шов с более однородной
структурой. После работ нужно произвести термическую обработку, это поможет
избежать образование трещин.
Для сваривания нержавейки и низкоуглеродистых сталей
на практике применяются два метода, которые подразумевают использование
сварочных стержней:
электроды из высоколегированной стали или электроды
на никелевой основе заполняют сварочный шов;
кромки изделия из низкоулегродистой стали наплавляется
легированными электродами, затем плакированный слой, кромки из нержавейки
свариваются специальными электродами для нержавейки.
Сварку нержавеющих и углеродистых сталей также можно
проводить аргонодуговым методом. Однако, такая технология используется крайне
редко и только для работы с особо ответственными конструкциями.
Также исполнитель может произвести соединение
методом полуавтоматической сварки с помощью металлического электрода в защитной
среде инертных газов.
Изучить: 1. Технология сварки
высокоуглеродистых сталей.
2. Особенности сварки высокоуглеродистых сталей.
3. Сварка углеродистой стали.
15.02.2022
группа: 412
Предмет: Техника и технология ручной дуговой сварки (наплавка, резка) неплавящимися электродами в защитном газе.
Тема урока: Подготовка к сварке. Выбор режимов сварки деталей из алюминиевых сплавов. Подготовка к сварке
Резку и подготовку кромок деталей из алюминия и его
сплавов следует вести механическими способами
Стыковое соединение металла разной толщины
Конструктивные элементы подготовки кромок (размеры
приведены в мм)
Конструктивные элементы подготовки кромок при сварке
со сквозным проплавленнем н формированием шва на весу
При сварке за один проход может возникнуть надрез
корня шва
При снятии фаски с обратной стороны стыкуемых кромок
надрез не возникает. Для снятия фасок можно использовать напильник
Свариваемые поверхности тщательно очищают от смазки,
на ширине 100-150 мм от кромок обезжиривают ацетоном, уайт-спиритом или другим
растворителем.
Пленку окиси алюминия удаляют механически или
химическим травлением.
При механической обработке (непосредственно перед
сваркой) кромки зачищают на ширину 25-30 мм абразивной бумагой, шабером или
щеткой из нержавеющей проволоки диаметром не более 0,15 мм.
Химическое травление проводят в течение 0,5-1 мин в
растворе, состоящем из 50г едкого натра и 45г фтористого натрия на 1 л воды.
После травления поверхность промывают проточной водой, а затем осветляют в
30-35%-ном растворе азотной кислоты (для алюминия и сплавов типа АМц) или в
25%-ном растворе ортофосфорной кислоты (для сплавов типа АМг и В95). После
повторной промывки поверхность сушат до полного испарения влаги.
Алюминиевую сварочную проволоку перед сваркой тоже
обрабатывают. Сначала ее обезжиривают, а затем подвергают травлению в 15%-ном растворе
едкого натра в течение 5-10 мин при 60-70°С. после чего следует промывка в
холодной воде и сушка при температуре 300°С в течение 10-30 мин.
Подготовленные к сварке материалы сохраняют свои
свойства 3-4 дня. Позже на поверхности вновь образуется окисная пленка.
Детали из алюминия и его сплавов собирают в
приспособлениях или на прихватках, выполняемых аргонодуговой сваркой
W-электродом. Расстояние между прихватками должно быть не более 150-180 мм.
Поверхности прихваток непосредственно перед сваркой зачищают
металлическими щетками. Обнаруженные дефектные прихватки удаляют, и стыки
прихватывают повторно. При сварке прихватки полностью переплавляют.
Выбор параметров режима
Сварку ведут на постоянном токе обрат ной полярности.
Защитным газом служит apгон или гелий и их смеси. Непосредственно перед сваркой
кромки обезжиривают .
Диаметр сопел горелок выбирают равным не менее 18-22
мм.
Длина дуги должна составлять 2-6 мм, а сварочный ток -
быть больше, чем при ручной аргонодуговой сварке W-электродом. Сварку выполняют
за один проходили двусторонними швами.
Процесс
сварки может быть: импульсно-дуговым (ИДС), струйным (СТР) или с короткими
замыканиями дуги (КЗ).
Ориентировочные режимы
Вид соединения
Размеры, мм
Процесс сварки
Газ
Сварочный ток, А
Напряжение на дуге, В
Скорость сварки, м/ч
Диаметр электрода , мм
Вылет электрода, мм
Расход газа, л/мин
S
b
2,5-3
0+0,5
ИДС
Ar
40-80
15-18
35-45
1,2
10-13
7-9
4
0+0,5
ИДС
ИДС
СТР
Ar
Не
Ar
80-130
120-160
150-220
18-20
24-26
23-24
30-40
15-50
45-70
1,4-1,6
13-18
8-10
45-50
10-20
6
0+1
ИДС
ИДС
СТР
Ar
Не
Ar
180-250
180-200
200-320
23-26
25-30
23-30
20-35
25-45
25-35
1,6-3
1,6-2
1,6-2
15-30
15-25
15-25
12-14
45-50
12-18
8-10
0+1
0+4
ИДС
СТР
СТР
Ar
Ar
Не
250-320
250-400
250-320
25-30
25-33
32-36
20-35
25-45
25-35
1,6-3
1,6-4
1,6-2
15-40
15-25
12-20
14-25
60-70
12-16
0+4
0+1,5
0+1,5
СТР
Ar
Ar
Не
Не+Ar
320-420
400-500
280-360
300-450
26-28
28-35
34-36
30-34
20-30
25-35
20-25
20-25
2
4
2-3
4
18-25
25-40
26-30
25-40
20-25
20-25
60-80
70-80
20-30
0+1,5
СТР
Ar
Не+Ar
Не
310-550
300-500
280-360
26-35
30-35
34-36
18-20
18-25
20-25
2-4
2-4
2-3
20-40
20-40
20-30
18-25
60-80
70-80
2,5-3
0+0,5
ИДС
ИДС
КЗ
СТР
Ar
Не
Не
Ar
60-100
80-100
90-120
90-120
16-18
17-19
16-17
17-19
35-40
35-45
40-45
40-45
1-1,4
1-1,2
0,8-1,2
0,8-1,2
10-15
6-8
35-40
35-40
6-9
4-5
0+0,5
ИДС
СТР
ИДС
Аг
Аг
Не
120-220
150-220
150-200
18-22
19-22
25-30
25-35
25-35
25-40
1,2-1,6
1,2-1,4
1,2-1,6
12-18
12-15
12-18
10-12
10-12
35-40
8 и более
0+1
СТР
Аг
Не
280-330
280-320
27-29
32-35
20-25
20-25
1,6
1,6
18-30
18-25
20-25
45-60
Техника сварки
При сварке алюминия и его сплавов необходимо
использовать чистые и сухие перчатки из спилка или из другого подобного
материала
Механизированную сварку стыковых соединений без
разделки кромок в нижнем и вертикальном положениях выполняют обычно без
поперечных колебаний электрода
При наличии разделки кромок первый шов выполняют также
без поперечных колебаний, а последующие - с небольшими (до 5 мм) перемещениями
электрода
При сварке угловых швов в нижнем
положении угол наклона горелки относительно вертикальной стенки - 30-
45°.
Угловой шов на вертикальной плоскости ведут снизу-вверх "углом
вперед". Однопроходную сварку
выполняют с перемещениями конца электрода.
Угловые швы больших сечений на вертикальной плоскости
делают многопроходными
путем выполнения узких швов. Так же
сваривают и стыковые горизонтальные швы
Изучить: 1. Подготовка металла к сварке.
2. Выборы
параметров сварки.
3. Техника
сварки.
15.02.2022
группа: 412
Предмет: Техника и технология ручной дуговой сварки (наплавка, резка) неплавящимися электродами в защитном газе.
Тема урока: Сварочные материалы для ручной дуговой сварки (наплавка, резка) неплавящимися электродами в защитном газе деталей из алюминия. Расход сварочных материалов. Сварочные
материалы для ручной дуговой сварки неплавящимися электродами в защитном газе деталей из
алюминия.
группа: 412
Предмет: Техника и технология ручной дуговой сварки (наплавка, резка) неплавящимися электродами в защитном газе.
Тема урока: Технология сварки меди и ее сплавов. Трудности при сварке меди.
В 1991 году изобретена и впервые опробована технология Friction stir welding (сварка трением с перемешиванием). С помощью данной технологии создают прочное неразъёмное соединение любых цветных металлов, включая трудносвариваемые алюминий, магний, титан и высоколегированные стальные сплавы.
Преимущества
перед сваркой плавлением делают FSW востребованным методом в автомобильной
промышленности, на производстве ракетоносителей, самолетов, поездов и т.д.
Все бы хорошо, но даже сварка меди обойдётся минимум в 600 тысяч евро. Такое оборудование вряд ли доступно рядовому сварщику автосервиса или домашнему мастеру.
Что же делать? Прибегнуть к старому доброму аргонодуговому способу (TIG), который при должном опыте позволит добиться отличного результата в работе с цветными металлами.
Как выполняется аргонодуговая сварка меди: правила, принципы и особенности технологии
Сегодня
разработаны и активно используются несколько технологий для образования
неразъёмного соединения медных деталей. Метод сварки меди аргоном считается
одним из самых эффективных. Соединение заготовок в среде инертного газа
позволяет работать с крупными и мелкими частями с образованием надёжного шва.
Температура плавления меди и её сплавов достаточно низкая. Чистый металл переходит в жидкое состояние при 1083 0С, бронза при 950 0С. Это создаёт некоторые сложности при работе с расплавом. Для тонких деталей высока вероятность прожига, в толстостенных заготовках металл быстро становится текучим и выплёскивается из ванны.
Высокая теплопроводность (в 2 раза выше в сравнении с алюминием) требует предварительного прогрева заготовок до температуры 350–600 0С с помощью газовой горелки. Приём снижает риски возникновения дефектов в месте контакта частей. Температура подбирается опытным путём в зависимости от толщины кромок и чистоты основного металла.
Сварку выполняют вольфрамовым электродом. Неплавящийся рабочий инструмент хорошо проваривает металл с образованием ровного и прочного шва. В линейке различают две марки:
·
ЭВЛ: лантанированные
элементы производят с добавлением оксида лантана 1,1–1,4%. Считается
универсальным рабочим инструментом для сварки аргоном.
· ЭВИ: итерированные электроды относятся к одним из самых стойких в ряду неплавящихся. Их применяют для самых ответственных участков сварки. В качестве добавки к вольфраму используют 1,8–2,2% оксида иттрия — соединение улучшает стабильность катодного пятна на участке поджига дуги, что в конечном итоге повышает её стабильность в расширенном интервале рабочих токов.
Сварка меди аргоном выполняется с использованием ЭВИ–электродов на постоянном токе. Среда защитного газа необходима, чтобы убрать процесс образования оксида меди в реакции взаимодействия с кислородом воздуха. В отличие от чистого металла диоксид относится к тугоплавким соединениям (1380 0С). Его образование затрудняет сварку и ухудшает качество шва.
Использование аргона
Подготовка металла
Для изделий толщиной в пределах 5–12 мм подходит метод односторонней
разделки. Угол скоса зависит от следующих критериев:
·
Толщины
свариваемых заготовок: чем больше параметр, тем шире должен быть угол открытия.
·
Диаметра
электрода: для стержня необходимо обеспечить достаточный доступ к корню шва.
·
Метода
работы: для сварки меди в среде аргона достаточно обеспечить угол 40–50 0С.
Заготовки
толщиной более 12 мм разделывают по каждой из сторон.
Режим аргонодуговой сварки.
Настройки
под аргонодуговой аппарат подбирают к толщине свариваемых деталей и в
зависимости от диаметра используемого электрода:
Толщина медных кромок, мм |
Ø электрода, мм |
Сварочный ток, А |
Расход защитного газа, л/мин |
1,2 |
2,5–3,0 |
120–130 |
От 7 до 8,5 |
1,5 |
2,5–3,0 |
140–150 |
От 7 до 8,5 |
2,5 |
3,5–4,0 |
220–230 |
От 7,5 до 10 |
3,0 |
3,5–4,0 |
230–240 |
От 7,5 до 10 |
Кроме неплавящихся вольфрамовых электродов аргоновая сварка меди ведётся с использованием присадочной проволоки. Расходник помогает устранить небольшое количество кислорода, которое всё–таки проникает в сварочную зону.
Желательно
выбирать проволоку, близкую по составу к свариваемому металлу. Обычно берут
материал с включением марганца. Добавка эффективно связывает проникающий
кислород, устраняя появление тугоплавкого оксида. Вместе с тем включения
марганца ухудшают качество шва, снижая однородность и прочность соединения. Для
того чтобы улучшить результат сварки, желательно использовать проволоку с
добавками редкоземельных элементов. Материалы, также как и марганец, полностью
удаляют кислород из сварочной зоны, но при этом сами не остаются в сварном шве.
Плохо то, что это один из самых дорогих расходников, применение которого для
бытовых операций, как правило, не оправданно.
В домашней
практике часто используют обычные медные провода, тщательно зачищая поверхность
от защитного лака и обезжиривая. Желательно, чтобы температура плавления
расходника была немного ниже, чем у соединяемого металла.
Полезные советы для сварки меди аргоном
·
Толстостенные
детали (более 12 мм) можно сваривать без присадочной проволоки за счёт
наплавления металла заготовок.
·
В процессе работы
горелку следует вести плавно зигзагами, заходя поочерёдно на одну и другую
сторону линии соединения. Приём позволяет выполнить расплавление более
равномерно, что улучшает качество шва.
·
Тонкие
детали сваривают прерывистым укороченным шагом — способ позволяет избежать
прожога материала.
·
На концевых
участках ванны используют функцию заварки кратера. Если опция не предусмотрена
в аппарате, дугу плавно отводят вручную, используя метод постепенного
удлинения.
·
Присадочную
проволоку всегда располагают перед горелкой.
·
Медные трубы
сваривают прерывистым швом на небольших токах.
Технология
аргонодуговой сварки позволяет выполнять соединение как в вертикальном, так и в
горизонтальном направлении. Техника работы и подбор сварочных токов осваиваются
на опыте, поэтому при недостатке навыка желательно попрактиковаться на ненужных
частях и только после этого приступать к сварке ответственных деталей.
Изучить: 1. Процесс
выполнения сварки меди.
2. Подготовка металла к сварке.
3. Режимы сварки.
группа: 412
Предмет: Техника и технология ручной дуговой сварки (наплавка, резка) неплавящимися электродами в защитном газе.
Тема урока: Техника сварки деталей из алюминиевых сплавов.
Способы
сварки алюминия и его сплавов.
Для алюминия
и его сплавов возможно применение почти всех промышленных способов сварки
плавлением и давлением. Ручную дуговую сварку покрытыми электродами в настоящее
время используют редко, хотя она в принципе возможна. Наибольшее
распространение для изготовления сварных конструкций приобрела дуговая сварка в
инертных газах. Автоматическую дуговую сварку с использованием флюсов применяют
для крупногабаритных конструкций, электрошлаковую - для металла больших толщин.
Для получения сварных швов с высокими механическими характеристиками используют
также электроннолучевую и лазерную сварку.
Дуговая
сварка в среде инертных газов наиболее распространена при изготовлении конструкций
из алюминиевых сплавов ответственного назначения. Осуществляется как
неплавящимся вольфрамовым электродом, так и плавящимся. Используемые инертные газы:
аргон высшего и первого сорта по ГОСТ 10157-79, гелий высокой чистоты и смесь
аргона с гелием. Выбор конкретного способа сварки определяется толщиной
металла, конструкцией изделия и масштабом производства.
Дуговая
сварка неплавящимся вольфрамовым электродом. В качестве неплавящегося электрода применяют
вольфрам с добавками лантана, иттрия и других элементов. Использование чистого
вольфрама не рекомендуется. Отмеченные примеси придают электроду повышенную
стойкость, обеспечивают большую плотность тока и другие преимущества.
Питание дуги
осуществляется от источника переменного тока, что обеспечивает разрушение
оксидной пленки за счет эффекта катодного распыления. Использование дуги
переменного тока связано с тем, что при сварке постоянным током обратной полярности
из-за возможного расплавления вольфрамового электрода допустим сварочный ток
небольшой величины, а при сварке постоянным током прямой полярности затруднено
удаление оксидной пленки.
Сварку
вольфрамовым электродом выполняют вручную, механизировано или автоматически.
При сварке в среде гелия напряжение повышается на 7... 10 В, при этом дуга
укорачивается, а сила тока снижается на 10... 15 %. Расход газа при
использовании гелия увеличивается в
1,8...2,2
раза. Ручная сварка ведется на меньших значениях тока в один или несколько
проходов в зависимости от толщины.
Дуговая
сварка вольфрамовым электродом в среде инертных газов является наиболее
универсальным способом сварки, который позволяет выполнять сварку в различных
пространственных положениях и труднодоступных местах. При этом достигается
высокая прочность и пластичность сварных соединений, близкие к прочности и
пластичности основного металла.
Сварка
вольфрамовым электродом диаметром 2...6 мм целесообразна для узлов алюминия и
его сплавов толщиной до 12 мм. Металл толщиной до 3 мм сваривают за один проход
на стальной подкладке; при толщине металла 4...6 мм сварку выполняют с двух
сторон, а начиная с толщины 6...7 мм применяют разделку кромок (V- или
Х-образную). Соединение с отбортовкой кромок целесообразно для металла толщиной
0,8...2 мм. Присадочный металл выбирают в зависимости от марки сплава: для
технического алюминия - проволоку марок АО, АД или АК, для сплавов типа АМг -
проволоку той же марки, но с
увеличенным
(на 1___1,5 %) содержанием магния для компенсации его
угара.
Диаметр проволоки составляет 2...5 мм. Рекомендуемые режимы ручной сварки
приведены в табл. 14.
Рекомендуемые
режимы ручной дуговой сварки вольфрамовым электродом
Таблица 14
Толщина
металла, мм |
Диаметр,
мм |
Сила тока,
А |
||
вольфрамового электрода |
присадочной проволоки |
в аргоне |
в гелии |
|
1...2 |
2 |
1...2 |
50...70 |
30...40 |
3...4 |
3 |
2...3 |
100...130 |
60...90 |
4...6 |
4 |
3 |
160... 180 |
ПО...130 |
6...10 |
5 |
3...4 |
220...300 |
160...240 |
11...15 |
6 |
4 |
280...360 |
220...300 |
Для
обеспечения надежной газовой защиты в зависимости от режима сварки
устанавливают оптимальный расход газа (от 4 до 12 л/мин при ручной сварке и до
30 л/мин при автоматической). Чрезмерный расход газа приводит к его
турбулентному истечению и засасыванию воздуха в зону дуги, т. е. к нарушению
газовой защиты, а при малом истечении газа (или чрезмерно большой скорости
сварки) защита зоны сварки будет недостаточной. Подачу защитного газа включают
с помощью аппаратуры управления за 3...5 с до возбуждения дуги, а выключение
подачи - через 5...7 с после обрыва дуги.
При
выполнении сварки алюминия и его сплавов вручную особое внимание уделяется
технике сварки. Угол между присадочной проволокой и электродом должен быть
примерно 90°. Присадка подастся короткими возвратно-поступательными движениями.
Недопустимы поперечные колебания вольфрамового электрода. Длина дуги -
1,5...2,5 мм. Вылет электрода от торца наконечника горелки - 1___1,5 мм. Сварку
обычно ведут справа налево («левый» способ), чтобы снизить перегрев свариваемого
металла.
Для сварки
алюминия и его сплавов малых толщин целесообразно применять импульсную дугу
переменного тока. При ее использовании удается сваривать алюминиевые сплавы
толщиной от 0,2 мм. Стыковые соединения металла толщиной 0,2... 1 мм сваривают
на стальных подкладках с формирующей канавкой, используя присадочную проволоку
диаметром 0,6...0,8 мм. При этом коробление изделия снижается на
40.. . 60%.
Сварка
плавящимся электродом. Плавящийся электрод применяют при дуговой сварке алюминиевых сплавов
толщиной более 4 мм. Сварку выполняют на постоянном токе обратной полярности
при силе тока, обеспечивающей струйный перенос электродного металла, проволокой
1.5.. .2.5
мм. В связи с недостаточно высокой жесткостью алюминиевой проволоки сварка
проволокой диаметром менее 1,2... 1,5 мм затруднительна. Сварку ведут в чистом
аргоне либо в смеси аргона и гелия (до 70 % Не). При этом газовую смесь
предпочитают при сварке металла больших толщин.
Изучить: 1. Процесс сварки алюминия.
2. Режимы
сварки алюминия.
3. Сварка алюминия плавящимся электродом.
группа: 412
Предмет: Техника и технология частично механизированной сварки (наплавка) плавлением в защитном газе.
Тема урока: Характеристика алюминиевых, никелевых, титановых сплавов. Особенности технологии сварки (наплавки).
Характеристика
алюминиевых, никелевых, титановых сплавов.
Сварка
алюминиевых и магниевых сплавов. Наличие оксидной пленки на поверхности алюминия
препятствует сплавлению свариваемых кромок между собой, а также основного и
присадочного металлов. Для предотвращения попадания оксидной пленки в сварной
шов необходимо перед сваркой удалять оксидную пленку химическими растворителями
с поверхности основного и присадочного металлов.
Вследствие
высокой теплопроводности и теплоемкости металла следует использовать для
сварки алюминиево-магниевых сплавов мощные источники теплоты с
высокой степенью концентрации тепловой энергии. Высокий коэффициент линейного
расширения сплавов способствует короблению изделий при нагреве. Сварку
конструкций из алюминиево-магниевых сплавов нужно вести в жестких зажимных
приспособлениях - кондукторах.
Сварку
конструкций выполняют покрытыми электродами, по слою флюса, в защитных газах
неплавящимся или плавящимся электродами, а также можно применять электрошлако-
вую сварку. Сварку покрытыми электродами выполняют при толщине металла менее 4
мм. При сварке неплавящимся электродом уровень качества сварного соединения
выше, чем при сварке плавящимся электродом, но при этом производительность
процесса сварки ниже.
Сварка
титановых сплавов. Вследствие
малой теплопроводности титановых сплавов на образование сварного соединения
требуется меньшее количество теплоты, чем при сварке малоуглеродистой стали.
Параметры режима сварки титановых сплавов близки к параметрам режима сварки
аустенитных сталей. Титановые сплавы немагнитны, поэтому нет опасности
магнитного дутья, но в то же время для сварки нельзя применять магнитные
стенды. В расплавленном состоянии титановые сплавы имеют высокую жидкотекучесть
и обладают высоким коэффициентом поверхностного натяжения, поэтому сварные
соединения склонны к прожогам. К сборке стыков из титановых сплавов предъявляют
более жесткие требования, чем при сварке других конструкционных материалов.
В связи с
высокой химической активностью титана при повышенных температурах и особенно в
расплавленном состоянии основной трудностью при сварке плавлением является
обеспечение надежной защиты от атмосферы не только сварочной ванны и корня шва,
но и остывающих участков сварного соединения, нагретых до температуры свыше 350
°С. Сварные конструкции обычно изготавливают дуговой сваркой в защитных
инертных газах.
В
зависимости от конфигурации и размеров свариваемых узлов применяют три типа
защиты зоны сварки инертным газом:
- ? общую защиту в камере с
контролируемой атмосферой;
- ? защиту только сварного
соединения с использованием местных камер;
- ? струйную защиту зоны сварки,
осуществляемую непрерывным обдуванием сварочной ванны и остывающих
участков сварного соединения перемещением сварочной горелки.
Камеры с
контролируемой атмосферой обеспечивают наиболее надежную защиту сварного
соединения. Применение таких камер особенно целесообразно в серийном
производстве в том случае, когда конструкция имеет сложную конфигурацию, а швы
располагаются в труднодоступных местах. Сварку в камерах выполняют вручную и в
автоматическом режиме, при этом сварщик может находиться как вне камеры, так и
в ней в специальном скафандре. Камеры с размещенными в них деталями,
подлежащими сварке, сначала вакуумиру- ют, а затем заполняют инертным газом.
Местные
защитные камеры используют с предварительным вакуумированием или без него. В
последнем случае вытеснение воздуха обеспечивается продувкой такой камеры
5-10-кратным объемом инертного газа. Разновидностью местных защитных камер
являются накидные малогабаритные камеры. Такие камеры предназначены, главным
образом, для автоматической сварки неповоротных стыков трубчатых конструкций.
Наибольшее
распространение имеет сварка неплавящимся электродом на воздухе. Для
обеспечения надежной защиты зоны сварки разработаны специальные горелки с
соплами с удлиненной насадкой, подкладки и другие приспособления. Аргонодуговую
сварку выполняют на постоянном токе прямой полярности.
Для сварки
титановых сплавов малой толщины (менее 1,5-2 мм) находит применение
импульсно-дуговая сварка неплавящимся электродом. При этом снижается перегрев
металла, уменьшаются сварочные деформации и несколько повышается пластичность
швов. Для сварки титановых сплавов толщиной более 3 мм можно применять сварку
под слоем флюса. Сварку ведут на остающейся металлической подкладке, на медной
технологической подкладке или на флюсовой подушке. Высокое качество сварки
титана и его сплавов обеспечивает применение электронно-лучевой сварки и
дуговой сварки в вакууме.
Трудности полуавтоматической сварке титана.
Титан и его сплавы обладают высокой химической активностью,
что обусловливает необходимость предохранения от окисления даже участков
околошовной зоны при нагревании до 250-300 градусов. Поскольку в околошовной
зоне часто наращивается зерно, необходимо выбирать подходящий токовый режим.
Газовые примеси (в первую очередь, водорода),
растворенные в основном и присадочных металлах, вызывают образование пор и
холодных трещин.
Из-за низкой вязкости расплавленного металл велик
риск образования прожогов.
Подготовка к полуавтоматической сварке.
Раскрой на заготовки
и подготовка кромок чаще всего проводятся механическими способами. Если изделия
являются толстостенными, можно провести разделительную резку и подготовку
кромок газотермическими методами, но затем надо обязательно обработать кромки
механически на глубину как минимум 3-5 мм. Для зачистки кромок на ширину 15-20
мм используются металлические щетки, шаберы и прочие приспособления.
Обязательным является последующее обезжиривание кромок. Если перед сваркой
проводилась вальцовка, ковка, штамповка или другие виды термообработки,
необходимо очистить поверхности гидропескоструйным или дробеструйным аппаратом
(подробнее см. Очистка поверхности металла перед сваркой). После этого они
подвергаются химической обработке: рыхлению оксидной пленки; травлению;
осветлению.
После того, как свариваемая поверхность химически
обработана, свариваемые кромки на 20 мм промываются бензином и протираются
ацетиленом или этиловым спиртом. Сварочная пленка на предварительном этапе
подвергается вакуумному отжигу, а затем – обезжириванию Сварка проводится в
специальных приспособлениях, либо на прихватках, выполненных ручной
аргонодуговой сваркой W-электродом. Когда свариваемые поверхности уже готовы к
работе, к ним нельзя прикасаться незащищенными руками.
Выбор режимов
полуавтоматической сварки титана.
При
полуавтоматической сварке титана используется постоянный ток обратной
полярности. При выборе режимов учитывается толщина металла, склонность сплава к
росту зерна и подверженность термическому циклу. Чтобы максимально уменьшить
рост зерна, стоит выбирать режимы с повышенными скоростями и незначительной
погонной энергией. Поскольку титан имеет высокое электрическое сопротивление,
сварка проводится с небольшими вылетами электрода. Однако при работе с
использованием невысоких токовых режимов есть риск непровара корня шва. Чтобы
избежать этого, корень стоит выполнить ручной аргонодуговой сваркой
W-электродом, а остальную разделку – сваркой плавящимся электродом. Основное
положение – нижнее. Если используется сварка с глубоким проплавлением на
повышенных токовых режимах, необходимо использовать гелиево-аргоновую газовую
смесь (80% + 20%). Для увеличения пластичности, прочности и устойчивости к
образованию трещин сварочные швы требуют дополнительной термической обработки,
выбрав режим в зависимости от состава сплава.
Техника
полуавтоматической сварки титана.
При механизированной
сварке титана плавящимся электродом в инертных газах особые сложности связаны с
обеспечением надежной защиты зоны нагрева. Поэтому, если применяется этот метод
сварки, работа проводится в специальных камерах, где контролируется атмосфера.
Сварка в монтажных условиях проводится импульсно-дуговым способом, что
обеспечивает более высокую производительность, чем альтернативный вариант –
ручная сварка неплавящимся электродом при одновременном снижении погонной
энергии в 2-2,5 раза. В некоторых случаях используется вакуумная сварка титана
и его сплавов, главным преимуществом которой является чистота металла шва, в
котором не образуются примеси из неметаллических элементов и газов. Режим
сварки и ее техники необходимо выбрать так, чтобы обеспечить устойчивое горение
дуги с минимумом разбрызгиваний. Для этого необходим струйный перенос
электродного металла. Важно выбрать оптимальное соотношение сварочного тока,
скорости подачи электродной проволоки, дугового напряжения и вылета электрода.
Газовая защита.
Одним из важнейших
условий получения качественного соединения при сварке титановых сплавов
является обеспечение надежной газовой защиты: сварного шва; участков основного
металла, которые нагреты до 250-300 градусов. Можно выбрать один из трех
вариантов газовой защиты: струйная – с задействованием специальных
приспособлений; местная – в герметичных камерах малого объема; общая – в
камерах с контролируемой атмосферой (УБС-1, ВКС-1, ВУАС-1).
Рис. 1 Защитная камера для сварки титана Дополнительные
защитные устройства изготавливаются из нержавеющей стали. Необходимо, чтобы
были предусмотрены газовые линзы и рассекатели. К газовой горелке прикрепляется
специальная насадка для защиты кристаллизующейся сварочной ванны. Ее ширина
должна быть 40-50 мм, а длина – 60-120 мм в зависимости от режима сварки. При
сварке кольцевых поворотных и неповоротных стыков, а также трубчатых
конструкций используются местные или малогабаритные камеры.
Рис. 2. Вспомогательное оборудование для защиты зоны сварки
Качество защиты можно определить по внешнему виду металла шва. Если его
поверхность является серебристой или светло-желтой, защиту можно считать
достаточной. Сварной шов желто-голубого цвета свидетельствует о нарушениях
защиты, хотя в некоторых случаях такие швы вполне допустимы. О некачественном
шве свидетельствует синевато-серый и темно-синий цвет.
Изучить: 1. Характеристика
цветных сплавов.
3. Газовая защита сварочной ванны.
группа: 412
Предмет: Техника и технология частично механизированной сварки (наплавка) плавлением в защитном газе.
Тема урока: Характеристика меди и ее сплавов. Особенности технологии сварки (наплавки).
Сварочные
характеристики меди.
Для меди, характерны такие ее технические характеристики, как высокая
стойкость по отношению к воздействию различных химических веществ, сохранение
высоких механических свойств в условиях глубокого холода, высокие показатели
теплопроводности и электропроводности.
Необходимо учитывать следующие особенности меди и ее сплавов, влияющие на
технологию сварки.
1. В связи с высокой температурой и теплопроводностью, затрудняющими
локальный разогрев, требуются более концентрированные источники нагрева и
повышенные режимы сварки. Однако в связи со склонностью меди к росту зерна при
сварке многослойных швов металл каждого прохода для измельчения зерна
проковывают при температурах 550-800° С.
2. Легкая окисляемость меди при высоких температурах приводит к засорению
металла шва тугоплавкими окислами. Закись меди растворима в жидком металле и
ограниченно — в твердом. С медью закись образует легкоплавкую эвтектику Сu—Сu2О (температура плавления 1064° С), которая
сосредоточивается по границам зерен и снижает пластичность меди, что может
привести к образованию горячих трещин.
3. При сварке латуней возможно испарение цинка. Образующийся окисел цинка
ядовит, поэтому при сварке требуется хорошая вентиляция. Испарение цинка может
привести к пористости металла шва. Это осложнение удается преодолеть
предварительным подогревом металла до температуры 200-300° С и повышением
скорости сварки, уменьшающим растекание жидкого металла и испарение цинка.
4. Медь в расплавленном состоянии поглощает значительные количества
водорода. В околошовной зоне диффузионно-подвижный водород взаимодействует с Сu2О, располагающейся но границам зерен;
образующиеся пары воды, которые не растворяются в меди и не могут из нее выйти,
создают в металле значительные напряжения, приводящие к образованию большого
числа микротрещин. Это явление получило название водородной болезни меди.
5. Высокий коэффициент линейного расширения (в 1,5 раза больше, чем у
стали) может вызвать при сварке повышенные температурные и остаточные
сварочные напряжения и деформации. Для уменьшения деформации конструкции сварку
ведут в жестком закреплении, по прихваткам. При повышенной толщине металла
регулируют величину зазора.
6. Повышенная жидкотекучесть расплавленной меди и ее сплавов (особенно
бронзы) затрудняет сварку в вертикальном и потолочном положениях, поэтому чаще
всего сварку ведут в нижнем положении. Для формировании корня шва без дефектов
необходимы подкладки.
Для меди и сплавов на ее основе могут быть
использованы все основные способы сварки плавлением. Сварка в защитных
газах позволяет получать сварные соединения с наиболее высокими свойствами
(механическими, коррозионными и т. д.), так как металл шва содержит минимальное
количество примесей. Сварку выполняют неплавящимся (вольфрамовым) и плавящимся
электродами. Используют вольфрамовые лантанированные или иттрированные
электроды диаметром до 6 мм. В качестве присадочного металла при сварке
плавящимся электродом пригодна проволока из меди и ее сплавов, которые по
составу идентичны основному металлу, но содержат раскислители. При сварке
используют инертные по отношению к меди газы: аргон, гелий (чистотой 99,9%),
азот. При неплавящемся электроде сварку выполняют на переменном токе или на
постоянном токе прямой полярности. При сварке плавящимся электродом используют
постоянный ток обратной полярности.
Подготовка под сварку
металла и электродной проволоки
Проволоки, листы, плиты, трубы и другие полуфабрикаты
из меди должны иметь сертификаты, определяющие их марку и химический состав. На
заводе работники ОТК проверяют поступившие медь на соответствие свойств и
состава сертификатам, ГОСТам или техническим условиям.
Медные листы и плиты в процессе хранения укладывают в
горизонтальное положение без провисания с прокладкой между ними алюминия меди
или мягких пород дерева, исключающих образование на меди вмятин и других
повреждений.
В меди, предназначенной для изготовления ответственных
сварных конструкций перед запуском в производство необходимо проконтролировать
содержание кислорода, которое не должно превышать 0,01 %. Кроме того, требуется
определить содержание висмута и свинца с помощью химического анализа или
качественной пробы. Для этого испытывают стандартные образцы на разрыв при
температуре 550°С. Если относительное удлинение составляет более 5%, медь можно
применять для изготовления сварных конструкций ответственного назначения.
Режут металл на гильотинных ножницах или плазменной
дугой, а кромки под сварку разделывают механическим путем на строгальном или
фрезерном станке.
Перед сваркой поверхность меди тщательно очищают от
загрязнений металлической щеткой (до блеска) или промывают 10%-ным раствором
каустической соды. После чего выполняют обезжиривание бензином, уайт-спиритом
или другим растворителем.
Сварочную
проволоку перед
употреблением подвергают очистке травлением. Для этого применяют водный раствор
азотной кислоты (75 см3/л) или смесь серной и соляной кислоты в
соотношении 100:1 с последующей промывкой в воде, затем в щелочи, после чего
снова в чистой проточной воде. После промывки проволоку сушат горячим воздухом.
Медные электроды перед сваркой прокаливают, что снижает вероятность проявления
водородной болезни.
Сборка под
сварку. При
сборке под сварку тщательно подгоняют стык по всей длине в приспособлениях,
обеспечивающих надежное поджатие свариваемых кромок. Однако при этом должен
быть исключен натяг, вызывающий дополнительные напряжения в металле. Смещение
кромок и зазор между ними для большинства медных конструкций допускается не
более 10 % толщины свариваемого металла, но не более 2 мм.
В процессе сборки прихватки производят таким образом,
чтобы их высота не превышала 1/3 глубины разделки или катета шва. При сварке по
таким прихваткам образуется качественный сварной шов, не требующий подрубки
прихваток перед сваркой. Длина прихваток должна равняться толщине свариваемого
металла, а расстояние между ними не превышать L = (15...20)δ при толщине
свариваемого металла до 10 мм. При сварке меди большей толщины расстояние между
прихватками составляет L = (6...8)δ. Перед прихваткой свариваемый металл
предварительно подогревают. Зависимость температуры подогрева от толщины меди представлена
ниже.
|
6-10 |
10-20 |
20-40 |
40 и более |
Температура нагрева,- °С |
200-250 |
250-300 |
300-400 |
400-500 |
При охлаждении ниже 200°С и повторном предварительном
нагреве свариваемого изделия прихватки могут разрушиться, поэтому в перерывах
между технологическими операциями изделие не должно охлаждаться ниже
температуры 200-250°С.
Прихватки выполняют ручной дуговой сваркой покрытыми
электродами, ручной дуговой сваркой неплавящимся электродом в среде защитных
газов или полуавтоматической сваркой плавящимся электродом в среде защитных
газов. При ручной дуговой сварке прихватки выполняют на постоянном токе
обратной полярности.
Силу
сварочного тока выбирают по зависимости:
I=(60…70)dэ
где dэ – диаметр электрода, мм.
Для предупреждения проплавления металла, при
необходимости, с обратной стороны стыка устанавливают формирующие графитовые,
магнезитовые или медные водоохлаждаемые подкладки. В зависимости от
конструктивных особенностей свариваемых деталей можно применять остающиеся
подкладки в виде лент, полос или проволоки.
Механизированная сварка плавящимся
электродом (полуавтоматическая сварка) меди.
При сварке меди и ее сплавов основной трудностью
является получение сварных швов без пор, окисных включений и трещин.
Образование пор в металле шва может быть представлено зависимостью изменения
растворимости водорода в меди от содержания в ней кислорода. Согласно диаграмме
взаимной растворимости кислорода и водорода при снижении в металле кислорода
меньше определенного значения расплавленный металл склонен к активному
поглощению водорода. В этом случае в процессе сварки при высокой влажности
защитных газов и окружающего дугу воздуха, повышенном содержании водорода в
металле и электродной проволоке или их загрязнении .органическими веществами,
металл шва насыщается водородом.
Если содержание водорода в металле превышает его
растворимость, в процессе кристаллизации сварочной ванны образуется
перенасыщенный раствор водорода в меди, который приводит к образованию пор, а
при наплавке больших толщин металла и к трещинам. На поры и трещины такого
происхождения активные раскислители влияния не оказывают и не предотвращают их
образование. В целях борьбы с порами и трещинами такого происхождения в
активную зону дуги вводят небольшие доли кислорода.
Для получения металла шва высокого качества содержание
кислорода в смеси с инертными по отношению к меди газами должно быть
достаточным для полного связывания водорода в зоне дуги и предотвращения этим
попадания его в сварочную ванну, и недостаточным для образования в шве закиси
меди.
В случае если водорода в меди меньше критического
значения по диаграмме взаимной растворимости, медь может усваивать кислород в
значительных объемах. В этом случае водород, попадающий из зоны дуги в ванну,
восстанавливает закись меди. Образующиеся при этом в металле шва пары воды
способствуют образованию пор и трещин. В этом случае для борьбы с кислородом в
меди применяют активные раскислители: фосфор, марганец, кремний, титан,
цирконий и другие активные к кислороду элементы.
Для меди характерно отсутствие внутреннего окисления и
весьма интенсивное образование окислов на ее поверхности при высоких
температурах. Толщина образуемых окислов тем больше, чем выше температура
нагрева и больше при ней время выдержки. Поэтому нагрев меди в процессе сварки
и особенно предварительный ее подогрев приводят к окислению поверхности металла
с образованием закиси меди значительной толщины.
При нарушении технологии сварки расплавленный металл
затекает вперед движения дуги, заплавляя окислы меди на свариваемых кромках. В
этом случае окислы меди остаются в шве в виде неметаллических включений. В
зависимости от массы попавших в наплавленный металл окислов в швах образуются
несплавления или черноты, располагающиеся между швом и основным металлом или
между отдельными валиками или слоями.
Для предотвращения образования таких дефектов процесс
сварки в среде защитных газов выполняется таким образом, чтобы дуга частично
горела на расплавленном металле ванны, а часть дуги располагалась на окисленной
поверхности свариваемых кромок. Под воздействием температуры дуги окислы меди
на свариваемых кромках диссоциируют и в сварочную ванну не попадают.
Такая технология может быть выполнена только при
строгом соответствии требованиям силы тока, скорости подачи электродной
проволоки, ее диаметра, скорости сварки, напряжения на дуге, наклона электрода
и соблюдении других параметров режима и технологических приемов сварки.
В этом случае ручная дуговая сварка неплавящимся
электродом в среде защитных газов предпочтительна слева направо, а
полуавтоматическая сварка плавящимся электродом в газовой среде - справа
налево. При сварке неплавящимся электродом горелка должна располагаться для
сварки углом назад на 40-45° от металла, а присадочный металл подаваться с
хвостовой части ванны под углом 30-35° к свариваемому металлу. В процессе
полуавтоматической сварки угол наклона горелки от металла при расположении
углом вперед должен составлять 75-80°.
Так же располагается горелка или
электрод при автоматической сварке как в среде защитных газов, так и подслоем
флюса. Ввиду высокой тепло- и температуропроводности изделия из меди подвергают
предварительному подогреву и повышенной погонной энергии сварки. Температура
предварительного подогрева зависит от массы и химического состава свариваемого
изделия, условий сварки и ее погонной энергии, выдержки между наплавляемыми
валиками, применяемой защитной среды и других факторов. В процессе сварки
предварительно нагретое изделие остывает, а теплота, вводимая в процессе
сварки, способствует его восстановлению до заданной температуры. Такой
оптимальный вариант на практике встречается весьма редко.
При сварке изделий большой массы тепла дуги
недостаточно для поддержания заданной температуры нагрева. В этом случае
основной металл не смачивается наплавленным металлом и образуются несплавления
шва. Если температура нагрева изделия будет выше оптимальной, расплавленный
металл становится жидкотекучим и затекает вперед дуги. Это снижает глубину
проплавления и образует в шве наплывы и непровары. Для поддержания заданной
температуры в этом случае процесс сварки периодически прекращают, охлаждая
изделие до заданной температуры. Чтобы получить сварные швы высокого качества и
обеспечить необходимую производительность процесса, температура изделий при
сварке не должна отличаться более чем на ±50°С от оптимального значения. Такие
условия обеспечивают угол смачивания 70-90°, что позволяет получать высокое
качество сварных швов (см. рисунок 4).
Рисунок 4 - Влияние температуры предварительного подогрева на угол смачивания при сварке меди
В зависимости от конструктивных особенностей
свариваемого изделия из меди технология сварки должна обеспечивать выполнение
всех сварочных операций не более чем за три- четыре предварительных подогрева
свариваемого изделия.
Если изделие остыло ниже температуры 100-150°С,
очередной предварительный подогрев его считают следующим циклом нагрева. При
несоблюдении таких условий в зоне сплавления и в сварных швах возможно
появление трещин, заметно снижаются также механические свойства сварных
соединений.
Горелки подогрева должны быть направлены на 70-100 мм
по обе стороны стыка, а их пламя при перемещении горелок не должно попадать на
кромки.
Для металла толщиной более 20 мм сварку начинают и
заканчивают на технологических планках размером 100×100 мм с формой разделки и
толщиной металла, соответствующей спариваемому металлу. Если предусмотрен
припуск на механическую обработку в начале и конце шва, технологические планки
можно не применять. При отсутствии технологических планок кратер в конце шва
заваривают без перемещения горелки вперед. В случае вынужденных перерывов
сварки кратер ранее выполненного шва после предварительной вырубки и зачистки
перекрывают на 15-30 мм. Допускается выплавка кратера дугой с последующей
беспрерывной его заваркой. Автоматическую и полуавтоматическую сварку меди и ее
сплавов в среде защитных газов производят плавящимся электродом, а
автоматическую и ручную дуговую сварку - неплавящимся электродом.
Дуговая сварка неплавящимся электродом применяется для
сварки меди толщиной до 10 мм. Медь большей толщины сваривают плавящимся
электродом автоматической или полуавтоматической сваркой. При автоматической
сварке меди и ее сплавов плавящимся электродом для защиты дуги используют
аргон, гелий или азот. Полуавтоматическая сварка применяется для сварки мелких
узлов, прихватки изделий перед сваркой, приварки технологических планок и
ремонта дефектных участков сварных швов.
При
неизменном режиме сварки (Iсв = 400...450 А, Uд = 32...34 В, Vcв = 14...16 м/ч,
температура предварительного подогрева меди 400-450°С) примесь к аргону азота
увеличивает глубину провара и массу ванны от 4 г при сварке в аргоне до 9 г при
сварке в азоте. Такое изменение состава защитной среды уменьшает удельную
энтальпию металла сварочной ванны от 2156×10-3 Дж/кг при сварке
в аргоне до 1960х10-8 Дж/кг при сварке в азоте. Добавка к аргону гелия повышает
массу ванны до 6 г, а удельная энтальпия ее по сравнению с защитой дуги аргоном
уменьшается до 2055×10-3Дж/кг.
Таким образом, при неизменных параметрах режима
тепловложение в металл ванны составляет (Дж) в аргоне 3684,4, в гелии 5275,4 и
в азоте 7536,2. Приведенные данные показывают, что с энергетической стороны в
качестве защитной среды лучше применять азот, затем гелий и аргон. В результате
более высокого тепловложения в металл при сварке меди в среде азота
увеличивается глубина провара, что позволяет снизить температуру
предварительного подогрева свариваемых изделий и повысить эффективный КПД
процесса.
Для получения сварных швов без пор и других дефектов к
защитным газам добавляют небольшие доли кислорода. Кислород, поступающий в зону
дуги с защитным газом, расходуется на потери в окружающее пространство, на
взаимодействие с водородом диссоциации влаги защитного газа и окружающего
воздуха, на взаимодействие с водородом, поступающим в зону дуги с электродным и
свариваемым металлом, на окисление свариваемого металла и его легирующих
добавок, на образование озона и других химических соединений.
Водород, находящийся в атмосфере дуги, взаимодействует
с кислородом смеси в первую очередь, а оставшийся после этого кислород
затрачивается на окисление металла. Поэтому добавка кислорода, необходимая для
взаимодействия с водородом в зоне дуги и устранения этим причин образования пор
в металле шва, считается полезной и не должна превышать допустимых норм.
Смеси
защитных газов, удовлетворяющие таким требованиям:
Ar + до 2% O2;
N2 + до 4% O2;
He + до 2% O2;
25-35% He + до 4% O2 + Ar остальное;
25-35% N2 + до 4% O2 + Ar остальное.
Механизированная
сварка плавящимся электродом (полуавтоматическая сварка) выполняется на постоянном токе
обратной полярности. Режимы полуавтоматической сварки приведены в табл /p/pице
2.
Таблица 2 -
Режимы механизированной сварки плавящимся электродом (полуавтоматческой сварки)
меди
Диаметр сварочной проволоки, мм |
Сила сварочного тока, А |
Напряжение на дуге, В |
1,2 |
140-160 |
20-22 |
1,6 |
200-240 |
22-24 |
2,0 |
280-340 |
26-28 |
Изучить: 1. Сварочная характеристика меди.
2.Подготовка
материала к сварке.
3. Особенности сварки меди.
группа: 412
Предмет: Техника и технология частично механизированной сварки (наплавка) плавлением в защитном газе.
Тема урока: Характеристика среднелегированных и высоколегированных сталей. Особенности технологии сварки (наплавки).
Сварка
углеродистых сталей
Углеродистая сталь – сплав железа и углерода с
незначительным содержанием полезных примесей: кремний и марганец, вредных
примесей: фосфор и сера. Концентрация углерода в сталях данного типа составляет
0,1-2,07%. Углерод выступает в качестве основного легирующего элемента. Именно
он определяет сварочно-механические свойства этого класса сплавов.
В зависимости от величины содержания углерода
выделяют следующие группы углеродистых сталей:
менее 0,25% – низкоуглеродистые;
0,25-0,6 % – среднеуглеродистые;
0,6-2,07 % – высокоуглеродистые.
Потребность в высокоуглеродистых сталях возникает
при проведении ремонтных работ, при производстве пружин, режущих, бурильных,
деревообрабатывающих и других инструментов, высокопрочной проволоки, а также в
тех изделиях, которые должны обладать высокой износостойкостью и прочностью.
Технология
сварки высокоуглеродистых сталей
Сваривание возможно, как правило, с предварительным
и сопутствующим подогревом до 150-400°С, а также последующей термообработкой.
Обусловлено это склонностью данного типа сплавов к хрупкости, чувствительностью
к горячим и холодным трещинам, химической неоднородностью шва.
К
сведению! Исключения возможны, если использовать специализированные электроды
для разнородных сталей.
После подогрева необходимо произвести отжиг, который
нужно проводить до тех пор, пока изделие не остынет до температуры 20°С.
Важным условием является недопустимость
осуществления сварки на сквозняках и при температуре окружающей среды ниже 5°С.
Для повышения прочности соединения необходимо
создавать плавные переходы от одного до другого свариваемого металла.
Хорошие результаты достигаются при сваривании узкими
валиками, с охлаждением каждого наплавленного слоя.
Исполнителю следует также соблюдать правила,
предусмотренные для соединения среднеуглеродистых сплавов.
Особенности
сварки высокоуглеродистых сталей
Рабочую поверхность необходимо очистить от
загрязнений различного рода: ржавчина, окалина, механические неровности и
грязь. Присутствие загрязнений может привести к образованию пор.
Охлаждать конструкции из высокоуглеродистых сталей
нужно медленно, на воздухе, для нормализации структуры.
Предварительный подогрев ответственных изделий до
400°С позволяет достичь необходимого показателя прочности.
Виды
сварки высокоуглеродистых сталей
1. Оптимальным вариантом проведения сварочного
процесса является ручная дуговая сварка с помощью покрытых электродов. Работа с
высокоуглеродистыми сталями обладает большим количеством специфических
характеристик. Поэтому сварка высокоуглеродистой стали проводится специально
разработанными электродами, например, НР-70. Сваривание осуществляется
постоянным током обратной полярности.
2. Сварка под флюсом также используется для
соединения сплавов данного типа. Равномерно покрыть флюсом рабочую зону в
ручном режиме довольно сложно. Поэтому, в большинстве случаев, используется
автоматическая технология. Расплавленный флюс образует плотную оболочку и
предотвращает воздействие вредных атмосферных факторов на сварочную ванну. Для
сваривания под флюсом используются трансформаторы, выдающие переменный ток.
Данные аппараты позволяют создавать устойчивую дугу. Главное достоинство
данного метода – небольшие потери металла вследствие малого разбрызгивания.
Важно отметить, что не рекомендуется применять метод
газовой сварки. Процесс характеризуется выгоранием большого количества
углерода, в результате чего образуются закалочные структуры, которые
отрицательно сказываются на качестве шва.
Однако, если свариванию подвергаются рядовые конструкции,
то применение данного способа возможно. Соединение производится на нормальном
или незначительном пламени, мощность которого не превышает 90 м3 ацетилена в
час. Изделие нужно подогреть до 300°С. Сварка осуществляется левым способом,
что дает возможность уменьшить время нахождения металла в расплавленном
состоянии и продолжительность его перегрева.
Сварка
углеродистой стали
Сварка коррозионностойких и углеродистых сталей
является ярким примером соединения разнородных материалов.
Предварительный и сопутствующий нагревы изделий до
температуры примерно в 600°С позволят получить шов с более однородной
структурой. После работ нужно произвести термическую обработку, это поможет
избежать образование трещин.
Для сваривания нержавейки и низкоуглеродистых сталей
на практике применяются два метода, которые подразумевают использование
сварочных стержней:
электроды из высоколегированной стали или электроды
на никелевой основе заполняют сварочный шов;
кромки изделия из низкоулегродистой стали наплавляется
легированными электродами, затем плакированный слой, кромки из нержавейки
свариваются специальными электродами для нержавейки.
Сварку нержавеющих и углеродистых сталей также можно
проводить аргонодуговым методом. Однако, такая технология используется крайне
редко и только для работы с особо ответственными конструкциями.
Также исполнитель может произвести соединение
методом полуавтоматической сварки с помощью металлического электрода в защитной
среде инертных газов.
Изучить: 1. Технология сварки
высокоуглеродистых сталей.
2. Особенности сварки высокоуглеродистых сталей.
3. Сварка углеродистой стали.
группа: 412
Предмет: Техника и технология ручной дуговой сварки (наплавка, резка) неплавящимися электродами в защитном газе.
Тема урока: Подготовка к сварке. Выбор режимов сварки деталей из алюминиевых сплавов.
Подготовка к сварке
Резку и подготовку кромок деталей из алюминия и его
сплавов следует вести механическими способами
Стыковое соединение металла разной толщины
Конструктивные элементы подготовки кромок (размеры
приведены в мм)
Конструктивные элементы подготовки кромок при сварке
со сквозным проплавленнем н формированием шва на весу
При сварке за один проход может возникнуть надрез
корня шва
При снятии фаски с обратной стороны стыкуемых кромок
надрез не возникает. Для снятия фасок можно использовать напильник
Свариваемые поверхности тщательно очищают от смазки,
на ширине 100-150 мм от кромок обезжиривают ацетоном, уайт-спиритом или другим
растворителем.
Пленку окиси алюминия удаляют механически или
химическим травлением.
При механической обработке (непосредственно перед
сваркой) кромки зачищают на ширину 25-30 мм абразивной бумагой, шабером или
щеткой из нержавеющей проволоки диаметром не более 0,15 мм.
Химическое травление проводят в течение 0,5-1 мин в
растворе, состоящем из 50г едкого натра и 45г фтористого натрия на 1 л воды.
После травления поверхность промывают проточной водой, а затем осветляют в
30-35%-ном растворе азотной кислоты (для алюминия и сплавов типа АМц) или в
25%-ном растворе ортофосфорной кислоты (для сплавов типа АМг и В95). После
повторной промывки поверхность сушат до полного испарения влаги.
Алюминиевую сварочную проволоку перед сваркой тоже
обрабатывают. Сначала ее обезжиривают, а затем подвергают травлению в 15%-ном растворе
едкого натра в течение 5-10 мин при 60-70°С. после чего следует промывка в
холодной воде и сушка при температуре 300°С в течение 10-30 мин.
Подготовленные к сварке материалы сохраняют свои
свойства 3-4 дня. Позже на поверхности вновь образуется окисная пленка.
Детали из алюминия и его сплавов собирают в
приспособлениях или на прихватках, выполняемых аргонодуговой сваркой
W-электродом. Расстояние между прихватками должно быть не более 150-180 мм.
Поверхности прихваток непосредственно перед сваркой зачищают
металлическими щетками. Обнаруженные дефектные прихватки удаляют, и стыки
прихватывают повторно. При сварке прихватки полностью переплавляют.
Выбор параметров режима
Сварку ведут на постоянном токе обрат ной полярности.
Защитным газом служит apгон или гелий и их смеси. Непосредственно перед сваркой
кромки обезжиривают .
Диаметр сопел горелок выбирают равным не менее 18-22
мм.
Длина дуги должна составлять 2-6 мм, а сварочный ток -
быть больше, чем при ручной аргонодуговой сварке W-электродом. Сварку выполняют
за один проходили двусторонними швами.
Процесс
сварки может быть: импульсно-дуговым (ИДС), струйным (СТР) или с короткими
замыканиями дуги (КЗ).
Ориентировочные режимы
Вид соединения |
Размеры, мм |
Процесс сварки |
Газ |
Сварочный ток, А |
Напряжение на дуге, В |
Скорость сварки, м/ч |
Диаметр электрода , мм |
Вылет электрода, мм |
Расход газа, л/мин |
|
S |
b |
|||||||||
|
2,5-3 |
0+0,5 |
ИДС |
Ar |
40-80 |
15-18 |
35-45 |
1,2 |
10-13 |
7-9 |
|
4 |
0+0,5 |
ИДС ИДС СТР |
Ar |
80-130 |
18-20 |
30-40 |
1,4-1,6 |
13-18 |
8-10 |
|
6 |
0+1 |
ИДС ИДС СТР |
Ar |
180-250 |
23-26 |
20-35 |
1,6-3 |
15-30 |
12-14 |
|
8-10 |
0+1 |
ИДС СТР СТР |
Ar |
250-320 |
25-30 |
20-35 |
1,6-3 |
15-40 |
12-20 |
|
12-16 |
0+4 |
СТР |
Ar |
320-420 |
26-28 |
20-30 |
2 |
18-25 |
20-25 |
|
20-30 |
0+1,5 |
СТР |
Ar |
310-550 |
26-35 |
18-20 |
2-4 |
20-40 |
18-25 |
|
2,5-3 |
0+0,5 |
ИДС |
Ar |
60-100 |
16-18 |
35-40 |
1-1,4 |
10-15 |
6-8 |
4-5 |
0+0,5 |
ИДС |
Аг |
120-220 |
18-22 |
25-35 |
1,2-1,6 |
12-18 |
10-12 |
|
8 и более |
0+1 |
СТР |
Аг |
280-330 |
27-29 |
20-25 |
1,6 |
18-30 |
20-25 |
Техника сварки
При сварке алюминия и его сплавов необходимо
использовать чистые и сухие перчатки из спилка или из другого подобного
материала
Механизированную сварку стыковых соединений без
разделки кромок в нижнем и вертикальном положениях выполняют обычно без
поперечных колебаний электрода
При наличии разделки кромок первый шов выполняют также
без поперечных колебаний, а последующие - с небольшими (до 5 мм) перемещениями
электрода
При сварке угловых швов в нижнем положении угол наклона горелки относительно вертикальной стенки - 30-
45°. Угловой шов на вертикальной плоскости ведут снизу-вверх "углом вперед". Однопроходную сварку
выполняют с перемещениями конца электрода. Угловые швы больших сечений на вертикальной плоскости
делают многопроходными путем выполнения узких швов. Так же
сваривают и стыковые горизонтальные швы
Изучить: 1. Подготовка металла к сварке.
2. Выборы
параметров сварки.
3. Техника
сварки.
группа: 412
Предмет: Техника и технология ручной дуговой сварки (наплавка, резка) неплавящимися электродами в защитном газе.
Тема урока: Сварочные материалы для ручной дуговой сварки (наплавка, резка) неплавящимися электродами в защитном газе деталей из алюминия. Расход сварочных материалов.
Особенности дуговой сварки в защитных газах следующие: высокая концентрация
энергии дуги, обеспечивающая минимальную зону термического влияния и небольшие
деформации изделия; высокая производительность; эффективная защита
расплавленного металла, особенно при использовании в качестве защитной среды
инертных газов; отсутствие необходимости применения флюсов или обмазок;
возможность сварки в различных пространственных положениях.
При сварке в защитных газах в качестве источника энергии,
обеспечивающего плавление присадочного и основного металлов, используется
электрическая дуга. Дуга отличается от других видов разрядов в газах низким
катодным падением потенциала, а следовательно, - низким общим напряжением дуги
и высокой плотностью тока. Электрическая дуга по длине имеет три области,
различающиеся физическими явлениями, протекающими в них.
Участки, непосредственно примыкающие к электродам, называют
катодной (у отрицательного электрода) и анодной (у положительного электрода)
областями, а участок между ними - столбом дуги. Те части электродов, на которые
<<опирается>>дуга и через которые проходит основной ток дуги,
называют активными пятнами, причем на положительном электроде - анодное пятно,
а на отрицательном - катодное. Температура дуги при сварке плавящимся
электродом сравнительно невелика: 5000…6500 гр.ц. В дугах с неплавящимся
электродами температура значительно выше.
С увеличением давления повышается напряженность поля в столбе, а размеры дуги
уменьшаются. Таким образом, изменяя давление, при котором горит дуга, можно
значительно изменять электрические и энергетические характеристики дуги.
Сварочная дуга в защитных газах характеризуется сильным излучением.
Процессы, протекающие в катодной области, играют основную
роль в поддержании дугового разряда и получении стабильной дуги. В анодной
области ток переносится отрицательно заряженными частицами - электронами, а при
наличии в дуговом промежутке газов, обладающих электроотрицательным
потенциалом, - также и отрицательными ионами.
Аргон - бесцветный, неядовитый газ, почти в 1,5 раза тяжелее
воздуха. С большинством элементов аргон не образует химических соединений. В
металлах аргон нерастворим в жидкостях, так и в твердом состоянии.Промышленный
аргон получают из воздуха в разделительных колонках путем избирательного
испарения с последующим глубоким охлаждением фракционной перегонкой. Полученный
таким образом аргон содержит некоторое количество кислорода. Дальнейшая очистка
от кислорода производится беспламенным сжиганием водорода в аргоне или другим
способом. В чистом аргоне все же остается небольшое количество кислорода, азота
и влаги. Аргон марки А рекомендуют использовать при сварке активных и едких
металлов и их сплавов (Ti, Zr, Nb); марки Б - для сварки сплавов на основе
магния, алюминия; марки В - для сварки коррозионно-стойких, жаропрочных и
окалиностойких сталей.
При сварке плавлением алюминия и его
сплавов в основном используют тянутую и прессованную сварочную проволоку из
алюминия и алюминиевых сплавов по ГОСТ 7871-75, который предусматривает
изготовление проволоки четырнадцати марок. Овальность проволоки не должна
превышать допустимых отклонений диаметра. Поверхность проволоки диаметром 4мм и
менее подвергают химической обработке. После обработки проволока должна иметь
блестящую поверхность с параметром шероховатости Ra менее 2,5 мкм по ГОСТ
2789-73.
Полуфабрикаты из алюминиевых сплавов (листы, профили, трубы)
характеризуются малой плотностью, сравнительно высокой прочностью, хорошей
обрабатываемостью и способностью легко деформироваться. Поэтому они нашли
широкое применение в таких отраслях машиностроения, как авиастроение,
судостроение, производство химической аппаратуры, строительство, транспортное
машиностроение др. Благодаря высокой коррозионной стойкости, а также хорошей
тепло- и электропроводимости большинство алюминиевых сплавов во многих случаях
являются трудно заменимыми конструкционными материалами.
В сварных конструкциях получили распространение деформируемые
алюминий (АД, АД1 и др.) и алюминиевые сплавы, не упрочняемые термообработкой
(АМц, АМг, АМг3, АМг63, АМг6 и др.), а также упрочняемые термообработкой (Д20,
М40, Д20, ВАД23, В92А,1201,1420 и др.). Литейные сплавы применяются в сварных
конструкциях редко. С помощью сварки плавлением изделий из алюминиевых сплавов
получаются различные виды сварных соединений - стыковые, нахлесточные, тавровые
и угловые. Наибольшее распространение получили стыковые соединения.
Нахлесточные, тавровые и угловые соединения желательно выполнять аргонодуговой
сваркой.
Для сварки алюминиевых сплавов в защитных газах применяют
аргон первого сорта или смеси аргона с гелием. При этом разрушение оксидной
пленки происходит в результате катодного распыления, в связи с чем, сварку
алюминиевых сплавов в аргоне желательно выполнять на постоянном токе обратной
полярности. Это возможно при автоматической и полуавтоматической сварке
плавящимся вольфрамовым электродом.
Изучить: 1. Основы сварки деталей из алюминия.
2. Сварочные
материалы применяемые при сварке деталей из алюминия.
3. Защитные газы применяемые при сварке алюминия.
группа: 412
Предмет: Техника и технология ручной дуговой сварки (наплавка, резка) неплавящимися электродами в защитном газе.
Тема урока: Технология сварки алюминия и его сплавов.
Сварка
алюминия и его сплавов.
Для алюминия и его сплавов возможно
применение почти всех промышленных способов сварки плавлением и давлением.
Ручную дуговую сварку покрытыми электродами в настоящее время используют редко,
хотя она в принципе возможна. Наибольшее распространение для изготовления
сварных конструкций приобрела дуговая сварка в инертных газах. Автоматическую
дуговую сварку с использованием флюсов применяют для крупногабаритных
конструкций, электрошлаковую - для металла больших толщин. Для получения
сварных швов с высокими механическими характеристиками используют также
электроннолучевую и лазерную сварку.
Дуговая сварка в среде
инертных газов наиболее
распространена при изготовлении конструкций из алюминиевых сплавов
ответственного назначения. Осуществляется как неплавящимся вольфрамовым
электродом, так и плавящимся. Используемые инертные газы: аргон высшего и
первого сорта по ГОСТ 10157-79, гелий высокой чистоты и смесь аргона с гелием.
Выбор конкретного способа сварки определяется толщиной металла, конструкцией
изделия и масштабом производства.
Дуговая сварка неплавящимся вольфрамовым электродом. В качестве неплавящегося электрода применяют
вольфрам с добавками лантана, иттрия и других элементов. Использование чистого
вольфрама не рекомендуется. Отмеченные примеси придают электроду повышенную
стойкость, обеспечивают большую плотность тока и другие преимущества.
Питание дуги осуществляется от
источника переменного тока, что обеспечивает разрушение оксидной пленки за счет
эффекта катодного распыления. Использование дуги переменного тока связано с
тем, что при сварке постоянным током обратной полярности из-за возможного
расплавления вольфрамового электрода допустим сварочный ток небольшой величины,
а при сварке постоянным током прямой полярности затруднено удаление оксидной
пленки.
Сварку вольфрамовым электродом
выполняют вручную, механизировано или автоматически. При сварке в среде гелия
напряжение повышается на 7... 10 В, при этом дуга укорачивается, а сила тока
снижается на 10... 15 %. Расход газа при использовании гелия увеличивается в 1,8...2,2
раза. Ручная сварка ведется на меньших значениях тока в один или несколько
проходов в зависимости от толщины.
Дуговая сварка вольфрамовым
электродом в среде инертных газов является наиболее универсальным способом
сварки, который позволяет выполнять сварку в различных пространственных
положениях и труднодоступных местах. При этом достигается высокая прочность и
пластичность сварных соединений, близкие к прочности и пластичности основного
металла.
Сварка вольфрамовым электродом
диаметром 2...6 мм целесообразна для узлов алюминия и его сплавов толщиной до
12 мм. Металл толщиной до 3 мм сваривают за один проход на стальной подкладке;
при толщине металла 4...6 мм сварку выполняют с двух сторон, а начиная с
толщины 6...7 мм применяют разделку кромок (V- или Х-образную). Соединение с
отбортовкой кромок целесообразно для металла толщиной 0,8...2 мм. Присадочный
металл выбирают в зависимости от марки сплава: для технического алюминия -
проволоку марок АО, АД или АК, для сплавов типа АМг - проволоку той же марки,
но с увеличенным (на 1___1,5 %) содержанием магния для компенсации его
угара.
Диаметр проволоки составляет 2...5 мм. Рекомендуемые режимы ручной сварки
приведены в табл. 14.
Рекомендуемые
режимы ручной дуговой сварки вольфрамовым электродом
Таблица 14
Толщина
металла, мм |
Диаметр,
мм |
Сила тока,
А |
||
вольфрамового электрода |
присадочной проволоки |
в аргоне |
в гелии |
|
1...2 |
2 |
1...2 |
50...70 |
30...40 |
3...4 |
3 |
2...3 |
100...130 |
60...90 |
4...6 |
4 |
3 |
160... 180 |
ПО...130 |
6...10 |
5 |
3...4 |
220...300 |
160...240 |
11...15 |
6 |
4 |
280...360 |
220...300 |
Для
обеспечения надежной газовой защиты в зависимости от режима сварки
устанавливают оптимальный расход газа (от 4 до 12 л/мин при ручной сварке и до
30 л/мин при автоматической). Чрезмерный расход газа приводит к его
турбулентному истечению и засасыванию воздуха в зону дуги, т. е. к нарушению
газовой защиты, а при малом истечении газа (или чрезмерно большой скорости
сварки) защита зоны сварки будет недостаточной. Подачу защитного газа включают
с помощью аппаратуры управления за 3...5 с до возбуждения дуги, а выключение
подачи - через 5...7 с после обрыва дуги.
При
выполнении сварки алюминия и его сплавов вручную особое внимание уделяется
технике сварки. Угол между присадочной проволокой и электродом должен быть
примерно 90°. Присадка подастся короткими возвратно-поступательными движениями.
Недопустимы поперечные колебания вольфрамового электрода. Длина дуги -
1,5...2,5 мм. Вылет электрода от торца наконечника горелки - 1___1,5 мм. Сварку
обычно ведут справа налево («левый» способ), чтобы снизить перегрев свариваемого
металла.
Для сварки
алюминия и его сплавов малых толщин целесообразно применять импульсную дугу
переменного тока. При ее использовании удается сваривать алюминиевые сплавы
толщиной от 0,2 мм. Стыковые соединения металла толщиной 0,2... 1 мм сваривают
на стальных подкладках с формирующей канавкой, используя присадочную проволоку
диаметром 0,6...0,8 мм. При этом коробление изделия снижается на
40.. . 60%.
Сварка
плавящимся электродом. Плавящийся электрод применяют при дуговой сварке алюминиевых сплавов
толщиной более 4 мм. Сварку выполняют на постоянном токе обратной полярности
при силе тока, обеспечивающей струйный перенос электродного металла, проволокой
1.5.. .2.5
мм. В связи с недостаточно высокой жесткостью алюминиевой проволоки сварка
проволокой диаметром менее 1,2... 1,5 мм затруднительна. Сварку ведут в чистом
аргоне либо в смеси аргона и гелия (до 70 % Не). При этом газовую смесь
предпочитают при сварке металла больших толщин. Ориентировочные параметры
режимов сварки плавящимся электродом сплавов типа АМг приведены в габл. 15.
Рекомендуемые
режимы сварки плавящимся электродом в защитных газах алюминиевых ставов типа
АМг
Таблица 15
Тип
соединения |
6, мм |
d„ мм |
Дв5 А |
t/д, В |
К», м/ч |
Расход Аг, л/мин |
Число проходов |
Встык, без
разделки кромок |
4...6 |
1,5...2,0 |
140...220 |
19...22 |
25...30 |
6...10 |
2 |
8...10 |
1,5...2 |
220...300 |
20...25 |
20...25 |
8...10 |
2 |
|
12 |
2 |
280...300 |
20...25 |
15...20 |
8...10 |
2 |
|
Встык V-образной |
15 |
2 |
250...390 |
24...30 |
20...25 |
12..18 |
4 |
25 |
2,5 |
400...440 |
26...29 |
15...40 |
15...20 |
8 |
При сварке
на постоянном токе обратной полярности обеспечивается надежное разрушение
оксидных пленок за счет катодного распыления и хорошее формирование швов.
Преимуществами процесса сварки плавящимся электродом являются: хорошее
перемешивание металла сварочной ванны, что снижает вероятность образования
крупных оксидных включений в металле швов; высокая производительность, особенно
при сварке металла большой толщины. Однако при этом способе сварки показатели
механических свойств несколько ниже, чем при сварке неплавящимся электродом.
При
необходимости вести сварку в различных пространственных положениях используют
импульсно-дуговой процесс. Импульсное изменение сварочного тока позволяет
обеспечить направленный перенос электродного металла в сварочную ванну и
удержание металла сварочной ванны независимо от пространственного положения
сварки. Кроме того, пульсация мощности дуги способствует получению более
мелкозернистой структуры металла шва, плавных очертаний швов с мелкочешуйчатым
строением.
Изучить: 1. Сварка
алюминия в среде защитных газов.
2. Требования при выполнении сварочных работ.
3. Техника сварки алюминия.
группа: 412
Предмет: Техника и технология ручной дуговой сварки (наплавка, резка) неплавящимися электродами в защитном газе.
Тема урока: Конструктивные размеры стыковых соединений при сварке высоколегированных сталей. Выбор режимов сварки.
Сварка высоколегированных сталей и сплавов
Высоколегированными
называют стали, содержащие один или несколько легирующих элементов в количестве
10 - 55%.
Высоколегированными
называют сплавы на железоникелевой основе (железа и никеля содержится более
65%) и на никелевой основе (никеля содержится более 55%).
По ГОСТ 5632
- 72 насчитывается 94 марки высоколегированных стилей и 22 марки
высоколегированных сплавов. Несколько марок сталей и сплавов выпускается по
различным техническим условиям.
Высоколегированные
стали и сплавы классифицируют по различным признакам, главным образом, по
системе легирования, структуре и свойствам. По системе легирования высоколегированные
стали делят, например, на хромистые, хромоникелевые, хромомарганцевые,
хромоникелемарганцевые, хромомарганцеазотистые. Самые распространенные
высоколегированные сплавы - никелевые, никелехромистые, никелехромовольфрамовые
и никелехромокобальтовые.
По структуре
высоколегированные стали подразделяют на стали мартенситного класса (например,
15X5, 15Х5М, 15Х5ВФ, 09Х16Н4Б, 11Х11Н2В2МФ - всего по стандарту 20 марок),
мартенситно-ферритного класса (15Х6СЮ, 15Х12ВНМФ, 12X13 и др.), ферритного
класса (08X13, 10Х13СЮ, 12X17, 15Х25Т), аустенитно-мартенситного класса (такие,
как 07Х16Н6, 08Х17Н5МЗ), аустенитно-ферритного класса (например, 08Х20Н14С2,
08Х18Г8Н2Т) и аустенитного класса (03Х17Н14М2, 03Х16Н15МЗБ, 08Х10Н20Т2,
08Х16Н13М2Б, 09Н16Х14Б, 09Н19Х14В2БР, 12Х18Н9, 12Х18Н9Т, 45Х14Н14В2М). В
некоторых аустенитных сталях никель, как дефицитный материал, частично или
полностью заменяют марганцем и азотом: 10Х14Г14НЗ, 10Х14Г14Н4Т, 12Х17Г9Н4А,
10Х14Г15А, 15Х17Г14А; всего по ГОСТ 5632-72 выпускается 27 марок аустенитных
сталей.
По системе
упрочнения высоколегированные стали и сплавы делят на карбидные, содержание
углерода 0,2 - 1,0%, боридные (образуются бориды железа, хрома, ниобия,
углерода, молибдена и вольфрама), с интерметаллидным упрочнением (упрочнение
мелкодисперсными частицами).
По свойствам
высоколегированные стали и сплавы подразделяют на коррозионностойкие
(нержавеющие), обладающие стойкостью против любой коррозии - атмосферной,
почвенной, щелочной, кислотной, солевой, межкристаллитной; жаростойкие
(окалиностойкие), не окисляющиеся при высоких температурах нагрева (до 1300°С);
жаропрочные, способные работать при температурах свыше 1000°C в течение
нормированного времени без снижения прочности.
Особенности
сварки высоколегированных сталей и сплавов. По сравнению с низкоуглеродистыми сталями
большинство высоколегированных сталей и сплавов обладают пониженным
коэффициентом теплопроводности (до 2 раз при повышенных температурах) и
увеличенным коэффициентом линейного расширения (до 1,5 раза).
Низкий
коэффициент теплопроводности приводит при сварке к концентрации тепла и
вследствие этого к увеличению проплавления металла изделия. Поэтому для
получения заданной глубины проплавления следует снижать величину сварочного
тока на 10 - 20%.
Увеличенный
коэффициент линейного расширения приводит при сварке к большим деформациям
сварных изделий, а в случае значительной жесткости - относительно крупные
изделия, повышенная толщина металла, отсутствие зазора между свариваемыми
деталями, жесткое закрепление изделия - к образованию трещин в сварочном
изделии.
Высоколегированные
стали и сплавы более склонны к образованию трещин, чем низкоуглеродистые.
Горячие трещины появляются большей частью в аустенитных сталях, холодные - в
закаливающихся сталях мартенситного и мартенситно-ферритного классов. Кроме
этого, коррозионностойкие стали, не содержащие титана или ниобия или
легированные ванадием, при нагревании выше 500°С теряют антикоррозионные
свойства по причине выпадения из твердого раствора карбидов хрома и железа,
которые становятся центрами коррозии и коррозионного растрескивания.
Термической обработкой (чаще всего закалкой) можно восстановить
антикоррозионные свойства сварных изделий. Нагревом до 850°С ранее выпавшие из
раствора карбиды хрома вновь растворяются в аустените, а при быстром охлаждении
они не выделяются в отдельную фазу. Такой вид термообработки называют
стабилизацией. Однако стабилизация приводит к снижению пластичности и вязкости
стали. Получение высокой пластичности, вязкости и одновременно
анти-коррозийности сварных соединений возможно нагревом металла до температуры
1000 - 1150°С и быстрым охлаждением в воде (закалка).
Содержание
углерода в основном металле и металле шва до 0,02 - 0,03% полностью исключает
выпадение карбидов хрома, а следовательно, межкристаллитную коррозию.
На практике
нашли применение следующие пути предотвращения трещин при сварке
высоколегированных сталей: создание в металле шва двухфазной структуры
(аустенит и феррит); ограничение в шве содержания вредных примесей (серы,
фосфора, свинца, сурьмы, олова, висмута) и введение таких элементов, как
молибден, марганец, вольфрам; применение электродных покрытий основного и
смешанного видов; создание при сварке менее жесткого состояния изделия.
Практикой
сварки аустенитной стали установлено, что с увеличением жесткости при
выполнении шва необходимо к аустениту прибавлять феррита в количестве от 2 до
10%. В этом случае пластичность металла шва по сравнению с аустенитным швом
повышается и усадка даже при жестком состоянии сварного изделия происходит за
счет повышенной пластической деформации металла шва без образования трещин.
Применение
электродов с основным или смешанным покрытием с легированием металла шва
молибденом, марганцем, вольфрамом придает металлу шва мелкозернистое строение.
В этом случае пластические свойства металла возрастают и при усадке горячие
трещины в нем не возникают.
Для
получения сварных соединении без трещины в процессе сварки рекомендуется
свариваемые детали собирать с зазором (рис. 102) и по возможности применять швы
с низким проваром (коэффициент формы провара должен быть менее 2). Швы лучше
выполнять тонкими электродами диаметром 1,6 - 2,0 мм при минимальной погонной
тепловой энергии.
Рис. 102. Влияние коэффициента формы провара (а, б) и зазора в корне шва (в, г)
на стойкость аустенитного углового шва против образования кристаллизационных
трещин марок высоколегированных сталей и сплавов должен быть строго обоснован
Сварные
соединения с неоднородным швом как после сварки, так и после термической
обработки обладают меньшей прочностью по сравнению с основным металлом. Кроме
того, в так их неоднородных сварных соединениях при эксплуатации с высоким
нагревом наблюдаются диффузионные явления между металлом шва и околошовным
металлом для выравнивания химического состава, что приводит к появлению
холодных трещин в околошовном металле, в зоне металлической связи. Поэтому
выбор типа электрода при дуговой сварке различных
Подогрев
(общий или местный) до температуры 100 - 300°С рекомендуется при сварке всех
высоколегированных сталей и сплавов в зависимости от характера микроструктуры
основного металла, содержания углерода, толщины и жесткости изделия. Для
мартенситных сталей и сплавов подогрев изделия обязателен; для аустенитных
сталей он применяется редко. Подогрев способствует более равномерному
распределению температур по изделию в процессе сварки и охлаждению с меньшими
скоростями, в результате чего не образуются концентрированные усадочные деформации
по сечению сварного соединения и трещины не возникают.
Перегрев
(укрупнение зерен) металла шва и околошовного металла при сварке
высоколегированных сталей и сплавов зависит от химического состава и
микроструктуры, температуры нагрева и длительности пребывания металла при
высокой температуре. Обычно при сварке больше перегреваются однофазные
ферритные стали.
Высоколегированные
стали, содержащие углерода более 0,12% (31Х19Н9МВБТ, 36Х18Н25С2, 55Х20Г9АН4,
17Х18Н9 и др.) свариваются с предварительным подогревом до 300°С и выше с
последующей термической обработкой сварных изделий.
Сварочная
проволока, виды электродных покрытии и типы покрытых электродов для сварки. Для сварки высоколегированных
сталей с особыми свойствами применяют сварочную проволоку, например Св-04Х19Н9,
Св-05Х19Н9Ф3С2, Св-06Х19Н9Т, Св-07Х19Н10Б, Св,08Х20Н9С2БТЮ, Св-10Х16Н25М6А -
всего 41 марка по ГОСТ 2246 - 70.
Электроды
берут с основными, рутилоосновными и рутилофлюоритноосновными покрытиями.
Дуговая сварка аустенитных сталей электродами с основным покрытием приводит к
науглероживанию металла шва, что вызывает снижение стойкости его против
межкристаллитной коррозии. Науглероживание происходит за счет разложения
мрамора, который содержится в большом количестве в этом покрытии. Науглероживание
металла шва исключается при сварке аустенитной стали электродами с
рутилоосновным покрытием (например, ОЗЛ-14), содержащего мрамора только 10%
вместо 35 - 45% в электродах с основным покрытием (например, УОНИИ-13/НЖ).
Ориентировочный
выбор марки сварочной проволоки, вида покрытия и типа электрода при дуговой
сварке высоколегированных сталей и сплавов в зависимости от назначения сварного
изделия приведен в табл. 38.
38. Примерный выбор покрытых электродов для сварки высоколегированных сталей с
особыми свойствами
ГОСТ 10052 -
75 предусматривает 49 типов покрытых электродов для ручной дуговой сварки
высоколегированных сталей с особыми свойствами, например, Э-02Х19Н9Б,
Э-04Х20Н9, Э-07Х20Н9, Э-06Х22Н9, Э-06Х13Н, Э-08Х20Н9Г2Б, Э-08Х14Н65М15В4Г2,
Э-10Х20Н70Г2М2В.
Каждый тип
электрода включает одну или несколько марок покрытых электродов.
Условное
обозначение электродов для дуговой сварки выполняется по ГОСТ 9466 - 75 (см.
гл. V). При этом во второй строке условного обозначения электродов группа
индексов, указывающих характеристики наплавленного металла и металла шва,
состоит из четырех цифровых индексов для электродов, обеспечивающих
аустенитно-ферритную структуру наплавленного металла, и из трех цифровых
индексов - для остальных электродов.
Первый
индекс показывает стойкость наплавленного металла и металла шва против
межкристаллитной коррозии (в зависимости от метода испытания в табл. 3
стандарта приняты индексы от 0 до 5). Второй индекс указывает максимальную
рабочую температуру, при которой обеспечивается относительно длительная
прочность наплавленного металла и металла шва (по табл. 4 в стандарте введены
цифровые индексы от 0 до 9). Третий индекс показывает допускаемую рабочую
температуру сварных соединений, выполненных данными электродами при сварке
жаростойких сталей (см. табл. 5). Четвертый индекс указывает содержание
ферритной фазы в наплавленном металле для электродов, обеспечивающих
аустенитно-ферритную структуру наплавленного металла (см. табл. 6).
Все данные,
необходимые для составления группы индексов, берутся из паспортов на электроды
конкретных марок.
Газовая
сварка аустенитных сталей производится пламенем мощностью 70 - 75 дм3 ацетилена/ч
на 1 мм толщины металла. Окислительное пламя не допускается, так как оно влечет
выгорание хрома. Для присадки применяют сварочную проволоку марок Свт02Х19Н9Т,
Св-08Х19Н10Б и других с минимальным содержанием углерода, легированную ниобием
или титаном. Тем не менее, при газовой сварке титан почти полностью выгорает и
не может обеспечить стойкость металла шва против межкристаллитной коррозии.
Кроме этого, нержавеющие стали при температурах нагрева 500 - 850°С с низкими
скоростями охлаждения, которые сопутствуют газовой сварке, выделяют по границам
зерен карбиды хрома, являющиеся центрами коррозии металла.
Диаметр
проволоки выбирают приблизительно равным толщине основного металла при толщине
листов 1 - 6 мм.
При сварке в
большинстве случаев пользуются флюсами, например, марки НЖ-8 такого состава:
28% мрамора, 30% фарфора, 10% ферромарганца, 6% ферросилиция, 6% ферротитана и
20% двуокиси титана. Флюс разводится на жидком стекле и наносится на кромки
деталей в виде пасты. Сварка производится после высыхания флюса.
Сварка
двухслойных сталей. Двухслойные
стали состоят чаще всего из низкоуглеродистой стали и покрывающего ее слоя
коррозионно-стойкой стали. В качестве антикоррозионного слоя применяют
аустенитные стали марок 08Х18Н10Т, 08Х17Н13МЗТ и подобных им. Дуговая сварка
двухслойной стали по технике выполнения швов аналогична сварке однослойного
металла. Чаще всего шов выполняется вначале со стороны углеродистой стали,
затем наплавленный металл со стороны плакирующего слоя зачищается и сваривается
уже плакирующий слой. Электроды по химическому составу должны быть однородны с
металлом плакирующего, например для стали 08Х17Н16МЗТ применяют электроды с
покрытием марки НЖ-16 и проволоку марки Св-06Х19Н10МЗТ. Для сварки аустенитными
электродами применяют постоянный ток обратной полярности.
Изучить: 1. Что такое свариваемость металлов?
2. Как следует
разрабатывать технологию на сварку углеродистых сталей в зависимости от
содержания в них углерода?
3. Каковы особенности сварки высоколегированных сталей?
группа: 412
Предмет: Техника и технология частично механизированной сварки (наплавка) плавлением в защитном газе.
Тема урока: Характеристика низкоуглеродистых сталей и низколегированных сталей. Особенности технологии сварки (наплавки).
Низколегированные
конструкционные стали
Наибольшее использование в машиностроении,
судостроении и промышленном строительстве получили низкоуглеродистые и
среднеуглеродистые низколегированные стали, некоторые марки которых приведены в
табл. 5.3.
Наилучшей свариваемостью
обладают низкоуглеродистые стали (09Г2С, 16ГС, 15ГФД и др.), а также стали с
карбонитрид- ным упрочнением, содержащие кроме углерода азот и
карбидообразующие элементы (16Г2АФ, 14Г2АФД, 08Г2ФСБ и др.). Их применяют в
судо- и вагоностроении, для нефте- и газотрубопроводов, различных
резервуаров, сварных мостостроительных конструкций. В продовольственном
машиностроении стали 16ГС, 15ГФ используют для корпусов и днищ аппаратов,
фланцев и других деталей, работающих при температурах от —40 до +475 °С под
давлением.
Детали из сталей 20ХН, 18ХГТ,
12ХНЗ, 20ХНЗА и других чаще всего применяют после цементации с последующей
закалкой и низким отпуском. После обработки они имеют высокие прочность и твердость
поверхностного слоя (около 60 НЯС) и вязкую (20...30 НЯС) сердцевину. Иногда
закалку проводят в масле. При этом прочность сердцевины значительно повышается
(за счет бейнитного превращения) и возрастает работоспособность деталей.
Низкоуглеродистые легированные стали имеют
низкий порог хладноломкости (в области отрицательных температур).
После закалки и отпуска в них
получается хорошее сочетание высокой прочности (а02 =
1100...1300 МПа) с высокой пластичностью (8 = 9... 10 %, |/ = 40...45 %) и
вязкостью (КС11 = = 0,6...0,8 мДж/м2) (рис. 5.11), поэтому их используют и для
изготовления деталей без цементации.
Для мелких деталей (сечением
равным или меньшим 25 мм) используют более дешевые хромистые стали (20Х, 15ХФ,
20ХР и другие, свойства приведены в табл. 5.4).
Сталь 20Х разрешена для
изготовления деталей, непосредственно контактирующих с пищевыми средами, и ее
используют для изготовления деталей перекачивающих насосов, маслоотжимных
шнековых прессов и др.
Для крупных деталей (сечением
более 100 мм) ответственного назначения применяют хромоникелевые и
сложнолегированные стали (12ХНЗА, 20Х2Н4А, 18Х2Н4МАи др.).
Сталь |
Содержание
элементов, масс. % |
|||||
С |
Сг |
№ |
Мп |
Другие элементы |
||
Низкоуглеродистые
стали |
||||||
15ГФ |
0,12...0,18 |
0,30 |
0,30 |
0,9...
1,20 |
0,17...0,37 |
о,оз.-
олгу |
16ГС |
0,12...0,18 |
0,30 |
0,30 |
0,9...1,20 |
0,4...0,7 |
— |
20Х |
0,17...0,23 |
0,70...1,0 |
0,30 |
0,50...0,80 |
0,17...0,37 |
— |
ЗОХГТ |
0,24...0,32 |
1,0...1,3 |
— |
0,80...1,1 |
— |
|
20Х2Н4 |
0,16...0,22 |
1,25...1,65 |
3,25...3,65 |
< 0,8 |
0,17...0,37 |
|
10Г2С1Д |
< 0,12 |
0,30 |
0,30 |
1,3...1,65 |
0,8...1,1 |
— |
Среднеуглеродистые
стали |
||||||
35ХМ |
0,32...0,40 |
0,80...1,10 |
0,30 |
0,17...0,37 |
0,40...0,70 |
|
40ХН |
0,36...0,44 |
0,45...0,75 |
1,0...1,4 |
0,50...0,80 |
0,17...0,37 |
— |
50ХФА |
0,46...0,54 |
0,80...1,10 |
0,30 |
0,50...0,80 |
0,17...0,37 |
о о К) о о < : |
ЗОХГСА |
0,28...0,34 |
0,80...1,10 |
0,30 |
0,80...1,10 |
0,9...1,20 |
— |
40ХН2МА |
0,37...0,44 |
0,60...0,90 |
1,25...1,65 |
0,50...0,80 |
0,17...0,37 |
|
38ХНЗМФ |
0,30...0,42 |
1,2...1,5 |
3,0...3,4 |
< 0,8 |
0,17...0,37 |
|
60С2А |
0,58...0,63 |
0,30 |
0,30 |
0,60...0,90 |
1,6...2,0 |
— |
Рис. 5.11. Зависимость механических свойств стали 40 от температуры
отпуска
Таблица 5.4
Режимы
термической обработки и механические свойства низкоуглеродистых легированных
конструкционных сталей
Сталь |
Режим
термической обработки |
а0,2> МПа |
аВ’ МПа |
6, % |
V, % |
15ГФ |
Без
термической обработки |
340 |
480 |
21 |
— |
16ГС |
Без
термической обработки |
315 |
480 |
21 |
— |
Закалка +
отпуск |
390 |
510 |
18 |
— |
|
10Г2С1Д |
Без
термической обработки |
350 |
500 |
21 |
— |
Закалка +
отпуск |
390 |
530 |
19 |
— |
|
20Х |
Нормализация
880—900 °С, охлаждение на воздухе |
350 |
590 |
18 |
45 |
Закалка с
880 °С + закалка с 770—820 °С + отпуск при 180 °С, охлаждение на воздухе |
640 |
785 |
И |
40 |
Среднеуглеродистые
легированные стали (табл. 5.5) содержат 0,3...0,5 % С, 3...5 % легирующих
элементов (Сг, N1, Мп, 51, XV, Мо) и небольшое количество элементов,
измельчающих зерно СП, N6, гг, V).
Особенности свариваемости
Основными требованиями при
сварке этих сталей являются: обеспечение равнопрочности металла сварного
соединения и основного металла; отсутствие дефектов сварного соединения;
заданная геометрия сварного шва; производительность и экономичность процесса
сварки [1, 11 - 13]. Эти требования обеспечиваются при выборе соответствующих
сварочных материалов и доли участия основного металла в формировании шва в
широком диапазоне параметров режима различных способов сварки плавлением. Вместе
с тем с увеличением содержания углерода и легирующих элементов в сталях, а
также толщины свариваемых элементов повышается чувствительность к закалке,
образованию горячих и холодных трещин, а при сварке термоупрочненных сталей - к
разупрочнению. Поэтому одной из основных отличительных технологических
особенностей сварки низколегированных сталей, по сравнению с
низкоуглеродистыми, является более узкий диапазон параметров режима сварки,
обеспечивающих требуемые свойства сварных соединений. Проблемы свариваемости
высокопрочных низколегированных сталей освещены в работах [3, 7, 9, 13].
Анализ основных проблем сварки конструкционных низкоуглеродистых
низколегированных сталей, возникавших в течение последних десятилетий,
показывает, что наибольшей явилось старение сварных соединений на мягких
сталях. Случаи аварий вследствие хрупких изломов на сварных конструкциях имели
место на кораблях, мостах и специальных конструкциях, что сдерживало дальнейшее
расширение области применения сварки. Уменьшение склонности стали к старению
решается снижением содержания растворенного в стали азота до 0,003% и менее,
или же связыванием азота и получением стабильных нитридов (например, алюминия)
или карбонитридов (например, титана, циркония, ниобия). Стремление получить
стали, стойкие к старению, привело в последние годы к разработке сталей нового
типа - микролегированных сталей. Микролегированные стали, а
особенно последних марок с низким легированием марганцем, молибденом и
микролегированием ниобием представляют собой последние достижения
металлургического развития конструкционных свариваемых сталей [3].
Вопросы свариваемости микролегированных сталей до сих пор продолжают оставаться
актуальными. Исследовано влияние ниобия на структуру и механические свойства
швов, выполненных сваркой под флюсом [5]. Для экспериментов было отобрано шесть
плавок низкоуглеродистых сталей, имеющих примерно одинаковый химический состав
и содержащих от 0 до 0,085% ниобия (Nb). Результаты опытов показали, что
ударная вязкость металла шва в значительной степени зависит от количества
игольчатого феррита в структуре и величины предела текучести т. В высокопрочных швах (с низким содержанием кислорода
и значительным количеством игольчатого феррита в структуре) легирование ниобием
оказывает рафинирующее действие на структуру металла шва. В швах с низкой
прочностью и высоким содержанием кислорода введение ниобия способствует
существенному снижению количества игольчатого феррита. Для определения конечной
структуры металла шва в зависимости от скорости охлаждения и прочности
необходимо использовать данные термокинетических диаграмм.
На основе термокинетического анализа и дилатометрических исследований построены
диаграммы превращений при непрерывном охлаждении для металла шва четырех
углеродисто-марганцевых сталей, легированных ниобием. После охлаждения с
различной скоростью в металле шва возможно получение различной микроструктуры:
доэвтектоидного, пластинчатого, игольчатого и реечного феррита. С помощью
диаграмм изучено влияние ниобия (от 0 до 0,03%) на характер превращения в
сварных швах различной прокаливаемости. В шве состава (в %): С = 0,1; Mn =
1,35; Si = 0,31, полученном сваркой под флюсом, ниобий увеличивает
прокаливаемость и подавляет ферритное и перлитное превращения, снижает
количество феррита по границам зерен и увеличивает содержание игольчатого
феррита в металле шва. Снижение температуры образования игольчатого феррита
приводит к некоторому его измельчению. В металле шва, содержащем (в %) С =
0,09; Мn = 1,0; Si = 0,15, полученном с использованием карбонатного флюса,
ниобий способствует образованию пластинчатого феррита и подавляет образование
доэвтектоидного феррита.
Весьма положительное влияние
на повышение прочности стали оказывает комплексное легирование ниобием и
ванадием ( сумма обеих примесей не должна превышать 0,15%). При содержании в
стали 0,16-0,18 % С и ~1,5 % Мn временное сопротивление достигает 560-580 МПа,
а предел текучести металла толщиной 16-20 мм 450 МПа, ударная вязкость такой
стали при низких температурах высокая: при - 40 0С она
больше 300 кДж/м2. Падение вязкости стали комплексного легирования
после высокого отпуска не наблюдается.
Исследовано влияние ниобия и
ванадия на механические свойства и склонность к хрупкому разрушению металла
швов, сваренных под флюсом. Увеличение концентрации ванадия или ниобия в шве
ведет к повышению прочности и ухудшению пластических свойств. Причиной
охрупчивания с увеличением микролегирования швов является выделение
мелкодисперсных карбидов ниобия и ванадия и карбонитридов, ведущее к развитию напряжений
второго рода. Свариваемость микролегированных сталей целесообразно оценивать по
индексам свариваемости:


; . (1)
Они учитывают влияние состава
и позволяют классифицировать стали по их свариваемости при оптимальном способе
сварки. При СW <
0,35 % сталь можно сваривать ручной дуговой сваркой электродами с основным
(фтористо-кальциевым) покрытием, механизированной сваркой под флюсом и в CO2. Если Сw лежит
в пределах 0,35-0,45%, то при сварке под флюсом погонную энергию следует
уменьшить до 35 кДж/см. При Сw > 0,45% для получения хороших пластических свойств
сварку ведут только электродами с фтористо-кальциевым покрытием
В связи с тенденцией к
производству оборудования большой единичной мощности в различных отраслях
промышленности возрос объем применения толстостенного проката из
низколегированных сталей, свариваемость которого представляет определенные
сложности. При сварке конструкций из толстостенного проката применяются:
электрошлаковая сварка, сварка в узкую разделку механизированными дуговыми
способами, электронно-лучевая сварка.
Одним из наиболее эффективных
видов сварки конструктивных элементов большой толщины продолжает оставаться
электрошлаковая сварка, расширившая возможности производства корпусов, котлов,
продукции тяжелого машиностроения и станкостроения, роторов турбин, а также
строительных и мостовых конструкций. Главной проблемой свариваемости при
электрошлаковой сварке являются низкие пластические свойства крупнозернистой
перегретой околошовной зоны, достигающей в случае сварки крупных элементов конструкций
(толщиной >100 мм) ширины 5мм и более. Появление такой зоны требует полной
перекристаллизационной термической обработки. Необходимость выполнения
последующей нормализации сварных соединений с целью повышения их
хладностойкости и связанное с этим увеличение трудоемкости и энергоемкости
производства сдерживают применение этого способа сварки в промышленности.
Поэтому одна из наиболее важных проблем свариваемости сталей состояла в
разработке материала, технологии и термической обработки, которые позволили бы
применять электрошлаковую сварку в случае толстостенных деталей без последующей
нормализации.
Со временем определился ряд
подходов к решению данной проблемы. Одним из направлений, обеспечивающих
применение электрошлаковой сварки, является разработка новых сталей, не
требующих последующей нормализации [7]. За счет дополнительного легирования
марганцем, хромом
( 2%), молибденом ( 1%), при
одновременном уменьшении содержания углерода до 0,1% удается обеспечить
повышенную внутризеренную дисперсность металла шва и околошовной зоны сварных
соединений, выполненных электрошлаковой сваркой. В перегретой зоне должна быть
бейнитная или бейнитно-мартенситная структура без полиэдрического феррита,
должно быть уменьшено содержание углерода (до 0,10-0,12%) с целью устранения
видманштеттовой структуры и повышения ударной вязкости металла участка
перегрева и, естественно, снижено содержание примесей (загрязнений).
Измельчение бывшего аустенитного зерна на участке перегрева, например, путем
микролегирования стали нитридами алюминия, является желательным, но не
непременным условием получения стали, свариваемой электрошлаковой сваркой без
нормализации. Наиболее просто и надежно легировать сталь элементами, которые
увеличивают дисперсность, разориентированность внутризеренной структуры,
устраняют видманштеттову структуру, подавляют выделение избыточного феррита по
границам зерен или увеличивают его стойкость против хрупких разрушений. В этих
целях хромомолибденовые стали целесообразно легировать повышенным (до ~2 %)
количеством марганца, хрома или небольшими добавками бора. Сталь,
предназначенную для электрошлаковой сварки без последующей нормализации,
желательно микролегировать церием, что позволяет увеличить чистоту границ
зерен. В таких сталях не должно быть микролегирующих элементов, образующих
карбиды по границам зерен и вследствие этого резко повышающих критическую
температуру хрупкости металла участка перегрева (например, 0,05-0,12 % Тi или
0,05-0,11 % Zr ).
Как показали исследования
механических свойств, включающие испытания по методам механики разрушения,
сварные соединения стали 10Х2ГМ, выполненные электрошлаковой сваркой, обладают
достаточным запасом вязкости вплоть до температуры - 40 0С [7]. Все
же нельзя утверждать, что данная проблема уже решена на основе этого
направления.
Другое направление связано с
регулированием структуры и свойств сварных соединений в процессе
электрошлаковой сварки. Оно характеризуется многообразием способов и
технологических приемов. Известны способы повышения прочностных и пластических характеристик
металла сварного шва за счет его легирования специальными элементами -
модификаторами (титаном, молибденом, ванадием и др.), способствующими
измельчению первичной столбчатой структуры [2, 4]. При электрошлаковой сварке
по способу, предложенному в работе [4], между свариваемыми деталями помещают
промежуточные прокладки, представляющие собой сетку из низкоуглеродистой стали,
в которую запрессована порошковая смесь из раскислителей и легирующих
элементов. Хорошие результаты достигнуты при электрошлаковой сварке
низколегированных и низкоуглеродистых сталей порошковой проволокой [2]. Способ
высокоскоростной электрошлаковой сварки плавящимся мундштуком в узкий зазор
предназначен для сварки низколегированной стали, эксплуатируемой при низких
температурах. Легирование сварного шва осуществляется через трубчатую
электродную проволоку, заполненную флюсом основного типа, в который введены
модификаторы. Рассмотренные способы приводят к повышению хладностойкости
металла шва, однако, существенно не влияют на свойства участка перегрева зоны
термического влияния сварных соединений.
Большинство из известных
технологических приемов базируется на регулировании теплового режима в зоне
сварки величиной погонной энергии. Например, известен способ электрошлаковой
сварки, при котором перед подачей электрода в шлаковую ванну осуществляют его
предварительный подогрев за счет увеличения вылета или током от независимого
источника [1]. На этом же принципе основан способ электрошлаковой сварки с
одновременным оплавлением кромок основного металла при помощи дополнительного
электрода, вводимого в шлаковую ванну [14]. Для увеличения производительности
сварки при одновременном уменьшении перегрева металла околошовной зоны
предложен способ электрошлаковой сварки с присадкой дополнительного материала в
виде обесточенной проволоки или пластины, помещаемой в сварочный зазор [6].
Этот способ позволяет примерно в полтора раза повысить скорость сварки и
соответственно ограничить погонную энергию. Предложен способ, ограничивающий
тепловложение в процессе электрошлаковой сварки, за счет дополнительной подачи
в шлаковую ванну порошкообразного присадочного металла. Процесс плавления
такого рода металла не сопровождается сильным перегревом, поскольку
теплонасыщение гранул происходит мгновенно. При этом примерно в четыре раза
сокращается время выдержки околошовной зоны выше температуры интенсивного роста
зерна. Снижение степени перегрева металлической ванны, уменьшение ее объема и
времени пребывания в жидком состоянии, увеличение скорости нагрева и охлаждения
способствуют улучшению свойств металла шва.
Широкое распространение как в
нашей стране, так и за рубежом получили способы ограничения тепловложения при
электрошлаковой сварке при помощи уменьшения объема наплавленного металла.
Последнее достигается за счет изменения величины сварочного зазора, сваркой
тонкой проволокой в узкий зазор. Например, уменьшение ширины зазора примерно на
45% приводит к увеличению скорости сварки и снижению тепловложения почти в два
раза. Это способствует уменьшению перегрева металла сварного соединения и
повышению его стойкости против хрупкого разрушения.
Одним из наиболее эффективных
оказалось направление, связанное с внешним воздействием на параметры
термических циклов посредством принудительного охлаждения сварного соединения
[8]. Этот способ электрошлаковой сварки позволяет непосредственно в процессе
сварки обеспечить заданный фазовый состав структуры, а следовательно, и
механические свойства сварных соединений. Это положение подтверждено
исследованиями, показавшими возможность обеспечения необходимого комплекса
эксплуатационных характеристик сварных соединений из термически упрочненных и
нормализованных сталей марок 10Г2ФР, 16ГС, 09Г2С. 20К, 20ЮЧ, 12ХМ толщиной
26-100 мм, выполненных электрошлаковой сваркой с регулированием термических
циклов. Известен положительный опыт сочетания различных методов для
регулирования параметров термических циклов, например, одновременное применение
сопутствующего охлаждения и дополнительной подачи в шлаковую ванну
порошкообразного присадочного металла (ППМ) при сварке стали марок 10Г2ФР,
12ХМ. Сопутствующее охлаждение оказывает существенное влияние на стадию
охлаждения, подача ППМ- на стадию нагрева. При одновременном применении ППМ и
сопутствующего охлаждения их воздействие на термические циклы суммируется и
позволяет наиболее эффективно оптимизировать их параметры.
Рассмотренные способы,
предложенные для снижения структурно-механической неоднородности сварных
соединений и повышения их хладностойкости, свидетельствуют о широкой возможности
применения электрошлаковой сварки при изготовлении сварных конструкций из
толстолистового металла за счет правильного выбора методов регулирования
процесса.
Одним из эффективных способов
повышения технологических и служебных характеристик металла сварных швов
(пластичности, ударной вязкости, жаро- и коррозионной устойчивости,
хладностойкости и пр.) является улучшение структуры путем микролегирования
редкоземельными металлами (РЗМ). Информационный взрыв, касающийся применения
РЗМ в машиностроительной металлургии, произошел в конце 60-х годов 20-го века и
направления его разрабатываются до сих пор. За рубежом наибольший интерес этой
проблеме уделяется в США и Японии. Из известных 17 редкоземельных металлов
применение в металлургической промышленности нашли иттрий и церий. РЗМ (в
частности, церий) могут выступать в роли раскислителей, десульфураторов,
модификаторов, а также микролегировать металл, изменяя его физико-механические
характеристики.
В публикациях, посвященных
применению РЗМ в сварочной технике, основное внимание уделяется исследованиям
по влиянию РЗМ на структуру и свойства наплавленного металла различных
конструкционных материалов, свойства присадочных проволок, стабильность горения
дуги.
Весьма перспективным является
микролегирование РЗМ сварочных материалов, применяемых для изготовления сварных
конструкций, эксплуатируемых в условиях пониженных температур, в которых
требования по пластичности и вязкости металла шва является основным критерием.
Исследовалось влияние РЗМ и их окислов на механико-технологические свойства
наплавленного металла. Металл для исследования наплавляли электродом типа Э-50
с введением в покрытие РЗМ - иттрия и окислов иттрия, церия, диспрозия, эрбия в
количестве 0,2 - 3,0 %. Выявлена экстремальная зависимость влияния иттрия на
ударную вязкость и пластические свойства. Прочностные характеристики не
претерпевают заметного изменения. При введении окислов РЗМ наблюдается
тенденция повышения всей гаммы механических свойств. Однако значение ударной
вязкости и пластичности ниже, чем при обработке наплавленного металла иттрием.
Особенно большой прирост получен по ударной вязкости при испытании на
хладностойкость наплавленного металла, микролегированного иттрием. Основной причиной
повышения хладностойкости низколегированного наплавленного металла,
обработанного иттрием, является рафинирование переплавленного металла, снижение
содержания примесей на границе зерен и придание этим примесям сфероидальной
формы. Кроме того микродобавки приводят к измельчению зерен феррита. Пластины
цементита перлитной составляющей, как установлено при
электронно-микроскопическом исследовании, дробятся, теряют ориентировку,
образуя прерывистые цепочки по границам зерен, края их округляются. При введении
~ 1% иттрия внутри и по границам зерен начинает образовываться новая фаза,
большей частью овальной формы, имеющая светло-розовую окраску на нетравленом
шлифе. Новая фаза обогащена иттрием, что установлено микрорентгеноспектральным
анализом.
Обработка наплавленного
металла иттрием влияет на форму, содержание и размеры неметаллических
включений. Крупные неправильной формы включения располагаются, как правило,
цепочками, диспергируют, приобретают шаровидную форму и равномерно
распределяются по сечению. Количество их уменьшается. Однако введение иттрия
выше оптимального содержания приводит к увеличению количества неметаллических
включений, не меняя их форму и расположение. Повышение содержания иттрия до 3%
приводит к образованию грубых игольчатых структур бейнита и
структурно-свободного феррита, что влечет за собой повышение характеристик
прочности, падение показателей пластичности.
Введение РЗМ как в основной
металл, так и в сварочные материалы существенно влияет на технологические
характеристики и стабильность процесса сварки. Изучено влияние РЗМ, вводимого в
сталь в количестве 0,013; 0,021и 0,03 %, на стабильность горения дуги, внешний
вид шва и разбрызгивание при сварке плавящимся электродом в защитной смеси СО2 - Аr. Установлено, что частота переноса металла в
моменты коротких замыканий и разбрызгивание металла уменьшаются при повышении
концентрации РЗМ в основном металле. При введении РЗМ в электродную проволоку
при сварке в аргоне легированных и низколегированных сталей, на постоянном токе
обратной полярности торец электрода резко заостряется благодаря этому
ограничивается блуждание дуги и устанавливается стабильный режим сварки с
короткими замыканиями даже при относительно высоком напряжении на дуге (частота
250 Гц). На прямой полярности явление заострения проволоки не наблюдается, но
из-за воздействия присадок РЗМ дуга горит стабильно. При сварке на переменном
токе присадки РЗМ позволяют применять источники питания с низким напряжением
холостого хода за счет снижения напряжения повторного зажигания дуги. Таким
образом, обработка сварочной ванны оптимальным количеством РЗМ оказывает
благотворное влияние на комплекс механико-технологических свойств
низколегированного наплавленного металла. РЗМ в процессе образования сварного
шва оказывают сложное действие - наряду с рафинированием модифицируют
наплавленный металл, что позволяет считать микролегирование РЗМ существенным
резервом повышения качества сварных соединений.
Изучить: 1. Характеристику низкоуглеродистых и низколегированных
сталей.
2. Особенности
сварки.
10.02.2022
группа: 412
Предмет: Техника и технология частично механизированной сварки (наплавка) плавлением в защитном газе.
Тема урока: Выбор материалов для наплавки изношенных деталей.
Наплавка — это процесс сварочного производства, при котором
на рабочую поверхность изделия, нагретую до оплавления, наносят расплавленный
металл. Таким образом можно получить поверхностный слой на изготовляемых деталях с заданными свойствами
(износостойкостью, кислотоупорностью или жаростойкостью) или восстановить слой
и размеры изношенного изделия. Наплавкой создаются биметаллические изделия,
высокая прочность и долговечность которых сочетаются с низкой стоимостью их
изготовления и меньшим расходом дефицитных материалов. При наплавке
(большинством способов), так же как и при сварке, образуется подвижная
сварочная ванна. В ее головной части основной металл расплавляется и
перемешивается с электродным металлом, а в хвостовой — происходят
кристаллизация расплава и образование металла шва. Наплавлять можно слои
металла как одинаковые по составу, структуре и свойствам с металлом детали, так
и значительно отличающиеся от них. Металл наплавки выбирают с учетом его
эксплуатационных требований и свариваемости.
Наплавка слоя с заданными свойствами затрудняется из-за перемешивания
наплавляемого металла с металлом самого изделия. Перемешивание и изменение
свойств наплавляемого металла тем больше, чем больше глубина проплавления
металла изделия. Поэтому при наплавке необходимо стремиться получить
минимальную глубину проплавления. Для этого следует использовать источники
теплоты, обеспечивающие равномерный нагрев поверхности металла с минимальной
глубиной проплавления. Обычно используют ацетилено-кислородное пламя,
электрическую дугу, электрошлаковый процесс, а в ряде случаев высокочастотный
нагрев.
Различают ручную, механизированную и автоматическую
наплавку. Две последние являются предпочтительными. Они позволяют
получить более высокие качество и производительность.
Обеспечение заданных свойств наплавленного металла при
механизированной наплавке достигается использованием электродной и наплавочной
проволок, а также специальной порошковой проволоки и порошковых лент. Наплавку
при этом производят под флюсом (плавленым и керамическим) или в среде защитных
газов. Порошковые проволоки, в шихту которых вводят минералы и газообразующие
вещества, обеспечивают выполнение наплавки без дополнительных защитных средств.
Наплавку можно производить на плоские, цилиндрические, конические,
сферические и другие поверхности в один или несколько слоев. Слой наплавки
может изменяться по толщине от долей миллиметра до сантиметров. При наплавке
слоев с заданными свойствами, как правило, химический состав наплавленного
металла значительно отличается от основного металла. В связи с этим при
наплавке необходимо выполнять ряд технологических требований. Основным из них
является минимальное разбавление наплавленного слоя основным металлом,
расплавляемым при наложении валиков. Поэтому при наплавке нужно обеспечить
получение наплавленного слоя с минимальным проплавлением основного металла. В
противном случае увеличивается доля основного металла в формировании
наплавленного слоя, он вызывает ненужное разбавление наплавленного металла
расплавляемым основным. Необходимо также обеспечить минимальную зону
термического влияния и минимальных напряжений и деформаций. Это достигается
путем уменьшения глубины проплавления регулированием параметров режима,
погонной энергии, увеличением вылета электрода, использованием широкой
электродной ленты и другими технологическими приемами. Существуют
различные приемы нанесения наплавленного слоя: ниточными валиками с перекрытием
один другого на 0,3...0,4 их ширины, широкими валиками, полученными за счет
поперечных к направлению оси валика колебаний электрода, электродными лентами и
др.
Расположение
валиков с учетом их перекрытия tn характеризуется
шагом наплавки (рис. 5.62).
Наплавку
криволинейных поверхностей тел вращения производят тремя способами (рис. 5.63):
по образующей тела вращения, по окружности и по винтовой линии. Наплавку
по образующей осуществляют отдельными валиками, как при наплавке
плоских поверхностей. Наплавку по окружностям также
выполняют отдельными валиками до полного замыкания их начального и конечного
Рис.
5.62. Схема наплавки слоев:
В — ширина валика; hn —
высота наплавки; hnр — глубина проплавления; 5Н —
шаг наплавки
Рис. 5.63.
Наплавка тел вращения: а — по образующей; б —
по окружности; в — по винтовой линии
участков со смещением на определенный шаг вдоль образующей линии. Деталь при
наплавке по винтовой линии вращается непрерывно, а источник нагрева
перемещается вдоль оси заготовки со скоростью, при которой одному ее обороту
соответствует смещение источника, равное шагу наплавки. При наплавке тел
вращения следует учитывать возможность стекания расплавленного металла в
направлении вращения заготовки. В этом случае источник нагрева нужно смещать в
сторону, противоположную направлению вращения, учитывая при этом длину
сварочной ванны и диаметр изделия (рис. 5.64).
Технологические
условия наплавки выбирают исходя из свойств материала наплавляемой заготовки.
Заготовки из низкоуглеродистых и низколегированных сталей обычно наплавляют без
их нагрева. На-
Рис. 5.64.
Смещение электрода при наплавке тел вращения: а — наклонно
расположенный электрод; б — вертикально расположенный
электрод
плавку деталей из средне- и высокоуглеродистых, легированных и
высоколегированных сталей часто выполняют с предварительным нагревом, а также с
последующей термообработкой для снятия внутренних напряжений. Термообработку
(отжиг) часто производят после наплавки для снижения твердости перед
последующей механической обработкой наплавленного слоя. Для наплавки в основном
применяют способы дуговой и электрошлаковой сварки. При выборе рационального
способа и технологии наплавки необходимо учитывать условия эксплуатации
наплавленного слоя и экономическую эффективность процесса.
При дуговой
наплавке под флюсом, так же как при сварке, нагрев и расплавление металла
производятся теплом дуги, которая горит между плавящимся электродом и основным
металлом под слоем флюса. Это один из основных видов механизированной и
автоматической наплавки. К его преимуществам можно отнести непрерывность и
высокую производительность, малые потери электродного металла, отсутствие
открытого излучения дуги. Наплавка под флюсом обеспечивает хороший внешний вид
наплавленного слоя (гладкая поверхность и плавный переход от одного
наплавленного валика к другому). В процессе наплавки легирование наплавленного
металла может осуществляться четырьмя основными способами (рис. 5.65).
1.
Использование легированной проволоки или ленты и обычных плавленых флюсов. При
этом применяют легированные сварочные проволоки и специальные наплавочные
проволоки и легированные ленты, в том числе спеченные. Наплавку осуществляют
под флюсами
Рис. 5.65.
Способы легирования наплавляемого металла: а — при помощи
сварочной проволоки; б — с использованием порошковой
проволоки; в — с применением керамического флюса; г — посредством
укладки
легированной
усадки
- (АН-20, АН-26 и др.), которые
выбирают в зависимости от состава электродного металла.
- 2. Применение порошковой проволоки
или порошковой ленты и обычных плавленых флюсов. Порошковая проволока или
лента расплавляется в дуге и образует однородный жидкий расплав. Эго дает
возможность получить наплавленный металл с общим содержанием легирующих
примесей до 40...50 %.
- 3. Применение обычной
низкоуглеродистой проволоки или ленты и легирующих флюсов (керамических).
Этот способ позволяет вводить в наплавленный металл до 35 % легирующих
элементов. При наплавке наиболее часто используют керамические флюсы
АНК-18 и АПК-19. Они обеспечивают хорошее формирование наплавленного
металла, легкую отделимость шлаковой корки, высокую стойкость
наплавленного металла против образования пор и трещин.
- 4. Использование обычной
низкоуглеродистой проволоки или ленты и обычных плавленых флюсов с предварительной
укладкой легирующих материалов на поверхность наплавляемого изделия. При
этом возможны предварительная засыпка или дозированная подача легирующих
порошков, предварительная укладка прутков или полосок легированной стали,
а также намазывание специальных паст на место наплавки и т.д. Во всех
случаях нанесенный легирующий материал расплавляется дугой и переходит в
наплавленный металл.
Между
сваркой и наплавкой много общего. Поэтому при наплавке используют то же
оборудование, что и при сварке соответствующими способами.
Для
предупреждения образования шлаковых включений и непроваров в наплавленном слое
при многослойной наплавке следует тщательно удалять шлаковую корку с предыдущих
слоев.
К дуговой
наплавке в защитных газах прибегают в тех случаях, когда невозможны
или затруднены подача флюса и удаление шлаковой корки. Преимуществами этого
вида наплавки являются возможность визуального наблюдения за процессом,
возможность механизации и автоматизации с применением серийного сварочного
оборудования (при наплавке заготовок в различных пространственных положениях,
глубоких отверстий, внутренних поверхностей, мелких заготовок и т.п.).
Наплавка в защитных
газах во многом аналогична наплавке под флюсом, отличие заключается лишь в том,
что вместо флюсовой осуществляется газовая защита зоны наплавки. Это
освобождает сварщика от необходимости засыпки флюса и удаления шлака. Для
уменьшения разбрызгивания металла наплавку в защитном газе следует выполнять
самой короткой дугой. Во избежание коробления заготовок наплавку плоских
поверхностей коробчатых заготовок нужно производить отдельными участками
«вразброс». Заготовки цилиндрической формы наплавляют по винтовой линии как
непрерывным валиком, так и с поперечными колебаниями электрода. Короткие
участки можно наплавлять продольными валиками вдоль оси заготовки. Однако при
этом могут возникнуть деформации, которые требуется уравновешивать. Для этого
наплавку каждого последующего валика необходимо выполнять с противоположной
стороны по отношению к уже наплавленному. При наплавке внутренних
цилиндрических и конических поверхностей следует использовать специальные
удлиненные мундштуки.
Наплавку
можно выполнять в среде углекислого газа (углеродистые и легированные стали),
аргона и гелия (высоколегированные стали, а также сплавы на основе алюминия и
магния) и азота (медь и некоторые ее сплавы, поскольку азот ведет себя по
отношению к ним нейтрально). При этом можно применять как плавящийся, так и
неплавящийся электрод. Неплавящийся вольфрамовый электрод обычно используют для
наплавки в среде аргона и гелия. Наиболее часто наплавку выполняют в углекислом
газе плавящимся электродом на постоянном токе обратной полярности. Углекислый
газ окисляет расплавленный металл. Поэтому в наплавочную проволоку обязательно
добавляют раскислители (марганец, кремний и др.). Наплавку производят как
проволокой сплошного сечения, так и порошковой. Для наплавки заготовок из
углеродистых и низколегированных сталей с целью восстановления их размеров
используют сварочные проволоки сплошного сечения Св-08ГС, СВ-08Г2С, CB-12FC, а
также наплавочные Нп-40, Нп-50, Нп-ЗОХГСА и др. Для получения наплавленного
слоя с особыми свойствами применяют порошковые проволоки.
Недостатком
описанного способа является то, что при наплавке в среде углекислого газа
жидкий металл сильно разбрызгивается. Это приводит к налипанию брызг на
мундштук и засорению сопла горелки. Помимо этого возможность сдувания газовой
струи ветром осложняет наплавку на открытом воздухе.
Дуговая
наплавка порошковыми проволоками с внутренней защитой основана на введении в
сердечник проволоки кроме легирующих компонентов шлакообразующих и
газообразующих материалов. Флюсовая и газовая защита при наплавке такой
проволокой не нужна. Легирующие элементы порошковой проволоки переходят в шов,
а газо- и шлакообразующие материалы обеспечивают нужную защиту металла от азота
и кислорода воздуха. Тонкая пленка расплавленного шлака в зоне дуги покрывает капли
жидкого металла и изолирует последние от воздуха, а разложение газообразующих
материалов приводит к образованию потока защитного газа. На поверхности
наплавленного валика после его затвердевания формируется тонкая шлаковая корка,
которую можно удалять при наплавке последующих слоев. Для наплавки используют
различные самозащитные порошковые проволоки: для создания низкоуглеродистых
слоев — сварочные (типа ПП-ЛНЗ и др.), для получения слоев с особыми свойствами
— специальные.
Технология
выполнения наплавки самозащитной порошковой проволокой аналогична технологии
наплавки в среде углекислого газа. Открытая дуга позволяет точно направлять
электрод, следить за формированием наплавленного слоя. Это имеет большое
значение при наплавке заготовок, имеющих сложную форму. Данный способ не
требует сложной аппаратуры по сравнению с наплавкой под флюсом и в среде
защитного газа. Наплавку можно выполнять на открытом воздухе. При этом
увеличивается производительность процесса по сравнению с наплавкой под флюсом и
в защитных газах, снижается себестоимость наплавляемого металла.
Рис.
5.66. Схема плазменной наплавки с вдуванием порошка в дугу
Плазменная
наплавка и напыление заключаются
в том, что нагрев присадочного и основного металлов производится сжатой дугой
или газовой плазмой, выделенной или совпадающей со столбом дуги. Механизм
образования наплавленного слоя аналогичен механизмам других способов дуговой
наплавки.
В качестве
наплавочных материалов также применяют порошки. Схема плазменной наплавки с
вдуванием порошка в дугу показана на рис. 5.66.
Дуга
возбуждается вольфрамовым электродом 1 и внутренним
соплом 2. Плазмообразующий газ, проходя через дугу, создает
плазменную струю 3 косвенного действия. Эта струя расплавляет
присадочный порошок. Другая дуга прямого действия 4, которая
горит между электродом 1 и основным металлом 5, совпадает с
плазменной струей прямого действия, нагревающей поверхность до нужной
температуры и тем самым обеспечивающей сплавление порошка и основного металла.
Изменяя силу тока сжатой дуги прямого действия, проплавление основного металла
можно свести до минимума. Толщину наплавленного слоя можно варьировать в
пределах 0,3... 10,0 мм с разбавлением основным металлом от 3 до 30 %. От
указанных дуг получает теплоту и основной металл. Регулировать долю основного
металла и производительность наплавки можно путем изменения силы тока. В этом
случае наплавляемое изделие в сварочную цепь не включают.
При плазменной
наплавке в качестве защитных газов используют аргон, азот, углекислый газ,
смеси аргона с гелием или азотом и др. В качестве плазмообразующего могут
применяться аргон, гелий, углекислый газ, воздух и г.д. Стабильное протекание
процесса наплавки обеспечивают неплавящиеся электроды из материала,
позволяющего без разрушения выдерживать нагревание до высоких температур.
Применяют электроды из чистого вольфрама или с присадками диоксида тория,
оксидов лантана и иттрия. Этот вид наплавки обеспечивает малую глубину
проплавления основного металла, возможность наплавки тонких слоев, высокое
качество и гладкую поверхность наплавленного металла.
Плазменный
нагрев можно также применять для напыления поверхностных слоев. Но сравнению с
наплавкой оно имеет ряд особенностей. Напыление представляет
собой процесс нанесения па неоплав- ленную поверхность изделия металлических
слоев из частиц материала, нагретых до температуры плавления или близкой к
плавлению. Присадочный материал в виде проволок подается в сжатую дугу и там
нагревается струей газа, а затем с большой скоростью подается на поверхность
изделия. Толщину напыленного слоя можно изменять от сотых до десятых долей
миллиметра. Более толстые слои не напыляют, так как они склонны отслаиваться от
поверхности изделия (откалываться). Напыление можно выполнять как металлами и
сплавами, так и различного вида соединениями: оксидами, карбидами, нитридами и
т.п.
Технологически
в отличие от наплавки напыление производят по способу косвенного нагрева
выделенной дуговой плазмой. Расстояние от сопла горелки до изделия при
проплавке составляет 6...25 мм, а при напылении — 50... 120 мм и более.
Напыленные слои материала имеют меньшую плотность и большую пористость по
сравнению с наплавленными и более склонны к откалыванию от поверхности изделия
при нарушении технологии. Однако в этих слоях практически отсутствует
разбавление основным металлом.
Рис.
5.67. Схема электрошлаковой наплавки на вертикальную поверхность
Сущность
процесса электрошлако - вой наплавки (рис. 5.67) заключается в
том, что в пространстве, которое образовано поверхностью наплавляемого
изделия 1 и формирующим кристаллизатором 4, охлаждаемым
водой, создается ванна расплавленного шлака 3, в которую
подается электродная проволока 5.
Ток, проходя
между электродом и изделием, нагревает шлаковую ванну до температуры выше 2000
°С. В результате этого электродный и основной металлы оплавляются, образуя
металлическую ванну. При затвердевании последней формируется наплавленный
слой 2.
Для
реализации электрошлаковой наплавки различных поверхностей нужно обеспечить
достаточно глубокую ванну, которую проще всего получить при вертикальном или
наклонном расположении деталей. По сравнению с дуговой наплавкой это менее
универсальный способ. Однако он весьма эффективен в случаях, когда на изделие
нужно наплавить слой металла значительной толщины (более 14... 16 мм).
Использование большой силы тока, а также электродов большого сечения
обеспечивает высокую производительность (до 150 кг наплавленного металла в
час).
В качестве
присадочного металла используют наплавочные проволоки (одну или несколько),
электродные ленты, пластины, а также стержни большого сечения, иногда и трубы.
Последние применяют для наплавки цилиндрических поверхностей изделий. Наплавку
обычно осуществляют с флюсами АН-8, АН-22 и т.д.
Вибродуговая
наплавка (рис.
5.68) обычно используется для наплавки заготовок типа тел вращения диаметром от
8 мм и более. Ее сущность заключается в том, что сварочная проволока 3 подается
с постоянной скоростью в направляющий мундштук 5 и периодически соприкасается в
точке А с поверхностью заготовки 1, которая равномерно
вращается. Концу проволоки сообщается колебательное перемещение от
вибратора 4. При наплавке через мундштук 2 непре-
Рис.
5.68. Схема вибродуговой наплавки
рывно
подается струя слабого раствора соды. Она охлаждает заготовку и защищает зону
сварки от контакта с атмосферой.
Нагрев
основного и электродного металла до расплавления осуществляется теплотой,
которая выделяется в результате периодически повторяющихся электрических
разрядов, т.е. прерывисто горящей электрической дуги. Наплавленный слой
образуется при кристаллизации расплавленного основного и электродного металла.
Малая длительность и прерывистость горения электрической дуги обусловливается
вибрациями электродной проволоки, создаваемыми электромагнитными или
механическими вибраторами. При вибрациях возникают короткие замыкания из-за
соприкосновения электродной проволоки и наплавляемого изделия (основного
металла), а во время отрыва проволоки появляется ток большой силы и загорается
электрическая дуга.
При наплавке
осуществляются следующие движения: вращение наплавляемого изделия,
поступательное движение вибродуговой головки вдоль продольной оси наплавляемого
изделия, подача проволоки в зону дуги и вибрация проволоки. Питание
производится от выпрямителей, сварочных генераторов, а также от низковольтных
трансформаторов с вторичным напряжением 12...16 В и более. Высокие показатели
достигаются при наплавке на постоянном токе обратной полярности. В сварочную
цепь обычно включают индуктивность, значение которой выбирают в зависимости от
частоты вибрации электродной проволоки, напряжения, рода тока и других
факторов. Для наплавки используют сварочные проволоки диаметром 0,8...2,0 мм.
Для защиты расплавленного металла от взаимодействия с окружающей средой наплавку
выполняют в струях жидкостей или защитных газов, а также под слоем флюса.
Применяются водные растворы кальцинированной соды; смеси кальцинированной соды,
мыла и глицерина; эмульсии глицерина.
Для ручной
дуговой наплавки па углеродистую сталь применяют электроды Э42...Э100.
Наилучших результатов достигают при использовании фтористо-кальциевых покрытий
УОНИ-13/50, У-340/50 и других покрытий этого типа. Наплавка такими электродами
дает достаточную плотность и мелкозернистость наплавленного слоя. Хорошие результаты
обеспечивают электроды ОЗС-4 и МР-3 типа Э-46 и электроды АНО-1, АНО-2, АНО-3
типа Э-42. Ими можно производить наплавку на переменном и постоянном токах.
Для
получения наплавленного слоя, например, с износостойкими свойствами необходимо
использовать специальные электроды. Режимы наплавки обычно указывают в паспорте
для каждой марки электрода. Вибродуговую наплавку часто используют для
восстановления изношенных шеек валов машин и механизмов различного служебного
назначения.
Прерывистость
наплавки обеспечивает зону термического влияния небольшой ширины, поэтому
возникающие деформации весьма малы, что особенно важно при наплавке
высокоточных сложных изделий.
При наплавке
в струе жидкости наплавленный металл быстро охлаждается, поэтому он обладает
повышенной твердостью и износостойкостью.
Вибродуговая
наплавка особенно эффективна при нанесении слоев металла малой толщины.
Недостатки этого процесса: сравнительно низкий коэффициент наплавки, низкая
производительность.
Металлизация
напылением — это
процесс нанесения жидкого пылеобразного металла на поверхность изделия. Его
сущность заключается в том, что к источнику нагрева (пламя, дуга, плазменная
струя) подают проволоку, которую нагревают и расплавляют. Образовавшийся жидкий
металл под давлением сжатого воздуха вылетает с большой скоростью из сопла
металлизатора в виде распыленных капель. Капли металла, ударяясь о напыляемую
поверхность, соединяются с нею и образуют слой покрытия.
Металлизация
легко восстанавливает изношенные поверхности деталей машин. Ее используют для
устранения внешних дефектов в отливках как из черных, гак и из цветных
металлов, а также для восстановления изношенных шеек, валов, поршней,
направляющих станин и т.д.
Напыление
осуществляют металлическими материалами в виде проволок (стальные, алюминиевые,
медные и т.д.) и неметаллическими материалами, подготовленными в виде порошков
(стекло, эмаль, пластмассы и т.д.). Металлизация менее эффективна по сравнению
с наплавкой. Металлизационный слой, состоящий из мелких поверхностно окисленных
частичек металла, имеет малую плотность, пониженную пластичность и прочность.
Изучить: 1. Основные виды наплавки.
2. Дуговая
наплавка в среде защитных газов.
3. Наплавка порошковыми проволоками.
08.02.2022
группа: 412
Предмет: Техника и технология частично механизированной сварки (наплавка) плавлением в защитном газе.
Тема урока: Наплавочные материалы: порошковые электродные ленты, спеченные электродные ленты, флюсы для наплавки. Порошковая электродная лента
Для
широкослойной наплавки все большее применение находит порошковая
электродная лента рис 35. , состоящая из двух или одной тонких (0,3-0,5 мм)
стальных (сталь 08кп) лент и засыпанной между ними шихты.
Шихту дляленты получают так же, как и для порошковой проволоки. Изготовляют
порошковую ленту на специальных станках.
Порошковая
лента состоит из оболочки из мягкой холоднокатаной ленты и сердцевины из
смеси порошков графита, ферросплавов, чистых металлов и других
компонентов. Порошковую ленту изготовляют из отдельных секций
шириной 12-14 мм на специальном станке, азатем собирают в широкую ленту.
Широкое
применение в промышленности находят порошковые ленты ИЭС им. Е.О. Патона. Ленты
выпускаются шириной 30-60мм и толщиной 1,5-3,0 мм. Широкая порошковая лента,
состоящая из одной секции, не всегда обеспечивает необходимую
однородность наплавленного металла, так как при ее изготовлении трудно
обеспечивать равномерное распределение материалов шихты по всему сечению ленты.
Поэтому для наплавки преимущественно применяют ленту небольшой ширины (до 30
мм).
Наиболее
часто используют порошковые ленты ПЛ-У30Х30Г3ТЮ, ПЛ-АН101
(ПЛ-У300Х25Н3С3), ПЛ-АН102 (ПЛ-30Х25Н4С4) и др.
Ленту марки ПЛ-У30Х30Г3ТЮ применяют для износостойких наплавок режущих
органов землеройных машин, деталей строительных машин.
Механизированная
наплавка пояса конуса и чаш засыпных аппаратов производится лентой
ПЛ-У300Х25Н3С3-11, ПЛ-30Х25Н4С4. Этой лентой наплавляют режущие кромки
грейферов, лопастей бетоносмесительных машин, катков тракторов, зубьев и ковшей
погрузчиков и др.
Важным
преимуществом этих порошковых лент является возможность их использования
без применения флюсов или защитных газов. Это достигнуто за счет
введения в ленту кроме легирующих элементов веществ, обеспечивающих
хорошее раскисление сварочной ванны и связывание азота воздуха в стойкие
нитриды. При наплавке лентой ПЛ-АН101 достигается минимальное
разбрызгивание электродного металла и высокая однородность
химического состава наплавленного металла.
Концентрация
вредных выделений при наплавке лентой ПЛ-АН101 ниже, чем при наплавке другими
порошковыми лентами.
Основными требованиями при
сварке этих сталей являются: обеспечение равнопрочности металла сварного
соединения и основного металла; отсутствие дефектов сварного соединения;
заданная геометрия сварного шва; производительность и экономичность процесса
сварки [1, 11 - 13]. Эти требования обеспечиваются при выборе соответствующих
сварочных материалов и доли участия основного металла в формировании шва в
широком диапазоне параметров режима различных способов сварки плавлением. Вместе
с тем с увеличением содержания углерода и легирующих элементов в сталях, а
также толщины свариваемых элементов повышается чувствительность к закалке,
образованию горячих и холодных трещин, а при сварке термоупрочненных сталей - к
разупрочнению. Поэтому одной из основных отличительных технологических
особенностей сварки низколегированных сталей, по сравнению с
низкоуглеродистыми, является более узкий диапазон параметров режима сварки,
обеспечивающих требуемые свойства сварных соединений. Проблемы свариваемости
высокопрочных низколегированных сталей освещены в работах [3, 7, 9, 13].
Анализ основных проблем сварки конструкционных низкоуглеродистых
низколегированных сталей, возникавших в течение последних десятилетий,
показывает, что наибольшей явилось старение сварных соединений на мягких
сталях. Случаи аварий вследствие хрупких изломов на сварных конструкциях имели
место на кораблях, мостах и специальных конструкциях, что сдерживало дальнейшее
расширение области применения сварки. Уменьшение склонности стали к старению
решается снижением содержания растворенного в стали азота до 0,003% и менее,
или же связыванием азота и получением стабильных нитридов (например, алюминия)
или карбонитридов (например, титана, циркония, ниобия). Стремление получить
стали, стойкие к старению, привело в последние годы к разработке сталей нового
типа - микролегированных сталей. Микролегированные стали, а
особенно последних марок с низким легированием марганцем, молибденом и
микролегированием ниобием представляют собой последние достижения
металлургического развития конструкционных свариваемых сталей [3].
Вопросы свариваемости микролегированных сталей до сих пор продолжают оставаться
актуальными. Исследовано влияние ниобия на структуру и механические свойства
швов, выполненных сваркой под флюсом [5]. Для экспериментов было отобрано шесть
плавок низкоуглеродистых сталей, имеющих примерно одинаковый химический состав
и содержащих от 0 до 0,085% ниобия (Nb). Результаты опытов показали, что
ударная вязкость металла шва в значительной степени зависит от количества
игольчатого феррита в структуре и величины предела текучести т. В высокопрочных швах (с низким содержанием кислорода
и значительным количеством игольчатого феррита в структуре) легирование ниобием
оказывает рафинирующее действие на структуру металла шва. В швах с низкой
прочностью и высоким содержанием кислорода введение ниобия способствует
существенному снижению количества игольчатого феррита. Для определения конечной
структуры металла шва в зависимости от скорости охлаждения и прочности
необходимо использовать данные термокинетических диаграмм.
На основе термокинетического анализа и дилатометрических исследований построены
диаграммы превращений при непрерывном охлаждении для металла шва четырех
углеродисто-марганцевых сталей, легированных ниобием. После охлаждения с
различной скоростью в металле шва возможно получение различной микроструктуры:
доэвтектоидного, пластинчатого, игольчатого и реечного феррита. С помощью
диаграмм изучено влияние ниобия (от 0 до 0,03%) на характер превращения в
сварных швах различной прокаливаемости. В шве состава (в %): С = 0,1; Mn =
1,35; Si = 0,31, полученном сваркой под флюсом, ниобий увеличивает
прокаливаемость и подавляет ферритное и перлитное превращения, снижает
количество феррита по границам зерен и увеличивает содержание игольчатого
феррита в металле шва. Снижение температуры образования игольчатого феррита
приводит к некоторому его измельчению. В металле шва, содержащем (в %) С =
0,09; Мn = 1,0; Si = 0,15, полученном с использованием карбонатного флюса,
ниобий способствует образованию пластинчатого феррита и подавляет образование
доэвтектоидного феррита.
Весьма положительное влияние
на повышение прочности стали оказывает комплексное легирование ниобием и
ванадием ( сумма обеих примесей не должна превышать 0,15%). При содержании в
стали 0,16-0,18 % С и ~1,5 % Мn временное сопротивление достигает 560-580 МПа,
а предел текучести металла толщиной 16-20 мм 450 МПа, ударная вязкость такой
стали при низких температурах высокая: при - 40 0С она
больше 300 кДж/м2. Падение вязкости стали комплексного легирования
после высокого отпуска не наблюдается.
Исследовано влияние ниобия и
ванадия на механические свойства и склонность к хрупкому разрушению металла
швов, сваренных под флюсом. Увеличение концентрации ванадия или ниобия в шве
ведет к повышению прочности и ухудшению пластических свойств. Причиной
охрупчивания с увеличением микролегирования швов является выделение
мелкодисперсных карбидов ниобия и ванадия и карбонитридов, ведущее к развитию напряжений
второго рода. Свариваемость микролегированных сталей целесообразно оценивать по
индексам свариваемости:
; . (1)
Они учитывают влияние состава
и позволяют классифицировать стали по их свариваемости при оптимальном способе
сварки. При СW <
0,35 % сталь можно сваривать ручной дуговой сваркой электродами с основным
(фтористо-кальциевым) покрытием, механизированной сваркой под флюсом и в CO2. Если Сw лежит
в пределах 0,35-0,45%, то при сварке под флюсом погонную энергию следует
уменьшить до 35 кДж/см. При Сw > 0,45% для получения хороших пластических свойств
сварку ведут только электродами с фтористо-кальциевым покрытием
В связи с тенденцией к
производству оборудования большой единичной мощности в различных отраслях
промышленности возрос объем применения толстостенного проката из
низколегированных сталей, свариваемость которого представляет определенные
сложности. При сварке конструкций из толстостенного проката применяются:
электрошлаковая сварка, сварка в узкую разделку механизированными дуговыми
способами, электронно-лучевая сварка.
Одним из наиболее эффективных
видов сварки конструктивных элементов большой толщины продолжает оставаться
электрошлаковая сварка, расширившая возможности производства корпусов, котлов,
продукции тяжелого машиностроения и станкостроения, роторов турбин, а также
строительных и мостовых конструкций. Главной проблемой свариваемости при
электрошлаковой сварке являются низкие пластические свойства крупнозернистой
перегретой околошовной зоны, достигающей в случае сварки крупных элементов конструкций
(толщиной >100 мм) ширины 5мм и более. Появление такой зоны требует полной
перекристаллизационной термической обработки. Необходимость выполнения
последующей нормализации сварных соединений с целью повышения их
хладностойкости и связанное с этим увеличение трудоемкости и энергоемкости
производства сдерживают применение этого способа сварки в промышленности.
Поэтому одна из наиболее важных проблем свариваемости сталей состояла в
разработке материала, технологии и термической обработки, которые позволили бы
применять электрошлаковую сварку в случае толстостенных деталей без последующей
нормализации.
Со временем определился ряд
подходов к решению данной проблемы. Одним из направлений, обеспечивающих
применение электрошлаковой сварки, является разработка новых сталей, не
требующих последующей нормализации [7]. За счет дополнительного легирования
марганцем, хромом
( 2%), молибденом ( 1%), при
одновременном уменьшении содержания углерода до 0,1% удается обеспечить
повышенную внутризеренную дисперсность металла шва и околошовной зоны сварных
соединений, выполненных электрошлаковой сваркой. В перегретой зоне должна быть
бейнитная или бейнитно-мартенситная структура без полиэдрического феррита,
должно быть уменьшено содержание углерода (до 0,10-0,12%) с целью устранения
видманштеттовой структуры и повышения ударной вязкости металла участка
перегрева и, естественно, снижено содержание примесей (загрязнений).
Измельчение бывшего аустенитного зерна на участке перегрева, например, путем
микролегирования стали нитридами алюминия, является желательным, но не
непременным условием получения стали, свариваемой электрошлаковой сваркой без
нормализации. Наиболее просто и надежно легировать сталь элементами, которые
увеличивают дисперсность, разориентированность внутризеренной структуры,
устраняют видманштеттову структуру, подавляют выделение избыточного феррита по
границам зерен или увеличивают его стойкость против хрупких разрушений. В этих
целях хромомолибденовые стали целесообразно легировать повышенным (до ~2 %)
количеством марганца, хрома или небольшими добавками бора. Сталь,
предназначенную для электрошлаковой сварки без последующей нормализации,
желательно микролегировать церием, что позволяет увеличить чистоту границ
зерен. В таких сталях не должно быть микролегирующих элементов, образующих
карбиды по границам зерен и вследствие этого резко повышающих критическую
температуру хрупкости металла участка перегрева (например, 0,05-0,12 % Тi или
0,05-0,11 % Zr ).
Как показали исследования
механических свойств, включающие испытания по методам механики разрушения,
сварные соединения стали 10Х2ГМ, выполненные электрошлаковой сваркой, обладают
достаточным запасом вязкости вплоть до температуры - 40 0С [7]. Все
же нельзя утверждать, что данная проблема уже решена на основе этого
направления.
Другое направление связано с
регулированием структуры и свойств сварных соединений в процессе
электрошлаковой сварки. Оно характеризуется многообразием способов и
технологических приемов. Известны способы повышения прочностных и пластических характеристик
металла сварного шва за счет его легирования специальными элементами -
модификаторами (титаном, молибденом, ванадием и др.), способствующими
измельчению первичной столбчатой структуры [2, 4]. При электрошлаковой сварке
по способу, предложенному в работе [4], между свариваемыми деталями помещают
промежуточные прокладки, представляющие собой сетку из низкоуглеродистой стали,
в которую запрессована порошковая смесь из раскислителей и легирующих
элементов. Хорошие результаты достигнуты при электрошлаковой сварке
низколегированных и низкоуглеродистых сталей порошковой проволокой [2]. Способ
высокоскоростной электрошлаковой сварки плавящимся мундштуком в узкий зазор
предназначен для сварки низколегированной стали, эксплуатируемой при низких
температурах. Легирование сварного шва осуществляется через трубчатую
электродную проволоку, заполненную флюсом основного типа, в который введены
модификаторы. Рассмотренные способы приводят к повышению хладностойкости
металла шва, однако, существенно не влияют на свойства участка перегрева зоны
термического влияния сварных соединений.
Большинство из известных
технологических приемов базируется на регулировании теплового режима в зоне
сварки величиной погонной энергии. Например, известен способ электрошлаковой
сварки, при котором перед подачей электрода в шлаковую ванну осуществляют его
предварительный подогрев за счет увеличения вылета или током от независимого
источника [1]. На этом же принципе основан способ электрошлаковой сварки с
одновременным оплавлением кромок основного металла при помощи дополнительного
электрода, вводимого в шлаковую ванну [14]. Для увеличения производительности
сварки при одновременном уменьшении перегрева металла околошовной зоны
предложен способ электрошлаковой сварки с присадкой дополнительного материала в
виде обесточенной проволоки или пластины, помещаемой в сварочный зазор [6].
Этот способ позволяет примерно в полтора раза повысить скорость сварки и
соответственно ограничить погонную энергию. Предложен способ, ограничивающий
тепловложение в процессе электрошлаковой сварки, за счет дополнительной подачи
в шлаковую ванну порошкообразного присадочного металла. Процесс плавления
такого рода металла не сопровождается сильным перегревом, поскольку
теплонасыщение гранул происходит мгновенно. При этом примерно в четыре раза
сокращается время выдержки околошовной зоны выше температуры интенсивного роста
зерна. Снижение степени перегрева металлической ванны, уменьшение ее объема и
времени пребывания в жидком состоянии, увеличение скорости нагрева и охлаждения
способствуют улучшению свойств металла шва.
Широкое распространение как в
нашей стране, так и за рубежом получили способы ограничения тепловложения при
электрошлаковой сварке при помощи уменьшения объема наплавленного металла.
Последнее достигается за счет изменения величины сварочного зазора, сваркой
тонкой проволокой в узкий зазор. Например, уменьшение ширины зазора примерно на
45% приводит к увеличению скорости сварки и снижению тепловложения почти в два
раза. Это способствует уменьшению перегрева металла сварного соединения и
повышению его стойкости против хрупкого разрушения.
Одним из наиболее эффективных
оказалось направление, связанное с внешним воздействием на параметры
термических циклов посредством принудительного охлаждения сварного соединения
[8]. Этот способ электрошлаковой сварки позволяет непосредственно в процессе
сварки обеспечить заданный фазовый состав структуры, а следовательно, и
механические свойства сварных соединений. Это положение подтверждено
исследованиями, показавшими возможность обеспечения необходимого комплекса
эксплуатационных характеристик сварных соединений из термически упрочненных и
нормализованных сталей марок 10Г2ФР, 16ГС, 09Г2С. 20К, 20ЮЧ, 12ХМ толщиной
26-100 мм, выполненных электрошлаковой сваркой с регулированием термических
циклов. Известен положительный опыт сочетания различных методов для
регулирования параметров термических циклов, например, одновременное применение
сопутствующего охлаждения и дополнительной подачи в шлаковую ванну
порошкообразного присадочного металла (ППМ) при сварке стали марок 10Г2ФР,
12ХМ. Сопутствующее охлаждение оказывает существенное влияние на стадию
охлаждения, подача ППМ- на стадию нагрева. При одновременном применении ППМ и
сопутствующего охлаждения их воздействие на термические циклы суммируется и
позволяет наиболее эффективно оптимизировать их параметры.
Рассмотренные способы,
предложенные для снижения структурно-механической неоднородности сварных
соединений и повышения их хладностойкости, свидетельствуют о широкой возможности
применения электрошлаковой сварки при изготовлении сварных конструкций из
толстолистового металла за счет правильного выбора методов регулирования
процесса.
Одним из эффективных способов
повышения технологических и служебных характеристик металла сварных швов
(пластичности, ударной вязкости, жаро- и коррозионной устойчивости,
хладностойкости и пр.) является улучшение структуры путем микролегирования
редкоземельными металлами (РЗМ). Информационный взрыв, касающийся применения
РЗМ в машиностроительной металлургии, произошел в конце 60-х годов 20-го века и
направления его разрабатываются до сих пор. За рубежом наибольший интерес этой
проблеме уделяется в США и Японии. Из известных 17 редкоземельных металлов
применение в металлургической промышленности нашли иттрий и церий. РЗМ (в
частности, церий) могут выступать в роли раскислителей, десульфураторов,
модификаторов, а также микролегировать металл, изменяя его физико-механические
характеристики.
В публикациях, посвященных
применению РЗМ в сварочной технике, основное внимание уделяется исследованиям
по влиянию РЗМ на структуру и свойства наплавленного металла различных
конструкционных материалов, свойства присадочных проволок, стабильность горения
дуги.
Весьма перспективным является
микролегирование РЗМ сварочных материалов, применяемых для изготовления сварных
конструкций, эксплуатируемых в условиях пониженных температур, в которых
требования по пластичности и вязкости металла шва является основным критерием.
Исследовалось влияние РЗМ и их окислов на механико-технологические свойства
наплавленного металла. Металл для исследования наплавляли электродом типа Э-50
с введением в покрытие РЗМ - иттрия и окислов иттрия, церия, диспрозия, эрбия в
количестве 0,2 - 3,0 %. Выявлена экстремальная зависимость влияния иттрия на
ударную вязкость и пластические свойства. Прочностные характеристики не
претерпевают заметного изменения. При введении окислов РЗМ наблюдается
тенденция повышения всей гаммы механических свойств. Однако значение ударной
вязкости и пластичности ниже, чем при обработке наплавленного металла иттрием.
Особенно большой прирост получен по ударной вязкости при испытании на
хладностойкость наплавленного металла, микролегированного иттрием. Основной причиной
повышения хладностойкости низколегированного наплавленного металла,
обработанного иттрием, является рафинирование переплавленного металла, снижение
содержания примесей на границе зерен и придание этим примесям сфероидальной
формы. Кроме того микродобавки приводят к измельчению зерен феррита. Пластины
цементита перлитной составляющей, как установлено при
электронно-микроскопическом исследовании, дробятся, теряют ориентировку,
образуя прерывистые цепочки по границам зерен, края их округляются. При введении
~ 1% иттрия внутри и по границам зерен начинает образовываться новая фаза,
большей частью овальной формы, имеющая светло-розовую окраску на нетравленом
шлифе. Новая фаза обогащена иттрием, что установлено микрорентгеноспектральным
анализом.
Обработка наплавленного
металла иттрием влияет на форму, содержание и размеры неметаллических
включений. Крупные неправильной формы включения располагаются, как правило,
цепочками, диспергируют, приобретают шаровидную форму и равномерно
распределяются по сечению. Количество их уменьшается. Однако введение иттрия
выше оптимального содержания приводит к увеличению количества неметаллических
включений, не меняя их форму и расположение. Повышение содержания иттрия до 3%
приводит к образованию грубых игольчатых структур бейнита и
структурно-свободного феррита, что влечет за собой повышение характеристик
прочности, падение показателей пластичности.
Введение РЗМ как в основной
металл, так и в сварочные материалы существенно влияет на технологические
характеристики и стабильность процесса сварки. Изучено влияние РЗМ, вводимого в
сталь в количестве 0,013; 0,021и 0,03 %, на стабильность горения дуги, внешний
вид шва и разбрызгивание при сварке плавящимся электродом в защитной смеси СО2 - Аr. Установлено, что частота переноса металла в
моменты коротких замыканий и разбрызгивание металла уменьшаются при повышении
концентрации РЗМ в основном металле. При введении РЗМ в электродную проволоку
при сварке в аргоне легированных и низколегированных сталей, на постоянном токе
обратной полярности торец электрода резко заостряется благодаря этому
ограничивается блуждание дуги и устанавливается стабильный режим сварки с
короткими замыканиями даже при относительно высоком напряжении на дуге (частота
250 Гц). На прямой полярности явление заострения проволоки не наблюдается, но
из-за воздействия присадок РЗМ дуга горит стабильно. При сварке на переменном
токе присадки РЗМ позволяют применять источники питания с низким напряжением
холостого хода за счет снижения напряжения повторного зажигания дуги. Таким
образом, обработка сварочной ванны оптимальным количеством РЗМ оказывает
благотворное влияние на комплекс механико-технологических свойств
низколегированного наплавленного металла. РЗМ в процессе образования сварного
шва оказывают сложное действие - наряду с рафинированием модифицируют
наплавленный металл, что позволяет считать микролегирование РЗМ существенным
резервом повышения качества сварных соединений.
Изучить: 1. Характеристику низкоуглеродистых и низколегированных
сталей.
2. Особенности
сварки.
группа: 412
Предмет: Техника и технология частично механизированной сварки (наплавка) плавлением в защитном газе.
Тема урока: Выбор материалов для наплавки изношенных деталей.
Наплавка — это процесс сварочного производства, при котором на рабочую поверхность изделия, нагретую до оплавления, наносят расплавленный металл. Таким образом можно получить поверхностный слой на изготовляемых деталях с заданными свойствами (износостойкостью, кислотоупорностью или жаростойкостью) или восстановить слой и размеры изношенного изделия. Наплавкой создаются биметаллические изделия, высокая прочность и долговечность которых сочетаются с низкой стоимостью их изготовления и меньшим расходом дефицитных материалов. При наплавке (большинством способов), так же как и при сварке, образуется подвижная сварочная ванна. В ее головной части основной металл расплавляется и перемешивается с электродным металлом, а в хвостовой — происходят кристаллизация расплава и образование металла шва. Наплавлять можно слои металла как одинаковые по составу, структуре и свойствам с металлом детали, так и значительно отличающиеся от них. Металл наплавки выбирают с учетом его эксплуатационных требований и свариваемости.
Наплавка слоя с заданными свойствами затрудняется из-за перемешивания
наплавляемого металла с металлом самого изделия. Перемешивание и изменение
свойств наплавляемого металла тем больше, чем больше глубина проплавления
металла изделия. Поэтому при наплавке необходимо стремиться получить
минимальную глубину проплавления. Для этого следует использовать источники
теплоты, обеспечивающие равномерный нагрев поверхности металла с минимальной
глубиной проплавления. Обычно используют ацетилено-кислородное пламя,
электрическую дугу, электрошлаковый процесс, а в ряде случаев высокочастотный
нагрев.
Различают ручную, механизированную и автоматическую
наплавку. Две последние являются предпочтительными. Они позволяют
получить более высокие качество и производительность.
Обеспечение заданных свойств наплавленного металла при
механизированной наплавке достигается использованием электродной и наплавочной
проволок, а также специальной порошковой проволоки и порошковых лент. Наплавку
при этом производят под флюсом (плавленым и керамическим) или в среде защитных
газов. Порошковые проволоки, в шихту которых вводят минералы и газообразующие
вещества, обеспечивают выполнение наплавки без дополнительных защитных средств.
Наплавку можно производить на плоские, цилиндрические, конические,
сферические и другие поверхности в один или несколько слоев. Слой наплавки
может изменяться по толщине от долей миллиметра до сантиметров. При наплавке
слоев с заданными свойствами, как правило, химический состав наплавленного
металла значительно отличается от основного металла. В связи с этим при
наплавке необходимо выполнять ряд технологических требований. Основным из них
является минимальное разбавление наплавленного слоя основным металлом,
расплавляемым при наложении валиков. Поэтому при наплавке нужно обеспечить
получение наплавленного слоя с минимальным проплавлением основного металла. В
противном случае увеличивается доля основного металла в формировании
наплавленного слоя, он вызывает ненужное разбавление наплавленного металла
расплавляемым основным. Необходимо также обеспечить минимальную зону
термического влияния и минимальных напряжений и деформаций. Это достигается
путем уменьшения глубины проплавления регулированием параметров режима,
погонной энергии, увеличением вылета электрода, использованием широкой
электродной ленты и другими технологическими приемами. Существуют
различные приемы нанесения наплавленного слоя: ниточными валиками с перекрытием
один другого на 0,3...0,4 их ширины, широкими валиками, полученными за счет
поперечных к направлению оси валика колебаний электрода, электродными лентами и
др.
Расположение
валиков с учетом их перекрытия tn характеризуется
шагом наплавки (рис. 5.62).
Наплавку криволинейных поверхностей тел вращения производят тремя способами (рис. 5.63): по образующей тела вращения, по окружности и по винтовой линии. Наплавку по образующей осуществляют отдельными валиками, как при наплавке плоских поверхностей. Наплавку по окружностям также выполняют отдельными валиками до полного замыкания их начального и конечного
Рис.
5.62. Схема наплавки слоев:
В — ширина валика; hn —
высота наплавки; hnр — глубина проплавления; 5Н —
шаг наплавки
Рис. 5.63.
Наплавка тел вращения: а — по образующей; б —
по окружности; в — по винтовой линии
участков со смещением на определенный шаг вдоль образующей линии. Деталь при
наплавке по винтовой линии вращается непрерывно, а источник нагрева
перемещается вдоль оси заготовки со скоростью, при которой одному ее обороту
соответствует смещение источника, равное шагу наплавки. При наплавке тел
вращения следует учитывать возможность стекания расплавленного металла в
направлении вращения заготовки. В этом случае источник нагрева нужно смещать в
сторону, противоположную направлению вращения, учитывая при этом длину
сварочной ванны и диаметр изделия (рис. 5.64).
Технологические
условия наплавки выбирают исходя из свойств материала наплавляемой заготовки.
Заготовки из низкоуглеродистых и низколегированных сталей обычно наплавляют без
их нагрева. На-
Рис. 5.64.
Смещение электрода при наплавке тел вращения: а — наклонно
расположенный электрод; б — вертикально расположенный
электрод
плавку деталей из средне- и высокоуглеродистых, легированных и
высоколегированных сталей часто выполняют с предварительным нагревом, а также с
последующей термообработкой для снятия внутренних напряжений. Термообработку
(отжиг) часто производят после наплавки для снижения твердости перед
последующей механической обработкой наплавленного слоя. Для наплавки в основном
применяют способы дуговой и электрошлаковой сварки. При выборе рационального
способа и технологии наплавки необходимо учитывать условия эксплуатации
наплавленного слоя и экономическую эффективность процесса.
При дуговой
наплавке под флюсом, так же как при сварке, нагрев и расплавление металла
производятся теплом дуги, которая горит между плавящимся электродом и основным
металлом под слоем флюса. Это один из основных видов механизированной и
автоматической наплавки. К его преимуществам можно отнести непрерывность и
высокую производительность, малые потери электродного металла, отсутствие
открытого излучения дуги. Наплавка под флюсом обеспечивает хороший внешний вид
наплавленного слоя (гладкая поверхность и плавный переход от одного
наплавленного валика к другому). В процессе наплавки легирование наплавленного
металла может осуществляться четырьмя основными способами (рис. 5.65).
1.
Использование легированной проволоки или ленты и обычных плавленых флюсов. При
этом применяют легированные сварочные проволоки и специальные наплавочные
проволоки и легированные ленты, в том числе спеченные. Наплавку осуществляют
под флюсами
Рис. 5.65.
Способы легирования наплавляемого металла: а — при помощи
сварочной проволоки; б — с использованием порошковой
проволоки; в — с применением керамического флюса; г — посредством
укладки
легированной
усадки
- (АН-20, АН-26 и др.), которые
выбирают в зависимости от состава электродного металла.
- 2. Применение порошковой проволоки
или порошковой ленты и обычных плавленых флюсов. Порошковая проволока или
лента расплавляется в дуге и образует однородный жидкий расплав. Эго дает
возможность получить наплавленный металл с общим содержанием легирующих
примесей до 40...50 %.
- 3. Применение обычной
низкоуглеродистой проволоки или ленты и легирующих флюсов (керамических).
Этот способ позволяет вводить в наплавленный металл до 35 % легирующих
элементов. При наплавке наиболее часто используют керамические флюсы
АНК-18 и АПК-19. Они обеспечивают хорошее формирование наплавленного
металла, легкую отделимость шлаковой корки, высокую стойкость
наплавленного металла против образования пор и трещин.
- 4. Использование обычной
низкоуглеродистой проволоки или ленты и обычных плавленых флюсов с предварительной
укладкой легирующих материалов на поверхность наплавляемого изделия. При
этом возможны предварительная засыпка или дозированная подача легирующих
порошков, предварительная укладка прутков или полосок легированной стали,
а также намазывание специальных паст на место наплавки и т.д. Во всех
случаях нанесенный легирующий материал расплавляется дугой и переходит в
наплавленный металл.
Между
сваркой и наплавкой много общего. Поэтому при наплавке используют то же
оборудование, что и при сварке соответствующими способами.
Для
предупреждения образования шлаковых включений и непроваров в наплавленном слое
при многослойной наплавке следует тщательно удалять шлаковую корку с предыдущих
слоев.
К дуговой
наплавке в защитных газах прибегают в тех случаях, когда невозможны
или затруднены подача флюса и удаление шлаковой корки. Преимуществами этого
вида наплавки являются возможность визуального наблюдения за процессом,
возможность механизации и автоматизации с применением серийного сварочного
оборудования (при наплавке заготовок в различных пространственных положениях,
глубоких отверстий, внутренних поверхностей, мелких заготовок и т.п.).
Наплавка в защитных
газах во многом аналогична наплавке под флюсом, отличие заключается лишь в том,
что вместо флюсовой осуществляется газовая защита зоны наплавки. Это
освобождает сварщика от необходимости засыпки флюса и удаления шлака. Для
уменьшения разбрызгивания металла наплавку в защитном газе следует выполнять
самой короткой дугой. Во избежание коробления заготовок наплавку плоских
поверхностей коробчатых заготовок нужно производить отдельными участками
«вразброс». Заготовки цилиндрической формы наплавляют по винтовой линии как
непрерывным валиком, так и с поперечными колебаниями электрода. Короткие
участки можно наплавлять продольными валиками вдоль оси заготовки. Однако при
этом могут возникнуть деформации, которые требуется уравновешивать. Для этого
наплавку каждого последующего валика необходимо выполнять с противоположной
стороны по отношению к уже наплавленному. При наплавке внутренних
цилиндрических и конических поверхностей следует использовать специальные
удлиненные мундштуки.
Наплавку
можно выполнять в среде углекислого газа (углеродистые и легированные стали),
аргона и гелия (высоколегированные стали, а также сплавы на основе алюминия и
магния) и азота (медь и некоторые ее сплавы, поскольку азот ведет себя по
отношению к ним нейтрально). При этом можно применять как плавящийся, так и
неплавящийся электрод. Неплавящийся вольфрамовый электрод обычно используют для
наплавки в среде аргона и гелия. Наиболее часто наплавку выполняют в углекислом
газе плавящимся электродом на постоянном токе обратной полярности. Углекислый
газ окисляет расплавленный металл. Поэтому в наплавочную проволоку обязательно
добавляют раскислители (марганец, кремний и др.). Наплавку производят как
проволокой сплошного сечения, так и порошковой. Для наплавки заготовок из
углеродистых и низколегированных сталей с целью восстановления их размеров
используют сварочные проволоки сплошного сечения Св-08ГС, СВ-08Г2С, CB-12FC, а
также наплавочные Нп-40, Нп-50, Нп-ЗОХГСА и др. Для получения наплавленного
слоя с особыми свойствами применяют порошковые проволоки.
Недостатком
описанного способа является то, что при наплавке в среде углекислого газа
жидкий металл сильно разбрызгивается. Это приводит к налипанию брызг на
мундштук и засорению сопла горелки. Помимо этого возможность сдувания газовой
струи ветром осложняет наплавку на открытом воздухе.
Дуговая
наплавка порошковыми проволоками с внутренней защитой основана на введении в
сердечник проволоки кроме легирующих компонентов шлакообразующих и
газообразующих материалов. Флюсовая и газовая защита при наплавке такой
проволокой не нужна. Легирующие элементы порошковой проволоки переходят в шов,
а газо- и шлакообразующие материалы обеспечивают нужную защиту металла от азота
и кислорода воздуха. Тонкая пленка расплавленного шлака в зоне дуги покрывает капли
жидкого металла и изолирует последние от воздуха, а разложение газообразующих
материалов приводит к образованию потока защитного газа. На поверхности
наплавленного валика после его затвердевания формируется тонкая шлаковая корка,
которую можно удалять при наплавке последующих слоев. Для наплавки используют
различные самозащитные порошковые проволоки: для создания низкоуглеродистых
слоев — сварочные (типа ПП-ЛНЗ и др.), для получения слоев с особыми свойствами
— специальные.
Технология
выполнения наплавки самозащитной порошковой проволокой аналогична технологии
наплавки в среде углекислого газа. Открытая дуга позволяет точно направлять
электрод, следить за формированием наплавленного слоя. Это имеет большое
значение при наплавке заготовок, имеющих сложную форму. Данный способ не
требует сложной аппаратуры по сравнению с наплавкой под флюсом и в среде
защитного газа. Наплавку можно выполнять на открытом воздухе. При этом
увеличивается производительность процесса по сравнению с наплавкой под флюсом и
в защитных газах, снижается себестоимость наплавляемого металла.
Рис.
5.66. Схема плазменной наплавки с вдуванием порошка в дугу
Плазменная
наплавка и напыление заключаются
в том, что нагрев присадочного и основного металлов производится сжатой дугой
или газовой плазмой, выделенной или совпадающей со столбом дуги. Механизм
образования наплавленного слоя аналогичен механизмам других способов дуговой
наплавки.
В качестве
наплавочных материалов также применяют порошки. Схема плазменной наплавки с
вдуванием порошка в дугу показана на рис. 5.66.
Дуга
возбуждается вольфрамовым электродом 1 и внутренним
соплом 2. Плазмообразующий газ, проходя через дугу, создает
плазменную струю 3 косвенного действия. Эта струя расплавляет
присадочный порошок. Другая дуга прямого действия 4, которая
горит между электродом 1 и основным металлом 5, совпадает с
плазменной струей прямого действия, нагревающей поверхность до нужной
температуры и тем самым обеспечивающей сплавление порошка и основного металла.
Изменяя силу тока сжатой дуги прямого действия, проплавление основного металла
можно свести до минимума. Толщину наплавленного слоя можно варьировать в
пределах 0,3... 10,0 мм с разбавлением основным металлом от 3 до 30 %. От
указанных дуг получает теплоту и основной металл. Регулировать долю основного
металла и производительность наплавки можно путем изменения силы тока. В этом
случае наплавляемое изделие в сварочную цепь не включают.
При плазменной
наплавке в качестве защитных газов используют аргон, азот, углекислый газ,
смеси аргона с гелием или азотом и др. В качестве плазмообразующего могут
применяться аргон, гелий, углекислый газ, воздух и г.д. Стабильное протекание
процесса наплавки обеспечивают неплавящиеся электроды из материала,
позволяющего без разрушения выдерживать нагревание до высоких температур.
Применяют электроды из чистого вольфрама или с присадками диоксида тория,
оксидов лантана и иттрия. Этот вид наплавки обеспечивает малую глубину
проплавления основного металла, возможность наплавки тонких слоев, высокое
качество и гладкую поверхность наплавленного металла.
Плазменный
нагрев можно также применять для напыления поверхностных слоев. Но сравнению с
наплавкой оно имеет ряд особенностей. Напыление представляет
собой процесс нанесения па неоплав- ленную поверхность изделия металлических
слоев из частиц материала, нагретых до температуры плавления или близкой к
плавлению. Присадочный материал в виде проволок подается в сжатую дугу и там
нагревается струей газа, а затем с большой скоростью подается на поверхность
изделия. Толщину напыленного слоя можно изменять от сотых до десятых долей
миллиметра. Более толстые слои не напыляют, так как они склонны отслаиваться от
поверхности изделия (откалываться). Напыление можно выполнять как металлами и
сплавами, так и различного вида соединениями: оксидами, карбидами, нитридами и
т.п.
Технологически
в отличие от наплавки напыление производят по способу косвенного нагрева
выделенной дуговой плазмой. Расстояние от сопла горелки до изделия при
проплавке составляет 6...25 мм, а при напылении — 50... 120 мм и более.
Напыленные слои материала имеют меньшую плотность и большую пористость по
сравнению с наплавленными и более склонны к откалыванию от поверхности изделия
при нарушении технологии. Однако в этих слоях практически отсутствует
разбавление основным металлом.
Рис.
5.67. Схема электрошлаковой наплавки на вертикальную поверхность
Сущность
процесса электрошлако - вой наплавки (рис. 5.67) заключается в
том, что в пространстве, которое образовано поверхностью наплавляемого
изделия 1 и формирующим кристаллизатором 4, охлаждаемым
водой, создается ванна расплавленного шлака 3, в которую
подается электродная проволока 5.
Ток, проходя
между электродом и изделием, нагревает шлаковую ванну до температуры выше 2000
°С. В результате этого электродный и основной металлы оплавляются, образуя
металлическую ванну. При затвердевании последней формируется наплавленный
слой 2.
Для
реализации электрошлаковой наплавки различных поверхностей нужно обеспечить
достаточно глубокую ванну, которую проще всего получить при вертикальном или
наклонном расположении деталей. По сравнению с дуговой наплавкой это менее
универсальный способ. Однако он весьма эффективен в случаях, когда на изделие
нужно наплавить слой металла значительной толщины (более 14... 16 мм).
Использование большой силы тока, а также электродов большого сечения
обеспечивает высокую производительность (до 150 кг наплавленного металла в
час).
В качестве
присадочного металла используют наплавочные проволоки (одну или несколько),
электродные ленты, пластины, а также стержни большого сечения, иногда и трубы.
Последние применяют для наплавки цилиндрических поверхностей изделий. Наплавку
обычно осуществляют с флюсами АН-8, АН-22 и т.д.
Вибродуговая
наплавка (рис.
5.68) обычно используется для наплавки заготовок типа тел вращения диаметром от
8 мм и более. Ее сущность заключается в том, что сварочная проволока 3 подается
с постоянной скоростью в направляющий мундштук 5 и периодически соприкасается в
точке А с поверхностью заготовки 1, которая равномерно
вращается. Концу проволоки сообщается колебательное перемещение от
вибратора 4. При наплавке через мундштук 2 непре-
Рис.
5.68. Схема вибродуговой наплавки
рывно
подается струя слабого раствора соды. Она охлаждает заготовку и защищает зону
сварки от контакта с атмосферой.
Нагрев
основного и электродного металла до расплавления осуществляется теплотой,
которая выделяется в результате периодически повторяющихся электрических
разрядов, т.е. прерывисто горящей электрической дуги. Наплавленный слой
образуется при кристаллизации расплавленного основного и электродного металла.
Малая длительность и прерывистость горения электрической дуги обусловливается
вибрациями электродной проволоки, создаваемыми электромагнитными или
механическими вибраторами. При вибрациях возникают короткие замыкания из-за
соприкосновения электродной проволоки и наплавляемого изделия (основного
металла), а во время отрыва проволоки появляется ток большой силы и загорается
электрическая дуга.
При наплавке
осуществляются следующие движения: вращение наплавляемого изделия,
поступательное движение вибродуговой головки вдоль продольной оси наплавляемого
изделия, подача проволоки в зону дуги и вибрация проволоки. Питание
производится от выпрямителей, сварочных генераторов, а также от низковольтных
трансформаторов с вторичным напряжением 12...16 В и более. Высокие показатели
достигаются при наплавке на постоянном токе обратной полярности. В сварочную
цепь обычно включают индуктивность, значение которой выбирают в зависимости от
частоты вибрации электродной проволоки, напряжения, рода тока и других
факторов. Для наплавки используют сварочные проволоки диаметром 0,8...2,0 мм.
Для защиты расплавленного металла от взаимодействия с окружающей средой наплавку
выполняют в струях жидкостей или защитных газов, а также под слоем флюса.
Применяются водные растворы кальцинированной соды; смеси кальцинированной соды,
мыла и глицерина; эмульсии глицерина.
Для ручной
дуговой наплавки па углеродистую сталь применяют электроды Э42...Э100.
Наилучших результатов достигают при использовании фтористо-кальциевых покрытий
УОНИ-13/50, У-340/50 и других покрытий этого типа. Наплавка такими электродами
дает достаточную плотность и мелкозернистость наплавленного слоя. Хорошие результаты
обеспечивают электроды ОЗС-4 и МР-3 типа Э-46 и электроды АНО-1, АНО-2, АНО-3
типа Э-42. Ими можно производить наплавку на переменном и постоянном токах.
Для
получения наплавленного слоя, например, с износостойкими свойствами необходимо
использовать специальные электроды. Режимы наплавки обычно указывают в паспорте
для каждой марки электрода. Вибродуговую наплавку часто используют для
восстановления изношенных шеек валов машин и механизмов различного служебного
назначения.
Прерывистость
наплавки обеспечивает зону термического влияния небольшой ширины, поэтому
возникающие деформации весьма малы, что особенно важно при наплавке
высокоточных сложных изделий.
При наплавке
в струе жидкости наплавленный металл быстро охлаждается, поэтому он обладает
повышенной твердостью и износостойкостью.
Вибродуговая
наплавка особенно эффективна при нанесении слоев металла малой толщины.
Недостатки этого процесса: сравнительно низкий коэффициент наплавки, низкая
производительность.
Металлизация
напылением — это
процесс нанесения жидкого пылеобразного металла на поверхность изделия. Его
сущность заключается в том, что к источнику нагрева (пламя, дуга, плазменная
струя) подают проволоку, которую нагревают и расплавляют. Образовавшийся жидкий
металл под давлением сжатого воздуха вылетает с большой скоростью из сопла
металлизатора в виде распыленных капель. Капли металла, ударяясь о напыляемую
поверхность, соединяются с нею и образуют слой покрытия.
Металлизация
легко восстанавливает изношенные поверхности деталей машин. Ее используют для
устранения внешних дефектов в отливках как из черных, гак и из цветных
металлов, а также для восстановления изношенных шеек, валов, поршней,
направляющих станин и т.д.
Напыление
осуществляют металлическими материалами в виде проволок (стальные, алюминиевые,
медные и т.д.) и неметаллическими материалами, подготовленными в виде порошков
(стекло, эмаль, пластмассы и т.д.). Металлизация менее эффективна по сравнению
с наплавкой. Металлизационный слой, состоящий из мелких поверхностно окисленных
частичек металла, имеет малую плотность, пониженную пластичность и прочность.
Изучить: 1. Основные виды наплавки.
2. Дуговая
наплавка в среде защитных газов.
3. Наплавка порошковыми проволоками.
группа: 412
Предмет: Техника и технология частично механизированной сварки (наплавка) плавлением в защитном газе.
Тема урока: Наплавочные материалы: порошковые электродные ленты, спеченные электродные ленты, флюсы для наплавки.
Порошковая электродная лента
Для
широкослойной наплавки все большее применение находит порошковая
электродная лента рис 35. , состоящая из двух или одной тонких (0,3-0,5 мм)
стальных (сталь 08кп) лент и засыпанной между ними шихты.
Шихту дляленты получают так же, как и для порошковой проволоки. Изготовляют
порошковую ленту на специальных станках.
Порошковая
лента состоит из оболочки из мягкой холоднокатаной ленты и сердцевины из
смеси порошков графита, ферросплавов, чистых металлов и других
компонентов. Порошковую ленту изготовляют из отдельных секций
шириной 12-14 мм на специальном станке, азатем собирают в широкую ленту.
Широкое
применение в промышленности находят порошковые ленты ИЭС им. Е.О. Патона. Ленты
выпускаются шириной 30-60мм и толщиной 1,5-3,0 мм. Широкая порошковая лента,
состоящая из одной секции, не всегда обеспечивает необходимую
однородность наплавленного металла, так как при ее изготовлении трудно
обеспечивать равномерное распределение материалов шихты по всему сечению ленты.
Поэтому для наплавки преимущественно применяют ленту небольшой ширины (до 30
мм).
Наиболее
часто используют порошковые ленты ПЛ-У30Х30Г3ТЮ, ПЛ-АН101
(ПЛ-У300Х25Н3С3), ПЛ-АН102 (ПЛ-30Х25Н4С4) и др.
Ленту марки ПЛ-У30Х30Г3ТЮ применяют для износостойких наплавок режущих
органов землеройных машин, деталей строительных машин.
Механизированная
наплавка пояса конуса и чаш засыпных аппаратов производится лентой
ПЛ-У300Х25Н3С3-11, ПЛ-30Х25Н4С4. Этой лентой наплавляют режущие кромки
грейферов, лопастей бетоносмесительных машин, катков тракторов, зубьев и ковшей
погрузчиков и др.
Важным
преимуществом этих порошковых лент является возможность их использования
без применения флюсов или защитных газов. Это достигнуто за счет
введения в ленту кроме легирующих элементов веществ, обеспечивающих
хорошее раскисление сварочной ванны и связывание азота воздуха в стойкие
нитриды. При наплавке лентой ПЛ-АН101 достигается минимальное
разбрызгивание электродного металла и высокая однородность
химического состава наплавленного металла.
Концентрация
вредных выделений при наплавке лентой ПЛ-АН101 ниже, чем при наплавке другими
порошковыми лентами.
Спеченные электродные ленты
Ленты изготавливают холодной прокаткой смеси порошков с
последующим спеканием в водороде. Спеченную ленту производят толщиной 0,8—1,2
мм и шириной 25—100 мм. Плотность готовой ленты не ниже 6 г/см3,
предел прочности не менее 60 МПа. Преимуществом спеченной ленты является
повышенная производительность наплавки (на 25—30 % по сравнению с
холоднокатаной лентой идентичного химического состава). Плотность тока при
наплавке спеченной лентой составляет 10— 30 А/мм2, напряжение 25—27
В. По ГОСТ 22366—77 предусматривается изготовление спеченных лент 7 марок,
однако из них нашли широкое применение следующие: ЛС—70Х3МН; ЛС—12Х14М3;
ЛС—50Х4В3ФС; ЛС—У10Х7ГР1. Ленты поставляются в рулонах. В рулоне должен быть
один отрезок ленты длиной не менее 40 м. Масса рулона не должна превышать 100
кг.
Таблица. Электродные ленты спеченные по
ГОСТ 22366-93
Марка ленты
Тип наплавленного металла
Марка флюса
Условия работы наплавляемых деталей, свойства
наплавленного металла
ЛС-5Х4В3ФС
50Х4В3ФСГ
АН-60
Термическая
усталость, большие нагрузки и умеренное абразивное изнашивание (валки горячей
прокатки, ножи резки горячего металла, штампы горячей штамповки) HRC 38…44
ЛС-5ХВ2М2ФС
50Х4В2М1Г
АН-60
То же. HRC
45…48
ЛС-70Х3НМ(А)
ЛС-70Х3НМ(Б)
70Х3ГСНМ
АН-60
АН20П
АН26П
Интенсивное
абразивное изнашивание и умеренные нагрузки при нормальных и повышенных
температурах до 300°С. А — для однослойной,
Б — для многослойной наплавки (ходовая часть
грузовых автомобилей и тракторов, подрессорных опор, детали автосцепки
вагонов, ролики рольгангов, опорные катки). HRC 52…58
ЛС-У10Х7ГР1
100Х7ГР
АН-60
Интенсивное
абразивное изнашивание с умеренными ударами (колеса и катки гусеничных машин,
ножи бульдозеров и грейдеров). HRC 56…58
ЛС-1Х14Н3
12X14Н3
АН20П
АН26П
Абразивное
изнашивание и коррозия при нормальных и повышенных температурах до 450° (плунжеры
гидропрессов, судовые валы).
HRC 47…49
ЛС-20Х10Г10Т
20Х10Г10Т
АН20П
АН26П
Трение и
коррозия (плунжеры гидропрессов, крановые колеса, детали автосцепных
устройств) НВ 220…240, после наклепа НВ 450…520
ЛС-08Х21Н9Г
6Х21Н9Г
АН26П
Коррозионное
изнашивание (фланцы, патрубки и сосуды энергетической и нефтехимической
аппаратуры), наплавленный металл склонен к МКК
Примечание. 1. Размеры ленты: 30×0,8…1,2, 60×0,8…1,2; 80×0,8…1,2
мм.
Флюсы классифицируют по следующим
основным признакам.
1. Назначению:
флюсы общего назначения применяют
для сварки и наплавки углеродистых и низколегированных сталей; флюсы
специального назначения применяют для специальных способов сварки, таких как
электрошлаковая сварка, сварка легированных сталей и т. д.
2. Способу изготовления:
плавленые, т. е. получаемые
сплавлением шихты в электрических или пламенных печах, и неплавленые — т. е.
изготовленные без расплавления шихты. К неплавленым относятся флюсы,
изготовленные измельчением и смешиванием отдельных компонентов, а также
керамические флюсы, которые получают смешиванием порошкообразных
шлакообразующих, легирующих, раскисляющих и других компонентов.
3. Химическому составу:
оксидные флюсы, состоящие из окислов металлов и фтористых
соединений, применяемые для сварки и наплавки углеродистых и низколегированных
сталей; солевые флюсы, состоящие из фтористых и хлористых солей, применяемые
для сварки активных металлов; солеоксидные флюсы, применяемые при сварке и
наплавке высоколегированных сталей.
4. Химическому составу
шлакообразующей части:
кислые флюсы, содержащие кислые
окислы SiO2 и TiO2; нейтральные флюсы, содержащие в
основном фториды и хлориды; основные флюсы, содержащие окислы основного характера,
такие как СаО, МgО и FеО.
Плавленые флюсы различают по
строению частиц: стекловидные, пемзовидные и кристаллические флюсы.
По размеру частиц (зерен) флюсы
делятся на: тонкозернистые(с зерном доО,8мм);мелкозернистые(0,1 — 1,6 мм);
среднезернистые{0,25 — 3,0 мм) и крупнозернистые (0,35 — 5,0мм).
Плавленые флюсы, в сравнении с
керамическими, обладают более высокими технологическими свойствами (лучшая
защита от воздуха, формирование наплавляемого сплава, отделимость шлаковой
корки). Кроме того, плавленые флюсы более дешевые. Однако керамические флюсы
позволяют в более широких пределах легировать наплавленный металл посредством
элементов, входящих в флюс. Для механизированной наплавки наиболее широко
используются плавленые флюсы.
Плавленые флюсы различают по
содержанию в них окислов различных элементов. По количеству окиси кремния флюсы
разделяются на: высококремнистые (38 — 44% SiO2); низкокремнистые (до 0,5 SiO2); бескремнистые. По содержанию
окиси марганца на: высокомарганцевые (более 30 % MnО); среднемарганцевые (15 —
30 % МnО); низкомарганцевые (менее 0,5 % МnО).
Высококремнистые плавленые флюсы
предназначены в основном для сварки и наплавки деталей из углеродистых и
низколегированных сталей (табл. 7.4). Наиболее широко в ремонтном производстве
для восстановления деталей наплавкой используют высококремнистые марганцовистые
флюсы ОСЦ-45, ОСЦ-45М, АН-348А и АН-348АМ.
Чтобы уменьшить окисление металла в
результате его реакций с флюсом, для сварки легированных сталей используют
флюсы с ограниченной концентрацией окиси кремния и окиси марганца. Состав
некоторых таких флюсов приведен в табл. 7.5.
Рассмотренные плавленые флюсы
являются системами, состоящими из неметаллических составляющих, окисных и
галогенных соединений. Легирование наплавленного металла в этих случаях может
иметь место только в результате диссоциации соединений, входящих в состав
флюса, или в результате обменных реакций, которые сопровождаются либо повышением
в металле концентрации кислорода, либо потерей им других полезных легирующих
составляющих. Поэтому вводить таким способом большое количество легирующих
элементов в наплавленный металл через флюс затруднительно, и оно ограничивается,
как правило, десятыми долями процента.
Более эффективным способом легирования
через флюсы является введение в их состав свободных металлических
составляющих. В этих случаях флюс представляет собой смесь металлических и
неметаллических составляющих. Такие флюсы называют керамическими. Составы
керамических флюсов могут быть весьма разнообразными, включающими различные
окислы, карбонаты, галогениды,
металлические порошки, различные
сложные соединения и связующие. В качестве основного вида связующего обычно
используют жидкое стекло.
Имея неоспоримое преимущество в виде
возможности широкого диапазона легирования наплавленного сплава, керамические
флюсы имеют и серьезные недостатки. Осуществляемое ими легирование связано с
количеством флюса, переводимого в жидкую фазу, а оно в сильной степени зависит
от сварочного режима и однородности химического состава флюса. Это приводит к
значительной неоднородности наплавленного металла по химическому составу.
Кроме того, к недостаткам керамических флюсов следует отнести .низкую механическую
прочность и большую гигроскопичность.
Однако, несмотря на отмеченные
недостатки, керамические флюсы достаточно широко используются для
восстановления деталей наплавкой. Чаще применяют флюсы АНК.-18 и АНК.-19-
Например, химический состав металла, наплавленного недорогой
низкоуглеродистой электродной проволокой СЬ-08 под слоем флюса АНК-19 содержит:
0,49 % С; 0,66% Мn; 0,34% Si; 3,15 %Сr. При этом твердость наплавленного
металла лежит в пределах ИКС 45 — 49.
Изучить: 1. Порошковая
электродная лента.
2. Спеченные электродные ленты.
3. Классификация флюсов.
08.02.2022
группа: 412
Предмет: Техника и технология ручной дуговой сварки (наплавка, резка) неплавящимися электродами в защитном газе.
Тема урока: Технология сварки высоколегированных (нержавеющих) и жаропрочных сталей и сплавов.
Сварка нержавейки, при которой пользуются аргоном
как защитным газом, является одной из самых распространенных технологий
получения качественных и надежных соединений деталей, изготовленных из такой
стали.
Нержавеющая сталь является металлом, который успешно
противостоит коррозионным процессам. Таким его делают легирующие добавки,
основной из которых является хром (в отдельных марках нержавейки он
может составлять до 20%). В различные виды такой стали могут также добавляться
в качестве легирующих элементов титан, никель, молибден и др. Эти добавки,
кроме антикоррозионных свойств, наделяют нержавейку и рядом других необходимых
физико-механических характеристик.
Нержавеющая сталь, кроме исключительных антикоррозионных
свойств, обладает поверхностью привлекательного внешнего вида. Именно поэтому
ее часто даже не покрывают краской. Отсюда возникают дополнительные требования
к качеству сварного шва: он должен быть не только надежным, но и аккуратным.
Выполнять
сварочные работы с нержавейкой и получать соединения, удовлетворяющие самым
строгим требованиям, может только специалист, обладающий не только необходимыми
знаниями технологии, но и достаточным опытом работы в данной области. Это
значит, что для обучения приемам сварки нержавеющей стали в среде аргона
недостаточно просто посмотреть видео такого процесса – необходимо еще получить
практические уроки.
В чем
заключаются сложности сварки нержавеющей стали
Сложность
сварки нержавейки объясняется свойствами данного металла, которые ему придают
легирующие добавки. По сравнению с низкоуглеродистой сталью, нержавейка имеет
более низкую теплопроводность (в два раза ниже), что является негативным
фактором для сварочных работ. Высокая температура из-за низкой теплопроводности
металла будет концентрироваться в месте выполнения соединения и недостаточно
активно отводиться от него. Это может стать причиной перегрева области
соединения и даже прожога металла. Именно поэтому технология сварки нержавейки
предусматривает снижение сварочного тока: его значение выбирается на 20% ниже,
чем при сварке обычных сталей.
Еще одной характеристикой нержавеющей стали,
которую обязательно следует учитывать при сварке, является повышенный
коэффициент линейного расширения и, как следствие, значительная линейная
усадка. Именно это свойство нержавейки приводит к тому, что детали из нее при
выполнении сварочных работ подвергаются значительным деформациям, нередко
приводящим к появлению трещин на их поверхности. Учитывая это, между
соединяемыми заготовками следует оставлять больший зазор, который будет
компенсировать деформационные процессы.
Нержавейка отличается повышенным электрическим
сопротивлением, что очень негативно сказывается на сварке, если она выполняется
электродом из высоколегированной стали. Такой электрод, который также имеет
большое электрическое сопротивление, начинает сильно нагреваться. Это приводит
к ухудшению качества формируемого сварного шва. Если вы соберетесь варить нержавейку такими электродами, следует
использовать изделия минимальной длины.
Объясняется это следующим. При значительном
нагреве (свыше 500 градусов) на границах кристаллических зерен металла начинают
образовываться карбид хрома и железа. Так появляются очаги возникновения и
дальнейшего распространения коррозии. Чтобы избежать этого негативного явления,
которое носит название межкристаллитной коррозии, необходимо очень быстро
охлаждать детали из нержавейки сразу после окончания сварочных работ. Однако
указанный метод эффективен лишь в том случае, если вы варите нержавеющую сталь
хромоникелевой группы.
Ленты изготавливают холодной прокаткой смеси порошков с
последующим спеканием в водороде. Спеченную ленту производят толщиной 0,8—1,2
мм и шириной 25—100 мм. Плотность готовой ленты не ниже 6 г/см3,
предел прочности не менее 60 МПа. Преимуществом спеченной ленты является
повышенная производительность наплавки (на 25—30 % по сравнению с
холоднокатаной лентой идентичного химического состава). Плотность тока при
наплавке спеченной лентой составляет 10— 30 А/мм2, напряжение 25—27
В. По ГОСТ 22366—77 предусматривается изготовление спеченных лент 7 марок,
однако из них нашли широкое применение следующие: ЛС—70Х3МН; ЛС—12Х14М3;
ЛС—50Х4В3ФС; ЛС—У10Х7ГР1. Ленты поставляются в рулонах. В рулоне должен быть
один отрезок ленты длиной не менее 40 м. Масса рулона не должна превышать 100
кг.
Таблица. Электродные ленты спеченные по
ГОСТ 22366-93
Марка ленты |
Тип наплавленного металла |
Марка флюса |
Условия работы наплавляемых деталей, свойства
наплавленного металла |
ЛС-5Х4В3ФС |
50Х4В3ФСГ |
АН-60 |
Термическая
усталость, большие нагрузки и умеренное абразивное изнашивание (валки горячей
прокатки, ножи резки горячего металла, штампы горячей штамповки) HRC 38…44 |
ЛС-5ХВ2М2ФС |
50Х4В2М1Г |
АН-60 |
То же. HRC
45…48 |
ЛС-70Х3НМ(А) ЛС-70Х3НМ(Б) |
70Х3ГСНМ |
АН-60 АН20П АН26П |
Интенсивное
абразивное изнашивание и умеренные нагрузки при нормальных и повышенных
температурах до 300°С. А — для однослойной, Б — для многослойной наплавки (ходовая часть
грузовых автомобилей и тракторов, подрессорных опор, детали автосцепки
вагонов, ролики рольгангов, опорные катки). HRC 52…58 |
ЛС-У10Х7ГР1 |
100Х7ГР |
АН-60 |
Интенсивное
абразивное изнашивание с умеренными ударами (колеса и катки гусеничных машин,
ножи бульдозеров и грейдеров). HRC 56…58 |
ЛС-1Х14Н3 |
12X14Н3 |
АН20П АН26П |
Абразивное
изнашивание и коррозия при нормальных и повышенных температурах до 450° (плунжеры
гидропрессов, судовые валы). HRC 47…49 |
ЛС-20Х10Г10Т |
20Х10Г10Т |
АН20П АН26П |
Трение и
коррозия (плунжеры гидропрессов, крановые колеса, детали автосцепных
устройств) НВ 220…240, после наклепа НВ 450…520 |
ЛС-08Х21Н9Г |
6Х21Н9Г |
АН26П |
Коррозионное
изнашивание (фланцы, патрубки и сосуды энергетической и нефтехимической
аппаратуры), наплавленный металл склонен к МКК |
Примечание. 1. Размеры ленты: 30×0,8…1,2, 60×0,8…1,2; 80×0,8…1,2
мм.
Флюсы классифицируют по следующим
основным признакам.
1. Назначению:
флюсы общего назначения применяют
для сварки и наплавки углеродистых и низколегированных сталей; флюсы
специального назначения применяют для специальных способов сварки, таких как
электрошлаковая сварка, сварка легированных сталей и т. д.
2. Способу изготовления:
плавленые, т. е. получаемые
сплавлением шихты в электрических или пламенных печах, и неплавленые — т. е.
изготовленные без расплавления шихты. К неплавленым относятся флюсы,
изготовленные измельчением и смешиванием отдельных компонентов, а также
керамические флюсы, которые получают смешиванием порошкообразных
шлакообразующих, легирующих, раскисляющих и других компонентов.
3. Химическому составу:
оксидные флюсы, состоящие из окислов металлов и фтористых
соединений, применяемые для сварки и наплавки углеродистых и низколегированных
сталей; солевые флюсы, состоящие из фтористых и хлористых солей, применяемые
для сварки активных металлов; солеоксидные флюсы, применяемые при сварке и
наплавке высоколегированных сталей.
4. Химическому составу
шлакообразующей части:
кислые флюсы, содержащие кислые окислы SiO2 и TiO2; нейтральные флюсы, содержащие в основном фториды и хлориды; основные флюсы, содержащие окислы основного характера, такие как СаО, МgО и FеО.
Плавленые флюсы различают по
строению частиц: стекловидные, пемзовидные и кристаллические флюсы.
По размеру частиц (зерен) флюсы
делятся на: тонкозернистые(с зерном доО,8мм);мелкозернистые(0,1 — 1,6 мм);
среднезернистые{0,25 — 3,0 мм) и крупнозернистые (0,35 — 5,0мм).
Плавленые флюсы, в сравнении с
керамическими, обладают более высокими технологическими свойствами (лучшая
защита от воздуха, формирование наплавляемого сплава, отделимость шлаковой
корки). Кроме того, плавленые флюсы более дешевые. Однако керамические флюсы
позволяют в более широких пределах легировать наплавленный металл посредством
элементов, входящих в флюс. Для механизированной наплавки наиболее широко
используются плавленые флюсы.
Плавленые флюсы различают по
содержанию в них окислов различных элементов. По количеству окиси кремния флюсы
разделяются на: высококремнистые (38 — 44% SiO2); низкокремнистые (до 0,5 SiO2); бескремнистые. По содержанию
окиси марганца на: высокомарганцевые (более 30 % MnО); среднемарганцевые (15 —
30 % МnО); низкомарганцевые (менее 0,5 % МnО).
Высококремнистые плавленые флюсы
предназначены в основном для сварки и наплавки деталей из углеродистых и
низколегированных сталей (табл. 7.4). Наиболее широко в ремонтном производстве
для восстановления деталей наплавкой используют высококремнистые марганцовистые
флюсы ОСЦ-45, ОСЦ-45М, АН-348А и АН-348АМ.
Чтобы уменьшить окисление металла в
результате его реакций с флюсом, для сварки легированных сталей используют
флюсы с ограниченной концентрацией окиси кремния и окиси марганца. Состав
некоторых таких флюсов приведен в табл. 7.5.
Рассмотренные плавленые флюсы
являются системами, состоящими из неметаллических составляющих, окисных и
галогенных соединений. Легирование наплавленного металла в этих случаях может
иметь место только в результате диссоциации соединений, входящих в состав
флюса, или в результате обменных реакций, которые сопровождаются либо повышением
в металле концентрации кислорода, либо потерей им других полезных легирующих
составляющих. Поэтому вводить таким способом большое количество легирующих
элементов в наплавленный металл через флюс затруднительно, и оно ограничивается,
как правило, десятыми долями процента.
Более эффективным способом легирования
через флюсы является введение в их состав свободных металлических
составляющих. В этих случаях флюс представляет собой смесь металлических и
неметаллических составляющих. Такие флюсы называют керамическими. Составы
керамических флюсов могут быть весьма разнообразными, включающими различные
окислы, карбонаты, галогениды,
металлические порошки, различные
сложные соединения и связующие. В качестве основного вида связующего обычно
используют жидкое стекло.
Имея неоспоримое преимущество в виде
возможности широкого диапазона легирования наплавленного сплава, керамические
флюсы имеют и серьезные недостатки. Осуществляемое ими легирование связано с
количеством флюса, переводимого в жидкую фазу, а оно в сильной степени зависит
от сварочного режима и однородности химического состава флюса. Это приводит к
значительной неоднородности наплавленного металла по химическому составу.
Кроме того, к недостаткам керамических флюсов следует отнести .низкую механическую
прочность и большую гигроскопичность.
Однако, несмотря на отмеченные недостатки, керамические флюсы достаточно широко используются для восстановления деталей наплавкой. Чаще применяют флюсы АНК.-18 и АНК.-19- Например, химический состав металла, наплавленного недорогой низкоуглеродистой электродной проволокой СЬ-08 под слоем флюса АНК-19 содержит: 0,49 % С; 0,66% Мn; 0,34% Si; 3,15 %Сr. При этом твердость наплавленного металла лежит в пределах ИКС 45 — 49.
Изучить: 1. Порошковая
электродная лента.
2. Спеченные электродные ленты.
3. Классификация флюсов.
группа: 412
Предмет: Техника и технология ручной дуговой сварки (наплавка, резка) неплавящимися электродами в защитном газе.
Тема урока: Технология сварки высоколегированных (нержавеющих) и жаропрочных сталей и сплавов.
Сварка нержавейки, при которой пользуются аргоном
как защитным газом, является одной из самых распространенных технологий
получения качественных и надежных соединений деталей, изготовленных из такой
стали.
Нержавеющая сталь является металлом, который успешно
противостоит коррозионным процессам. Таким его делают легирующие добавки,
основной из которых является хром (в отдельных марках нержавейки он
может составлять до 20%). В различные виды такой стали могут также добавляться
в качестве легирующих элементов титан, никель, молибден и др. Эти добавки,
кроме антикоррозионных свойств, наделяют нержавейку и рядом других необходимых
физико-механических характеристик.
Нержавеющая сталь, кроме исключительных антикоррозионных
свойств, обладает поверхностью привлекательного внешнего вида. Именно поэтому
ее часто даже не покрывают краской. Отсюда возникают дополнительные требования
к качеству сварного шва: он должен быть не только надежным, но и аккуратным.
Выполнять
сварочные работы с нержавейкой и получать соединения, удовлетворяющие самым
строгим требованиям, может только специалист, обладающий не только необходимыми
знаниями технологии, но и достаточным опытом работы в данной области. Это
значит, что для обучения приемам сварки нержавеющей стали в среде аргона
недостаточно просто посмотреть видео такого процесса – необходимо еще получить
практические уроки.
В чем
заключаются сложности сварки нержавеющей стали
Сложность
сварки нержавейки объясняется свойствами данного металла, которые ему придают
легирующие добавки. По сравнению с низкоуглеродистой сталью, нержавейка имеет
более низкую теплопроводность (в два раза ниже), что является негативным
фактором для сварочных работ. Высокая температура из-за низкой теплопроводности
металла будет концентрироваться в месте выполнения соединения и недостаточно
активно отводиться от него. Это может стать причиной перегрева области
соединения и даже прожога металла. Именно поэтому технология сварки нержавейки
предусматривает снижение сварочного тока: его значение выбирается на 20% ниже,
чем при сварке обычных сталей.
Еще одной характеристикой нержавеющей стали,
которую обязательно следует учитывать при сварке, является повышенный
коэффициент линейного расширения и, как следствие, значительная линейная
усадка. Именно это свойство нержавейки приводит к тому, что детали из нее при
выполнении сварочных работ подвергаются значительным деформациям, нередко
приводящим к появлению трещин на их поверхности. Учитывая это, между
соединяемыми заготовками следует оставлять больший зазор, который будет
компенсировать деформационные процессы.
Нержавейка отличается повышенным электрическим
сопротивлением, что очень негативно сказывается на сварке, если она выполняется
электродом из высоколегированной стали. Такой электрод, который также имеет
большое электрическое сопротивление, начинает сильно нагреваться. Это приводит
к ухудшению качества формируемого сварного шва. Если вы соберетесь варить нержавейку такими электродами, следует
использовать изделия минимальной длины.
Объясняется это следующим. При значительном
нагреве (свыше 500 градусов) на границах кристаллических зерен металла начинают
образовываться карбид хрома и железа. Так появляются очаги возникновения и
дальнейшего распространения коррозии. Чтобы избежать этого негативного явления,
которое носит название межкристаллитной коррозии, необходимо очень быстро
охлаждать детали из нержавейки сразу после окончания сварочных работ. Однако
указанный метод эффективен лишь в том случае, если вы варите нержавеющую сталь
хромоникелевой группы.
Как
подготовить детали из нержавейки к сварке
Для того чтобы в результате аргонодуговой сварки изделий
из нержавейки получить качественное и надежное соединение, необходимо правильно
подготовить их поверхности. Такая обработка не сильно отличается от подготовки
к сварке в среде аргона деталей из других металлов и
заключается в следующем.
·
Кромки
соединяемых заготовок необходимо зачистить до металлического блеска, для чего
используется металлическая щетка или шлифовальная машинка.
·
После
зачистки кромки деталей обезжириваются при помощи ацетона или авиационного
бензина, что необходимо сделать для обеспечения устойчивости дуги и повышения
качества сварного шва.
·
При
подготовке соединяемых заготовок к сварке следует предусмотреть в них увеличенный
зазор, который будет компенсировать деформационные процессы.
Кроме диаметра присадочной проволоки, надо
обращать внимание и на ее состав. Степень легирования такой проволоки должна
превышать соответствующий показатель у металла, из которого изготовлены
соединяемые заготовки.
Марки
сварочной проволоки для нержавейки
Для того чтобы в результате аргонодуговой сварки изделий
из нержавейки получить качественное и надежное соединение, необходимо правильно
подготовить их поверхности. Такая обработка не сильно отличается от подготовки
к сварке в среде аргона деталей из других металлов и
заключается в следующем.
·
Кромки
соединяемых заготовок необходимо зачистить до металлического блеска, для чего
используется металлическая щетка или шлифовальная машинка.
·
После
зачистки кромки деталей обезжириваются при помощи ацетона или авиационного
бензина, что необходимо сделать для обеспечения устойчивости дуги и повышения
качества сварного шва.
·
При
подготовке соединяемых заготовок к сварке следует предусмотреть в них увеличенный
зазор, который будет компенсировать деформационные процессы.
Кроме диаметра присадочной проволоки, надо
обращать внимание и на ее состав. Степень легирования такой проволоки должна
превышать соответствующий показатель у металла, из которого изготовлены
соединяемые заготовки.
Марки
сварочной проволоки для нержавейки
Аргонодуговая
сварка нержавейки при помощи электрода из вольфрама
Сварка нержавейки в защитной среде аргона используется
преимущественно в тех случаях, когда соединить необходимо детали небольшой
толщины. Данная технология позволяет получать качественные и надежные
соединения с красивыми и аккуратными сварными швами.
В защитной среде аргона чаще всего выполняется сварка
нержавеющих труб, используемых для транспортировки различных жидких и
газообразных сред. Качество сварных швов, получаемых при использовании данной
технологии, позволяет применять ее для соединения деталей трубопроводов,
эксплуатируемых под высоким давлением.
Выполненное
электросваркой в среде аргона соединение труб из нержавеющей стали
Аргонодуговая сварка, выполняемая неплавящимся вольфрамовым электродом, может производиться на переменном
или постоянном токе прямой полярности. Основным рабочим органом при выполнении
такой сварки является горелка, в которой закреплен электрод и из сопла которой
подается струя аргона. Сварной шов формируется за счет присадочной проволоки,
подаваемой вручную в зону горения сварочной дуги. Все движения, совершаемые
горелкой, также выполняются вручную.
В отличие от обычной электродуговой технологии, при
сварке, выполняемой в среде аргона, электродом и присадочной проволокой не
совершают поперечных движений – их перемещают только вдоль оси формируемого
шва.
Делается это для того, чтобы не вывести сварочную ванну из
зоны действия аргоновой защиты (это негативно скажется на качестве соединения).
Необходимо также позаботиться и о защите от окружающего воздуха обратной
стороны шва, которая также обдувается аргоном. Конечно, расход газа от этого
увеличивается, но качество всех участков сварного шва будет высоким.
Положение
горелки при сварке ТИГ
Чтобы не
загрязнить поверхности соединяемых заготовок и не оплавить конец вольфрамового
электрода, им нельзя прикасаться к основному металлу даже в процессе розжига
дуги. Именно поэтому технология сварки в среде аргона с применением
вольфрамового электрода предполагает использование для розжига дуги специальной
пластины, изготовленной из графита или угля. Только после зажигания на такой
пластине сварочную дугу аккуратно переводят на нержавейку. Хорошо демонстрирует
этот процесс, выполнению которого обязательно следует научиться начинающему
специалисту, обучающее видео.
Чтобы
исключить окисление нагретого электрода и только что сформированного шва,
подачу аргона следует отключать не сразу после окончания сварки, а через 10–15
секунд. На расходе газа это скажется незначительно, но этим вы увеличите срок
службы электрода и улучшите качество сварного шва.
Изучить: 1. Сложность сварки
нержавеющей стали.
2. Подготовка
деталей.
3. Процесс сварки нержавеющей стали.
08.02.2022
группа: 412
Предмет: Техника и технология ручной дуговой сварки (наплавка, резка) неплавящимися электродами в защитном газе.
Тема урока: Способы предупреждения и исправления дефектов сварных швов для ручной дуговой сварки (наплавка) неплавящимся электродом в защитном газе.
1. Наиболее
распространены дефекты при сварке цветных металлов.
Металлические включения. В практике наиболее
распространены вольфрамовые включения при сварке цветных металлов. Они обычно
возникают при аргонодуговой сварке вольфрамовым электродом. При этом могут
наблюдаться мгновенная нестабильность дуги и появление одновременно с вольфрамовыми
включениями оксидных включений. Вольфрамовые включения могут располагаться
внутри шва и на поверхности соединений в виде брызг. При попадании вольфрама в
жидкую ванну он обычно погружается на дно ванны. Вольфрам в металле нерастворим
и обладает большой плотностью.
Шлаковые включения. Эти
включения образуются в шве из-зa плохой очистки свариваемых кромок oт окалины и
других загрязнений и, чаще всего, вследствие внутренних подрезов и плохой
зачистки от шлака поверхности первых слоев многослойных швов.
Оксидные пленки могут
возникать при всех видах сварки. Причины иx образования такие жe, как и
шлаковых включений: это загрязненность поверхностей свариваемых элементов;
плохая зачистка от шлака поверхности слоев шва при многослойной сварке; низкое
качество флюса; недостаточная квалификация сварщика и т.д.
2. Две основные группы вольфрамовых включений.
Вольфрамовые включения подразделяют на две основные группы:
изолированные и групповые. Размер диаметра изолированных включений 0,4 ... 3.2
мм. Групповые включения описываются (по рентгенограмме) размером группы,
количеством и размером отдельных (изолированных) включений в группе, при этом
размер группы характеризуется размером минимальной окружности, в которую
вписывается группа включений. Если изображение нескольких включений сливается.
то их принимают за одно включение.
3. Меры, предупреждающие образованию дефектов в швах
конструкций.
Чтобы свариваемые заготовки эффективно плавились под
действием неплавящегося электрода и аргона и не образовывались дефекты в
сварном шве при изготовлении металлических конструкций, необходимо точно
соблюдать некоторые особенности аргонодуговой сварки. Именно так можно добиться
максимального качества конечного результата.
Неплавящийся вольфрамовый стержень должен как можно глубже
проникать в зазор между заготовками. Сварочная дуга должна быть максимально
короткой. Таким способом можно глубже проводить плавку, что отразиться на
размерах сварного шва. Он будет меньше, а качество выше.
Движение электрода должно производиться строго по центру
зазора, и посередине. Отклонения снижают качество шва и его внешний вид.
Присадочная проволока не должна выходить за пределы сварного
участка, и всегда находиться в зоне аргона. Именно таким образом достигается
защита ванны от негативного воздействия кислорода и азота, находящихся в
воздухе. Их воздействие приведет к повышению хрупкости сварного шва. Те же
самые требования и к неплавкому электроду.
Нельзя резко подавать присадку в сварную зону. Это приведет к
большому разбрызгиванию металла и к его перерасходу.
Подача проволоки при ручной сварке должна производиться под
углом. Никаких поперечных отклонений.
Нельзя при окончании сварки обрывать шов отводом электрода из
зоны сваривания. Нужно просто погасить дугу с помощью реостата.
Подавать защитный газ и выключать его после окончания сварки можно только
через (за) 10 секунд. Таким способом защищается еще неостывший плавящийся
металл, который при соприкосновении с воздухом тут же покроется оксидной
пленкой.
Обязательно перед началом сварочных работ производится подготовка
соединяемых металлических заготовок. Это касается и стали, и алюминия, и других
металлов. Нужно стыкуемые плоскости очистить от грязи, ржавчины и других
материалов, используя железную щетку или болгарку с металлической щетковидной
насадкой. Зачищать надо до металлического блеска. Если есть необходимость
(жирные и масляные пятна), то соединяемые поверхности придется обезжирить
растворителем или спиртом.
Обязательно сопоставляются режимы сварки с толщиною стыкуемых заготовок,
учитывая диаметр неплавящегося электрода.
сто погасить дугу с помощью реостата.
4. Способы исправления дефектов.
Чрезмерное усиление шва устраняют с помощью абразивного
инструмента или пневматического зубила.
Непровар, кратеры, пористость и неметаллические включения
устраняют путем вырубки пневматическим зубилом или расчистки абразивным
инструментом всего дефектного участка с последующей заваркой. Часто применяют
выплавку дефектного участка резаком поверхностной кислородной или
воздушно-дуговой резки.
Подрезы заваривают тонкими швами. Наплывы устраняются
обработкой абразивным инструментом или с помощью пневматического зубила.
Наружные трещины устраняются разделкой и последующей
заваркой. Для предупреждения распространения трещины по концам ее сверлят
отверстия. Разделку трещины
выполняют зубилом или резаком. Кромки разделки зачищают от
шлака, брызг металла, окалины и заваривают. Швы с внутренними трещинами
вырубывают и заваривают заново. При наличии сетки трещин дефектный участок
вырезают и взамен сваркой накладывают заплату.
Изучить: 1. Наиболее
распространенные включения.
2. Меры, предупреждающие образованию дефектов в швах
конструкций.
3. Исправление дефектов.
03.02.2022
группа: 412
Предмет: Техника и технология ручной дуговой сварки (наплавка, резка) неплавящимися электродами в защитном газе.
Тема урока: Причины возникновения дефектов сварных швов ручной дуговой сварки (наплавка, резка) неплавящимися электродами в защитном газе.
Дефекты
сварных швов при сварке и наплавке
Напряжения,
существующие после окончания сварки или наплавки до полного остывания детали,
называют остаточными сварочными напряжениями. Они возникают в результате
затруднения расширения и сжатия металла при его нагреве и остывании.
Различают
сварочные напряжения трех родов: линейные или одноосные, действующие только по
одной оси в одном направлении; плоскостные или двухосные; объемные или
трехосные. По направлению действия различают следующие напряжения: продольные и
поперечные, расположенные перпендикулярно к оси сварочного шва. Для низкоуглеродистых
и низколегированных сталей в основном характерны сварочные напряжения первого
рода, которые уравновешиваются внутренними напряжениями восстанавливаемой
детали.
При
разработке технологического процесса восстановления деталей с помощью сварки и
наплавки необходимо обеспечить минимальные значения сварочных напряжений или
предусмотреть их снятие. Если значения сварочных напряжений достигнут предела
текучести металла, то они вызовут его пластическую деформацию, т.е. коробление
детали.
Деформации
бывают временные, существующие только во время проведения сварочных работ, и
остаточные, которые остаются после остывания деталей. В зависимости от формы и
размеров деталей различают деформацию в плоскости, вызывающую уменьшение
размеров конструкции, и угловую деформацию, которая вызывает образование
выпучин, грибовидный изгиб и смещение осей цилиндрических поверхностей.
Значение и характер остаточных напряжений в значительной степени определяются
размерами и свойствами восстанавливаемых деталей, режимами сварки и наплавки,
последовательностью наложения швов и их формой. При растягивающих напряжениях в
наплавленной детали снижается усталостная прочность, повышается коробление, возникает
усадка по длине, а также ухудшается сопротивление детали переменным нагрузкам.
Деформация изгиба увеличивается пропорционально квадрату длины валика.
По
расположению в шве дефекты бывают наружные и внутренние.
К наружным
дефектам относят продольные и поперечные горячие и холодные трещины,
подрезы, кратеры, остатки шлака, неровную поверхность шва, наплывы и др.
Горячие (микро- и
макроскопические) трещины (рис. 13.5, а) образуются
в процессе сварки углеродистых сталей при температуре 1200— 1350°С. На образование
трещин влияют вредные примеси (углерода, кремния, серы, фосфора и водорода) в
металле валика. При наличии в сварочном шве полезных примесей (марганца, никеля
и хрома) уменьшается вероятность появления горячих трещин.
Холодные
трещины (см.
рис. 13.5, бив) возникают при температуре ниже 400°С. Их делят
на закалочные и хрупкие.
Закалочные
трещины образуются на границе сплавления в средне- и высоколегированных сталях
перлитного и мартенситного классов вследствие того, что объем металла
увеличивается и имеют место структурные напряжения. Если неизбежно образование
мартенсита, то сварку и наплавку ведут малым током и с большой скоростью.

Рис.
13.5. Дефекты сварных швов:
7 и 2 —
продольные трещины в шве и околошовной зоне; 3 и 4 — поперечные трещины в шве и
околошовной зоне; 5 — поперечные трещины по толщине свариваемого металла; а —
горячие трещины; бив — холодные трещины; гиб — подрез; ей ж — наплывы; з-л —
непровар; м — поры; н — шлаковые включения
Тогда иглы мартенсита будут маленькими и возникающие напряжения недостаточны
для разрушения металла.
Хрупкие
трещины появляются в наплавленном слое при его быстром охлаждении. Они
распространяются из наплавленного металла в основном с большой скоростью
(1200—1800 м/с). Для их предупреждения нужно предварительно подогревать детали
перед наплавкой, что способствует распаду аустенита, и после медленно
охлаждать.
Появлению
холодных трещин способствует повышенное содержание в металле серы, фосфора,
водорода, кислорода и других вредных примесей.
Подрез (см. рис. 13.5, гид)
характеризуется наличием канавки у края шва. Он получается при сварке током
большой силы или горелкой большой мощности.
Кратеры (незаплавленные углубления),
остатки шлака и неровные поверхности шва образуются в результате работы
сварщика низкой квалификации.
Наплывы (см. рис. 13.5, ей ж) происходят
при слишком быстром плавлении электрода и недостаточном нагреве свариваемого
металла.
К внутренним
дефектам относят непровар корня шва или его кромки, поры, шлаковые
включения, пережог металла шва и др.
Непровар (см. рис. 13.5, з—л) характеризуется
плохим сцеплением или даже отсутствием сцепления наплавленного металла с
основным. Этот дефект получается при недостаточном прогреве свариваемого или
наплавляемого металла, малом угле разделки трещины, малом токе или малой
мощности горелки, а также из-за большой скорости сварки.
Поры (см. рис. 13.5, м) возникают
только на границе раздела фаз твердого и жидкого металла, что объясняется
наличием в нем пузырьков газа СО, С02, Н2 и др. Они
образуются при большой влажности электродов или неправильной регулировке
газовой горелки, плохой очистке свариваемых и наплавляемых поверхностей от
масла, грязи и окалины.
Шлаковые
включения (см.
рис. 13.5, н) образуются при сварке длинной дугой или окислительным
пламенем.
Пережог представляет собой окисленный
крупнозернистый металл шва вследствие применения тока большой силы, медленного
перемещения электрода или горелки. Наружные дефекты швов контролируют визуально
или через лупу с 10—20-кратным увеличением. Для выявления трещин применяют
травление шва 10%-м раствором азотной кислоты.
Внутренние
дефекты обнаруживают ультразвуковым или металлографическим методом,
просвечиванием шва рентгеновскими или гамма-лучами.
Изучить: 1. Изучить причины
возникновения дефектов и напряжений?
2. Наружные дефекты сварных швов.
3. Внутренние дефекты
сварных швов.
03.02.2022
группа: 412
Предмет: Техника и технология ручной дуговой сварки (наплавка, резка) неплавящимися электродами в защитном газе.
Тема урока: Назначение и условия работы контрольно-измерительных приборов, правила эксплуатации и область их применения.
Любые сварочные работы требуют применения
специализированного оборудования. К такому относятся источники питания
(трансформаторы, инверторы, выпрямители), собственно сам сварочный аппарат,
держатель электродов, газовая горелка и прочее.
Отметим, что набор сварочного оборудования для
разных способов сварки будет отличаться. Кроме того, имеет отличия само
сварочное оборудование, и его эксплуатация также может быть различной: одно
допускается для передвижных постов, другое может использоваться только
стационарно и прочее.
Заметим, что сварочное оборудование и его
эксплуатация должны отвечать ряду требований, о которых мы и предлагаем
поговорить дальше.
Разновидности сварочного оборудования.
Отметим, что все оборудование для сварки разделяется
по способу применения – одни аппараты предназначены для бытового использования
непрофессиональными сварщиками, с другими могут работать исключительно
специалисты в области сварки. Главное отличие бытовых и профессиональных
устройств состоит в том, что первые более просты в управлении, а также имеют, в
отличие от профессиональных, меньшие габариты и работают на меньшем напряжении.
Собственно сварочные аппараты также различаются:
одни предназначены для дуговой сварки, другие для проведение газосварочных
работ и пр. Разными они могут быть и по степени
механизации процесса – полуавтоматические, автоматические аппараты.
Все
сварочное оборудование условно подразделяют на два класса, а именно:
Собственно, сварочное оборудование – аппараты и
инструменты, которые используются непосредственно для сваривания металлов. К
этому классу относят – инверторы, держатели электродов, газовые горелки,
различные клапаны и газосмесители, пр.
Защитное оборудование – все инструменты, спецодежда
и устройства, предназначенные для защиты сварщика во время процесса
сварки.
Эксплуатация
и обслуживание сварочного оборудования.
Основные правила эксплуатации любого оборудования
прописываются в инструкциях производителей, сварочные аппараты и инструменты не
исключение. Правилами безопасности четко указывается, что все сварочные работы
должны производиться исключительно по инструкциям и установленным требованиям.
Выполнение правил эксплуатации сварочного
оборудование не только будет способствовать бесперебойной и долгой работе
аппаратов и инструментов, но и создаст безопасные условия для проведения
сварочных работ. А дополнительные защитные средства сварщика обезопасят его от
сопутствующих процессу сварки негативных явлений: разбрызгивания расплавленного
металла, ультрафиолетового излучения и прочего.
Кроме того, жесткие требования предъявляются по
организации рабочего места. Здесь необходимо соблюсти правила пожарной
безопасности, подключения электроустановок, проветривания помещения,
предназначенного для проведения сварочных работ.
При эксплуатации оборудования для электродуговой
сварки подключение выпрямителей или трансформаторов выполняют строго по
инструкции. Обязательно проводится заземление корпусов аппаратов и других
металлических-нетоковедущих частей сварочного оборудования. Заземлению подлежит
и рабочее место специалиста – сварочные станки и столы, плиты и прочее.
Заземление проводится посредством гибких медных
проводков (могут применяться провода из других электропроводящих металлов).
Отметим, что запрещено последовательно включать в заземляющий проводник несколько
установок для сварки.
Следует также соблюдать правила работы с держателями
электродов и горелками. Эти инструменты запрещается направлять на людей. Кроме
того, за их состоянием необходимо постоянно следить и во время производить
очистку и ремонт комплектующих.
Все сварочное оборудование должно содержаться в
сухом помещении. Не следует допускать падений аппаратов и устройств, во
избежание механических повреждений. При регулярной эксплуатации оборудования
каждые шесть месяцев осуществляется очистка, плановая проверка и при
необходимости ремонт. Обязательно
очищать все сварочные аппараты от пыли и грязи, которые скапливаются внутри
устройства.
Ответственность за правильную эксплуатацию
сварочного оборудования несет сварщик. Он обязан работать только в строго
заданных режимах, использовать электросварочные установки по назначению,
следить за их сохранностью, а также соблюдать технику безопасности. Заметим,
что самостоятельно работать на сварочном оборудовании, без присмотра
специалиста, могут только операторы, прошедшие обучение полуавтоматической и
автоматической сварке и инструктаж по правилам безопасности работ.
В противном случае сварочные работы должны
производиться исключительно двумя специалистами – непосредственно сварщиком и
наблюдателем.
Эксплуатация сварочного оборудования с соблюдением
правил и техники безопасности повысит срок службы устройств и снизит риск
возникновения опасных ситуаций.
Изучить: 1. Сварочное оборудование?
2. Инструменты сварщика?
3. Эксплуатация и
обслуживание сварочного оборудования?
03.02.2022
группа: 412
Предмет: Техника и технология частично механизированной сварки (наплавка) плавлением в защитном газе.
Тема урока: Флюсы для сварки плавлением.
Сварка нержавейки в защитной среде аргона используется
преимущественно в тех случаях, когда соединить необходимо детали небольшой
толщины. Данная технология позволяет получать качественные и надежные
соединения с красивыми и аккуратными сварными швами.
В защитной среде аргона чаще всего выполняется сварка
нержавеющих труб, используемых для транспортировки различных жидких и
газообразных сред. Качество сварных швов, получаемых при использовании данной
технологии, позволяет применять ее для соединения деталей трубопроводов,
эксплуатируемых под высоким давлением.
Выполненное
электросваркой в среде аргона соединение труб из нержавеющей стали
Аргонодуговая сварка, выполняемая неплавящимся вольфрамовым электродом, может производиться на переменном
или постоянном токе прямой полярности. Основным рабочим органом при выполнении
такой сварки является горелка, в которой закреплен электрод и из сопла которой
подается струя аргона. Сварной шов формируется за счет присадочной проволоки,
подаваемой вручную в зону горения сварочной дуги. Все движения, совершаемые
горелкой, также выполняются вручную.
В отличие от обычной электродуговой технологии, при
сварке, выполняемой в среде аргона, электродом и присадочной проволокой не
совершают поперечных движений – их перемещают только вдоль оси формируемого
шва.
Делается это для того, чтобы не вывести сварочную ванну из
зоны действия аргоновой защиты (это негативно скажется на качестве соединения).
Необходимо также позаботиться и о защите от окружающего воздуха обратной
стороны шва, которая также обдувается аргоном. Конечно, расход газа от этого
увеличивается, но качество всех участков сварного шва будет высоким.
Положение
горелки при сварке ТИГ
Чтобы не
загрязнить поверхности соединяемых заготовок и не оплавить конец вольфрамового
электрода, им нельзя прикасаться к основному металлу даже в процессе розжига
дуги. Именно поэтому технология сварки в среде аргона с применением
вольфрамового электрода предполагает использование для розжига дуги специальной
пластины, изготовленной из графита или угля. Только после зажигания на такой
пластине сварочную дугу аккуратно переводят на нержавейку. Хорошо демонстрирует
этот процесс, выполнению которого обязательно следует научиться начинающему
специалисту, обучающее видео.
Чтобы
исключить окисление нагретого электрода и только что сформированного шва,
подачу аргона следует отключать не сразу после окончания сварки, а через 10–15
секунд. На расходе газа это скажется незначительно, но этим вы увеличите срок
службы электрода и улучшите качество сварного шва.
Изучить: 1. Сложность сварки
нержавеющей стали.
2. Подготовка
деталей.
3. Процесс сварки нержавеющей стали.
группа: 412
Предмет: Техника и технология ручной дуговой сварки (наплавка, резка) неплавящимися электродами в защитном газе.
Тема урока: Способы предупреждения и исправления дефектов сварных швов для
1. Наиболее
распространены дефекты при сварке цветных металлов.
Металлические включения. В практике наиболее
распространены вольфрамовые включения при сварке цветных металлов. Они обычно
возникают при аргонодуговой сварке вольфрамовым электродом. При этом могут
наблюдаться мгновенная нестабильность дуги и появление одновременно с вольфрамовыми
включениями оксидных включений. Вольфрамовые включения могут располагаться
внутри шва и на поверхности соединений в виде брызг. При попадании вольфрама в
жидкую ванну он обычно погружается на дно ванны. Вольфрам в металле нерастворим
и обладает большой плотностью.
Шлаковые включения. Эти
включения образуются в шве из-зa плохой очистки свариваемых кромок oт окалины и
других загрязнений и, чаще всего, вследствие внутренних подрезов и плохой
зачистки от шлака поверхности первых слоев многослойных швов.
Оксидные пленки могут
возникать при всех видах сварки. Причины иx образования такие жe, как и
шлаковых включений: это загрязненность поверхностей свариваемых элементов;
плохая зачистка от шлака поверхности слоев шва при многослойной сварке; низкое
качество флюса; недостаточная квалификация сварщика и т.д.
2. Две основные группы вольфрамовых включений.
Вольфрамовые включения подразделяют на две основные группы:
изолированные и групповые. Размер диаметра изолированных включений 0,4 ... 3.2
мм. Групповые включения описываются (по рентгенограмме) размером группы,
количеством и размером отдельных (изолированных) включений в группе, при этом
размер группы характеризуется размером минимальной окружности, в которую
вписывается группа включений. Если изображение нескольких включений сливается.
то их принимают за одно включение.
3. Меры, предупреждающие образованию дефектов в швах
конструкций.
Чтобы свариваемые заготовки эффективно плавились под
действием неплавящегося электрода и аргона и не образовывались дефекты в
сварном шве при изготовлении металлических конструкций, необходимо точно
соблюдать некоторые особенности аргонодуговой сварки. Именно так можно добиться
максимального качества конечного результата.
Неплавящийся вольфрамовый стержень должен как можно глубже
проникать в зазор между заготовками. Сварочная дуга должна быть максимально
короткой. Таким способом можно глубже проводить плавку, что отразиться на
размерах сварного шва. Он будет меньше, а качество выше.
Движение электрода должно производиться строго по центру
зазора, и посередине. Отклонения снижают качество шва и его внешний вид.
Присадочная проволока не должна выходить за пределы сварного
участка, и всегда находиться в зоне аргона. Именно таким образом достигается
защита ванны от негативного воздействия кислорода и азота, находящихся в
воздухе. Их воздействие приведет к повышению хрупкости сварного шва. Те же
самые требования и к неплавкому электроду.
Нельзя резко подавать присадку в сварную зону. Это приведет к
большому разбрызгиванию металла и к его перерасходу.
Подача проволоки при ручной сварке должна производиться под
углом. Никаких поперечных отклонений.
Нельзя при окончании сварки обрывать шов отводом электрода из
зоны сваривания. Нужно просто погасить дугу с помощью реостата.
Подавать защитный газ и выключать его после окончания сварки можно только
через (за) 10 секунд. Таким способом защищается еще неостывший плавящийся
металл, который при соприкосновении с воздухом тут же покроется оксидной
пленкой.
Обязательно перед началом сварочных работ производится подготовка
соединяемых металлических заготовок. Это касается и стали, и алюминия, и других
металлов. Нужно стыкуемые плоскости очистить от грязи, ржавчины и других
материалов, используя железную щетку или болгарку с металлической щетковидной
насадкой. Зачищать надо до металлического блеска. Если есть необходимость
(жирные и масляные пятна), то соединяемые поверхности придется обезжирить
растворителем или спиртом.
Обязательно сопоставляются режимы сварки с толщиною стыкуемых заготовок,
учитывая диаметр неплавящегося электрода.
сто погасить дугу с помощью реостата.
4. Способы исправления дефектов.
Чрезмерное усиление шва устраняют с помощью абразивного
инструмента или пневматического зубила.
Непровар, кратеры, пористость и неметаллические включения
устраняют путем вырубки пневматическим зубилом или расчистки абразивным
инструментом всего дефектного участка с последующей заваркой. Часто применяют
выплавку дефектного участка резаком поверхностной кислородной или
воздушно-дуговой резки.
Подрезы заваривают тонкими швами. Наплывы устраняются
обработкой абразивным инструментом или с помощью пневматического зубила.
Наружные трещины устраняются разделкой и последующей
заваркой. Для предупреждения распространения трещины по концам ее сверлят
отверстия. Разделку трещины
выполняют зубилом или резаком. Кромки разделки зачищают от
шлака, брызг металла, окалины и заваривают. Швы с внутренними трещинами
вырубывают и заваривают заново. При наличии сетки трещин дефектный участок
вырезают и взамен сваркой накладывают заплату.
Изучить: 1. Наиболее
распространенные включения.
2. Меры, предупреждающие образованию дефектов в швах
конструкций.
3. Исправление дефектов.
группа: 412
Предмет: Техника и технология ручной дуговой сварки (наплавка, резка) неплавящимися электродами в защитном газе.
Тема урока: Причины возникновения дефектов сварных швов ручной дуговой сварки (наплавка, резка) неплавящимися электродами в защитном газе.
Дефекты
сварных швов при сварке и наплавке
Напряжения,
существующие после окончания сварки или наплавки до полного остывания детали,
называют остаточными сварочными напряжениями. Они возникают в результате
затруднения расширения и сжатия металла при его нагреве и остывании.
Различают
сварочные напряжения трех родов: линейные или одноосные, действующие только по
одной оси в одном направлении; плоскостные или двухосные; объемные или
трехосные. По направлению действия различают следующие напряжения: продольные и
поперечные, расположенные перпендикулярно к оси сварочного шва. Для низкоуглеродистых
и низколегированных сталей в основном характерны сварочные напряжения первого
рода, которые уравновешиваются внутренними напряжениями восстанавливаемой
детали.
При
разработке технологического процесса восстановления деталей с помощью сварки и
наплавки необходимо обеспечить минимальные значения сварочных напряжений или
предусмотреть их снятие. Если значения сварочных напряжений достигнут предела
текучести металла, то они вызовут его пластическую деформацию, т.е. коробление
детали.
Деформации
бывают временные, существующие только во время проведения сварочных работ, и
остаточные, которые остаются после остывания деталей. В зависимости от формы и
размеров деталей различают деформацию в плоскости, вызывающую уменьшение
размеров конструкции, и угловую деформацию, которая вызывает образование
выпучин, грибовидный изгиб и смещение осей цилиндрических поверхностей.
Значение и характер остаточных напряжений в значительной степени определяются
размерами и свойствами восстанавливаемых деталей, режимами сварки и наплавки,
последовательностью наложения швов и их формой. При растягивающих напряжениях в
наплавленной детали снижается усталостная прочность, повышается коробление, возникает
усадка по длине, а также ухудшается сопротивление детали переменным нагрузкам.
Деформация изгиба увеличивается пропорционально квадрату длины валика.
По
расположению в шве дефекты бывают наружные и внутренние.
К наружным
дефектам относят продольные и поперечные горячие и холодные трещины,
подрезы, кратеры, остатки шлака, неровную поверхность шва, наплывы и др.
Горячие (микро- и
макроскопические) трещины (рис. 13.5, а) образуются
в процессе сварки углеродистых сталей при температуре 1200— 1350°С. На образование
трещин влияют вредные примеси (углерода, кремния, серы, фосфора и водорода) в
металле валика. При наличии в сварочном шве полезных примесей (марганца, никеля
и хрома) уменьшается вероятность появления горячих трещин.
Холодные
трещины (см.
рис. 13.5, бив) возникают при температуре ниже 400°С. Их делят
на закалочные и хрупкие.
Закалочные трещины образуются на границе сплавления в средне- и высоколегированных сталях перлитного и мартенситного классов вследствие того, что объем металла увеличивается и имеют место структурные напряжения. Если неизбежно образование мартенсита, то сварку и наплавку ведут малым током и с большой скоростью.
Рис.
13.5. Дефекты сварных швов:
7 и 2 —
продольные трещины в шве и околошовной зоне; 3 и 4 — поперечные трещины в шве и
околошовной зоне; 5 — поперечные трещины по толщине свариваемого металла; а —
горячие трещины; бив — холодные трещины; гиб — подрез; ей ж — наплывы; з-л —
непровар; м — поры; н — шлаковые включения
Тогда иглы мартенсита будут маленькими и возникающие напряжения недостаточны
для разрушения металла.
Хрупкие
трещины появляются в наплавленном слое при его быстром охлаждении. Они
распространяются из наплавленного металла в основном с большой скоростью
(1200—1800 м/с). Для их предупреждения нужно предварительно подогревать детали
перед наплавкой, что способствует распаду аустенита, и после медленно
охлаждать.
Появлению
холодных трещин способствует повышенное содержание в металле серы, фосфора,
водорода, кислорода и других вредных примесей.
Подрез (см. рис. 13.5, гид)
характеризуется наличием канавки у края шва. Он получается при сварке током
большой силы или горелкой большой мощности.
Кратеры (незаплавленные углубления),
остатки шлака и неровные поверхности шва образуются в результате работы
сварщика низкой квалификации.
Наплывы (см. рис. 13.5, ей ж) происходят
при слишком быстром плавлении электрода и недостаточном нагреве свариваемого
металла.
К внутренним
дефектам относят непровар корня шва или его кромки, поры, шлаковые
включения, пережог металла шва и др.
Непровар (см. рис. 13.5, з—л) характеризуется
плохим сцеплением или даже отсутствием сцепления наплавленного металла с
основным. Этот дефект получается при недостаточном прогреве свариваемого или
наплавляемого металла, малом угле разделки трещины, малом токе или малой
мощности горелки, а также из-за большой скорости сварки.
Поры (см. рис. 13.5, м) возникают
только на границе раздела фаз твердого и жидкого металла, что объясняется
наличием в нем пузырьков газа СО, С02, Н2 и др. Они
образуются при большой влажности электродов или неправильной регулировке
газовой горелки, плохой очистке свариваемых и наплавляемых поверхностей от
масла, грязи и окалины.
Шлаковые
включения (см.
рис. 13.5, н) образуются при сварке длинной дугой или окислительным
пламенем.
Пережог представляет собой окисленный
крупнозернистый металл шва вследствие применения тока большой силы, медленного
перемещения электрода или горелки. Наружные дефекты швов контролируют визуально
или через лупу с 10—20-кратным увеличением. Для выявления трещин применяют
травление шва 10%-м раствором азотной кислоты.
Внутренние
дефекты обнаруживают ультразвуковым или металлографическим методом,
просвечиванием шва рентгеновскими или гамма-лучами.
Изучить: 1. Изучить причины
возникновения дефектов и напряжений?
2. Наружные дефекты сварных швов.
3. Внутренние дефекты
сварных швов.
группа: 412
Предмет: Техника и технология ручной дуговой сварки (наплавка, резка) неплавящимися электродами в защитном газе.
Тема урока: Назначение и условия работы контрольно-измерительных приборов, правила эксплуатации и область их применения.
Любые сварочные работы требуют применения
специализированного оборудования. К такому относятся источники питания
(трансформаторы, инверторы, выпрямители), собственно сам сварочный аппарат,
держатель электродов, газовая горелка и прочее.
Отметим, что набор сварочного оборудования для
разных способов сварки будет отличаться. Кроме того, имеет отличия само
сварочное оборудование, и его эксплуатация также может быть различной: одно
допускается для передвижных постов, другое может использоваться только
стационарно и прочее.
Заметим, что сварочное оборудование и его
эксплуатация должны отвечать ряду требований, о которых мы и предлагаем
поговорить дальше.
Разновидности сварочного оборудования.
Отметим, что все оборудование для сварки разделяется
по способу применения – одни аппараты предназначены для бытового использования
непрофессиональными сварщиками, с другими могут работать исключительно
специалисты в области сварки. Главное отличие бытовых и профессиональных
устройств состоит в том, что первые более просты в управлении, а также имеют, в
отличие от профессиональных, меньшие габариты и работают на меньшем напряжении.
Собственно сварочные аппараты также различаются:
одни предназначены для дуговой сварки, другие для проведение газосварочных
работ и пр. Разными они могут быть и по степени
механизации процесса – полуавтоматические, автоматические аппараты.
Все
сварочное оборудование условно подразделяют на два класса, а именно:
Собственно, сварочное оборудование – аппараты и
инструменты, которые используются непосредственно для сваривания металлов. К
этому классу относят – инверторы, держатели электродов, газовые горелки,
различные клапаны и газосмесители, пр.
Защитное оборудование – все инструменты, спецодежда
и устройства, предназначенные для защиты сварщика во время процесса
сварки.
Эксплуатация
и обслуживание сварочного оборудования.
Основные правила эксплуатации любого оборудования
прописываются в инструкциях производителей, сварочные аппараты и инструменты не
исключение. Правилами безопасности четко указывается, что все сварочные работы
должны производиться исключительно по инструкциям и установленным требованиям.
Выполнение правил эксплуатации сварочного
оборудование не только будет способствовать бесперебойной и долгой работе
аппаратов и инструментов, но и создаст безопасные условия для проведения
сварочных работ. А дополнительные защитные средства сварщика обезопасят его от
сопутствующих процессу сварки негативных явлений: разбрызгивания расплавленного
металла, ультрафиолетового излучения и прочего.
Кроме того, жесткие требования предъявляются по
организации рабочего места. Здесь необходимо соблюсти правила пожарной
безопасности, подключения электроустановок, проветривания помещения,
предназначенного для проведения сварочных работ.
При эксплуатации оборудования для электродуговой
сварки подключение выпрямителей или трансформаторов выполняют строго по
инструкции. Обязательно проводится заземление корпусов аппаратов и других
металлических-нетоковедущих частей сварочного оборудования. Заземлению подлежит
и рабочее место специалиста – сварочные станки и столы, плиты и прочее.
Заземление проводится посредством гибких медных
проводков (могут применяться провода из других электропроводящих металлов).
Отметим, что запрещено последовательно включать в заземляющий проводник несколько
установок для сварки.
Следует также соблюдать правила работы с держателями
электродов и горелками. Эти инструменты запрещается направлять на людей. Кроме
того, за их состоянием необходимо постоянно следить и во время производить
очистку и ремонт комплектующих.
Все сварочное оборудование должно содержаться в
сухом помещении. Не следует допускать падений аппаратов и устройств, во
избежание механических повреждений. При регулярной эксплуатации оборудования
каждые шесть месяцев осуществляется очистка, плановая проверка и при
необходимости ремонт. Обязательно
очищать все сварочные аппараты от пыли и грязи, которые скапливаются внутри
устройства.
Ответственность за правильную эксплуатацию
сварочного оборудования несет сварщик. Он обязан работать только в строго
заданных режимах, использовать электросварочные установки по назначению,
следить за их сохранностью, а также соблюдать технику безопасности. Заметим,
что самостоятельно работать на сварочном оборудовании, без присмотра
специалиста, могут только операторы, прошедшие обучение полуавтоматической и
автоматической сварке и инструктаж по правилам безопасности работ.
В противном случае сварочные работы должны
производиться исключительно двумя специалистами – непосредственно сварщиком и
наблюдателем.
Эксплуатация сварочного оборудования с соблюдением
правил и техники безопасности повысит срок службы устройств и снизит риск
возникновения опасных ситуаций.
Изучить: 1. Сварочное оборудование?
2. Инструменты сварщика?
3. Эксплуатация и
обслуживание сварочного оборудования?
группа: 412
Предмет: Техника и технология частично механизированной сварки (наплавка) плавлением в защитном газе.
Тема урока: Флюсы для сварки плавлением.
История возникновения
сварки под слоем флюса
В 1927г. известный изобретатель Д.С. Дульчевский, работавший
в Одесских железнодорожных мастерских, разработал свой первый автомат для
сварки под флюсом. Идея этого способа сварки появилась не на пустом
месте. Еще Н.Г. Славянов применял для защиты расплавленного металла от
воздействия воздуха битое стекло. Создание данного способа сварки потребовало
разработки оборудования принципиально нового типа.
Во время Великой Отечественной войны в Институте
электросварки, который активно включился в работу на нужды оборонной
промышленности в Нижнем Тагиле на Уралвагонзаводе, где изготовлялись знаменитые
танки Т-34, начал свою научно-техническую деятельность Б.Е. Патон, проводя
исследования по автоматическому регулированию процессов сварки с непрерывной
подачей в зону дуги присадочных материалов.
В 1942г. были начаты работы по созданию полуавтоматической
сварки под флюсом. При этом процессе была механизирована лишь подача сварочной
проволоки в зону дуги, осуществляемая по мере ее плавления специальным
устройством – подающим механизмом. Все остальные операции, в том числе
перемещение горелки по стыку, обеспечение постоянства дугового промежутка,
осуществляются сварщиком. Полуавтоматическая сварка под флюсом не получила широкого
распространения. Это связано с тем, что в процессе выполнения сварки было
невозможно визуальное наблюдение за положением электрода по отношению к
свариваемым кромкам. Сварку можно было вести только в нижнем положении. В
1952г. для сварки алюминия разработан вариант, при котором для защиты зоны дуги
применяется тонкий дозированный слой флюса. Он обеспечивает защиту только
нижней части дуги и поверхности сварочной ванны. В связи с этим данный процесс
получил название «сварка по флюсу». Он нашел применение в промышленности для
сварки цветных металлов.
Изучение нового материала.
- Флюс
защищает капли электродного металла и жидкий металл сварочной ванны
от воздействия воздуха, обеспечивает устойчивое горение дуги, хорошее
формирование шва и образует шлаковую корку, легко отделимую от поверхности шва
после затвердевания.
- Различают
флюсы общего назначения и специальные.
Флюсы общего назначения предназначены для механизированной дуговой сварки и
наплавки углеродистых и низколегированных сталей низкоуглеродистой и
легированной сварочной проволокой, специальные флюсы - для отдельных видов
сварки, например, электрошлаковой или сварки высоколегированных сталей.
- По
способу изготовления флюсы делятся на: плавленные и неплавленные.
Плавленые флюсы получают путем сплавления компонентов шихты в электрических
или пламенных печах.
При изготовлении неплавленных флюсов частицы флюсовой шихты скрепляют без их
сплавления. К числу неплавленных флюсов относятся керамические и спеченные
флюсы, а также флюсы-смеси. Керамические флюсы производят из смесей
порошкообразных материалов, скрепляемых с помощью клеющих веществ, главным
образом жидкого стекла. Спеченные флюсы изготовляют путем спекания компонентов
шихты при повышенных темпера турах без их сплавления. Полученные комки затем
измельчают до требуемого размера.
Наиболее широко
распространен процесс при использовании одного электрода — однодуговая сварка.
Сварочная дуга горит между голой электродной проволокой и изделием, находящимся
под слоем флюса. В расплавленном флюсе газами и парами флюса и расплавленного
металла образуется полость — газовый пузырь, в котором существует сварочная
дуга. Давление газов в газовом пузыре составляет 7 — 9 г/см2, но в
сочетании с механическим давлением, создаваемым дугой, его достаточно для
оттеснения жидкого металла из-под дуги, что улучшает теплопередачу от нее к
основному металлу. Повышение силы сварочного тока увеличивает механическое
давление дуги и глубину проплавления основного металла.
Кристаллизация расплавленного
металла сварочной ванны приводит к образованию сварного шва. Затвердевший флюс
образует шлаковую корку на поверхности шва. Расплавленный флюс, образуя пузырь
и покрывая поверхность сварочной ванны, аффективно защищает расплавленный
металл от взаимодействий с воздухом.
Металлургические взаимодействия между
расплавленным металлом и шлаком способствуют получению металла шва с требуемым
химическим составом. В отличие от ручной дуговой сварки металлическим
электродом при сварке под флюсом, так же как и при сварке в защитных газах,
токоподвод к электродной проволоке осуществляется на небольшом расстоянии
(вылет электрода) от дуги (до 70мм). Это позволяет без перегрева электрода
использовать повышенные сварочные токи (до 2000 А). Плотность сварочного тока
достигает 200—250 А/мм2, в то время как при ручной дуговой сварке не
превышает 15 А/мм2. В результате повышается глубина проплавления
основного металла и скорость расплавления электродной проволоки, т. е.
достигается высокая производительность процесса. Дуга в процессе сварки не
видна, сварщику не требуется защитная маска и тяжелая защитная одежда .
К недостаткам способа относится возможность сварки только в
нижнем положении ввиду возможного стекания расплавленных флюса и металла при
отклонении плоскости шва от горизонтали более чем на 10-15 градусов .
Классификация сварочных автоматов и
полуавтоматов
Автоматы для сварки под
флюсом классифицируются:
– по способу перемещения вдоль шва – тракторного типа,
подвесные и самоходные
– по количеству электродов – одноэлектродные, многоэлектродные (несколькими
изолированными токоподводами, от раздельных источников сварочного тока или
расщепленным электродом от одного источника);
– по типу плавящегося электрода –для сварки электродной проволокой, ленточным
электродом или стержнями;
– по роду тока – для сварки на постоянном или переменном токе.
В зависимости от способа перемещения дуги относительно
изделия сварка выполняется автоматически и полуавтоматически. При
автоматической сварке подача электродной проволоки в дугу и перемещение ее
осуществляется специальными механизмами .
При полуавтоматической сварке дугу перемещает сварщик
вручную.
Этот способ широко применяется в промышленности при производстве конструкций из
сталей, цветных металлов и сплавов. Это объясняется высокой производительностью
процесса и высоким качеством и стабильностью свойств сварного соединения,
улучшенными условиями работы; более низким, чем при ручной сварке, расходом
материалов и электроэнергии.
Основные узлы автоматов для сварки под слоем
флюса
Автомат для сварки под флюсом включает следующие основные
узлы: механизм подачи электродной проволоки (ленты), токоподвод, механизмы
настроечных или регулировочных перемещений, кассету с электродной проволокой,
флюсовую аппаратуру, тележку (для перемещения относительно изделия), пульт
управления .
Источник питания
Источник питания для автоматической сварки должен иметь
внешнюю характеристику, зависящую от способа поддержания непрерывного горения
дуги. В системе саморегулирования используются источники с жесткой
характеристикой, в системе автоматического регулирования напряжения – с
падающей характеристикой. Как и автомат в целом, источники питания
изготавливают на сравнительно большие токи – от 315 до 1600 А. Источники могут
иметь относительно высокое напряжение холостого хода – до 141 В, но это
напряжение должно автоматически отключаться при окончании сварки. Источник
должен обеспечивать дистанционное управление током или напряжением, поскольку
обычно он находится на значительном расстоянии от автомата. В качестве
источников питания для автоматической сварки наиболее часто используют
трансформаторы и выпрямители с электрическим управлением – магнитным или
тиристорным.
Сварочная головка
Основными элементами сварочной головки являются: механизм
подачи проволоки, подающие ролики, токоподводящий мундштук и устройства для
установочных перемещений головки. Основные функции сварочной головки – это
подача в зону сварки сварочного материала и подвод к нему напряжения,
поддержание стабильных параметров сварки или их изменения по заданной
программе. Механизм подачи состоит из электродвигателя и редуктора. При
использовании электродвигателей переменного тока применяют регулируемые
редукторы. Электродвигатели постоянного тока могут работать в сочетании с
нерегулируемыми редукторами. Подающие ролики расположены на выходных валах
редуктора. Их назначение – стабильная подача сварочной проволоки без
проскальзывания. Обычно это достигается при использовании двух пар подающих роликов.
К корпусу редуктора крепится токоподводящий мундштук для обеспечения
электрического контакта и направления проволоки в сварочную ванну. Мундштуки
могут быть трубчатыми, колодочными, или роликовыми. Конструкция подвески
сварочной головки должна обеспечивать возможность ее установочных перемещений:
вертикальное – для установления необходимого вылета электрода или угла наклона
его относительно свариваемого стыка; поперечное – для установки торца электрода
по центру стыка в начале и корректировки его в процессе сварки.
Механизм перемещения по
стыку свариваемых деталей
Механизм перемещения по стыку свариваемых деталей
представляет собой передвигающуюся по рельсам или направляющим тележку. В
большинстве автоматов тележка выполняет роль базового элемента. На ее корпусе
устанавливают сварочную головку, кассету для проволоки пульт управления
автоматом. Тележка должна обеспечивать плавность хода в широком диапазоне
скоростей сварки. Различают тележки тракторного и кареточного типов. Тележка
тракторного типа перемещается с помощью бегунковых колес либо по направляющим
рельсам, либо непосредственно по свариваемому изделию. Тележка кареточного типа
перемещается только по направляющим стапеля или устройства крепления самого
автомата.
Система
управления сварочным автоматом
Система управления сварочным автоматом имеет
основное устройство – шкаф управления. В нем находятся автоматический
выключатель для соединения с сетью, понижающий трансформатор с выпрямительными
блоками для питания всех элементов системы, промежуточные реле, блоки
управления отдельными частями системы, предохранители и др. Современные системы
управления строятся на основе микропроцессорной техники, в этом случае шкаф
может быть укомплектован монитором для визуализации настройки и хода процесса
сварки и принтером для его документирования.
Шкаф управления может располагаться отдельно или встраиваться
в корпус источника. Панель управления, как правило, располагается на сварочном
автомате и содержит органы непосредственной настройки и наблюдения за сварочным
процессом: потенциометры, тумблеры, кнопки, электроизмерительные приборы и др.
С панели подают команды для настроечных перемещений приводов, а также главные
команды: пуск и стоп сварки.
Пульт дистанционного управления соединен со шкафом длинным
проводом и переносится оператором в удобное для наблюдения процесса место. С
его помощью дублируется только часть команд, реализуемых панелью управления.
Кассеты для проволоки
Наибольшее распространение при сварке проволокой 3-5мм получили
кассеты закрытого типа. На шланговых аппаратах (проволока диаметром до 2мм)
устанавливают, как правило, кассеты открытого типа. На некоторых сварочных
аппаратах устанавливают крестовины для проволоки или конические катушки.
Модели автоматов для сварки под слоем флюса
Самоходный автомат А-1412, предназначенный для двухдуговой
сварки под слоем флюса на переменном токе, комплектуется двумя трансформаторами
типа ТДФЖ-2002. Он конструктивно унифицирован с автоматом А-1416 и
содержит те же основные узлы. Тележка перемещается с маршевой скоростью от
асинхронного электродвигателя, с рабочей скоростью – от
электродвигателя постоянного тока. Ее рабочая скорость регулируется путем
изменения частоты вращения электродвигателя в десятикратном диапазоне с помощью
тиристорного регулятора.
Отечественные сварочные автоматы по своим техническим данным и
назначению полностью удовлетворяют основные потребности промышленности.
Технология сварки под слоем флюса.
- сила сварочного тока, его род и полярность, напряжение
дуги, скорость сварки, диаметр и скорость подачи электродной проволоки.
- вылет электрода (расстояние от его торца до мундштука),
наклон электрода или изделия, марка флюса, подготовка кромок и вид сварного
соединения.
- с увеличением силы сварочного тока глубина проплавления
основного металла увеличивается, ширина шва при этом остается неизменной.
- с повышением напряжения на дуге при неизменном токе сварки увеличивается
длина и подвижность дуги, в результате чего значительно возрастает ширина шва и
уменьшается высота усиления. Глубина проплавления уменьшается незначительно.
- увеличение силы сварочного тока при увеличении
толщины свариваемого изделия должно обязательно сопровождаться соответствующим
повышением напряжения дуги.
Таким образом, форма и размеры шва зависят от многих
параметров режима сварки: величины сварочного тока, напряжения дуги,
диаметра электродной проволоки, скорости сварки и др. Такие параметры, как
наклон электрода или изделия, величина вылета электрода, грануляция флюса, род
тока и полярность и т. п. оказывают меньшее влияние на форму и размеры
шва.
Необходимое условие сварки - поддержание дуги. Для
этого скорость подачи электрода должна соответствовать скорости его плавления
теплотой дуги. С увеличением силы сварочного тока скорость подачи электрода
должна увеличиваться. Электродные проволоки меньшего диаметра при равной силе
сварочного тока следует подавать с большей скоростью. Условно это можно
представить как расплавление одинакового количества электродного металла при
равном количестве теплоты, выделяемой в дуге (в действительности количество
расплавляемого электродного металла несколько увеличивается с ростом плотности
сварочного тока). При некотором уменьшении скорости подачи длина дуги и ее
напряжение увеличиваются. В результате уменьшаются доля теплоты, идущая на
расплавление электрода, и количество расплавляемого
электродного металла.
Влияние параметров режима на форму и размеры шва
обычно рассматривают при изменении одного из них и сохранении остальных
постоянными. Приводимые ниже закономерности относятся к случаю наплавки на
пластину, когда глубина проплавления не превышает 0,7 ее толщины (при большей
глубине проплавления ухудшение теплоотвода от нижней части сварочной ванны
резко увеличивает глубину проплавления и изменяет форму и
размеры шва).
С увеличением силы сварочного тока глубина
проплавления возрастает почти линейно до некоторой величины. Это объясняется
ростом давления дуги на поверхность сварочной ванны, которым оттесняется
расплавленный металл из-под дуги (улучшаются условия теплопередачи от дуги к
основному металлу), и увеличением погонной энергии. Ввиду того, что повышается
количество расплавляемого электродного металла, увеличивается и высота усиления
шва. Ширина шва возрастает незначительно, так как дуга заглубляется в основной
металл (находится ниже плоскости основного металла).
Увеличение плотности сварочного тока (уменьшение
диаметра электрода при постоянном токе) позволяет резко увеличить глубину
проплавления. Это объясняется уменьшением подвижности дуги. Ширина шва при этом
уменьшается. Путем уменьшения диаметра электродной проволоки можно получить шов
с требуемой глубиной проплавления в случае, если величина максимального
сварочного тока, обеспечиваемая источником питания дуги, ограничена. Однако при
этом уменьшается коэффициент формы провара шва и интенсифицируется зональная
ликвация в металле шва, располагающаяся в его рабочем сечении. Род и полярность
тока оказывают значительное влияние на форму и размеры шва, что объясняется
различным количеством теплоты, выделяющимся на катоде и аноде дуги.
При сварке на постоянном токе прямой полярности
глубина проплавления на 40 - 50%, а на переменном - на 15 - 20% меньше, чем при
сварке на постоянном токе обратной полярности. Поэтому швы, в которых
требуется небольшое количество электродного металла и большая глубина
проплавления (стыковые и угловые без разделки кромок), целесообразно выполнять
на постоянном токе обратной полярности. При увеличении напряжения дуги (длины
дуги) увеличивается ее подвижность и возрастает доля теплоты дуги, расходуемая
на расплавление флюса (количество расплавленного флюса). При этом растет ширина
шва, а глубина его проплавления остается практически постоянной. Этот параметр
режима широко используют в практике для
регулирования ширины шва.
Увеличение скорости сварки уменьшает погонную
энергию и изменяет толщину прослойки расплавленного металла под дугой. В
результате этого основные размеры шва уменьшаются. Однако в некоторых случаях
(сварка тонкими проволоками на повышенной плотности сварочного тока) увеличение
скорости сварки до некоторой величины, уменьшая прослойку расплавленного
металла под дугой и теплопередачу от нее к основному металлу, может привести к
росту глубины проплавления. При чрезмерно больших скоростях сварки и силе
сварочного тока в швах могут образовываться подрезы.
С увеличением вылета электрода возрастает
интенсивность его подогрева, а значит, и скорость его плавления. В результате
толщина прослойки расплавленного металла под дугой увеличивается и, как
следствие этого, уменьшается глубина проплавления. Этот эффект иногда
используют при сварке электродными проволоками диаметром 1-3мм для увеличения
количества расплавляемого электродного металла при сварке швов, образуемых в
основном за счет добавочного металла (способ сварки с увеличенным вылетом
электрода). В некоторых
случаях, особенно при автоматической наплавке, электроду сообщают колебания
поперек направления шва с различной амплитудой и частотой, что позволяет в
широких пределах изменять форму и размеры шва. При сварке с поперечными
колебаниями электрода глубина проплавления и высота усиления уменьшаются, а
ширина шва увеличивается и обычно несколько больше амплитуды колебаний. Этот
способ удобен для предупреждения прожогов при сварке стыковых соединений с повышенным
зазором в стыке или уменьшенным притуплением кромок. Подобный же эффект
наблюдается при сварке сдвоенным электродом, когда электроды расположены
поперек направления сварки. При их последователь ном расположении глубина
проплавления, наоборот, возрастает.
Состав и строение частиц флюса оказывают заметное влияние на форму и размеры
шва. При уменьшении насыпной массы флюса (пемзовидные флюсы) повышается
газопроницаемость сдоя флюса над сварочной ванной и, как результат этого,
уменьшается давление в газовом пузыре дуги. Это приводит к увеличению толщины
прослойки расплавленного металла под дугой, а значит, и к уменьшению глубины
проплавления. Флюсы с низкими стабилизирующими свойствами, как правило,
способствуют более глубокому проплавлению.
Пространственное положение электрода и изделия при сварке под флюсом оказывает
такое же влияние на форму и размеры шва, как и при ручной сварке. Для
предупреждения отекания расплавленного флюса, ввиду его высокой жидкотекучести,
сварка этим способом возможна только в нижнем положении при наклоне изделия на
угол не более 10 -15°. Изменение формы и размеров шва наклоном изделия находит
практическое применение только при сварке кольцевых стыков труб ввиду сложности
установки листовых конструкций в наклонное положение. Сварка с наклоном
электрода находит применение для повышения скорости многодуговой сварки.
Подогрев основного металла до температуры 100°С и выше приводит к увеличению
глубины провара и ширины шва.
Область применения
Механизированная сварка под флюсом является одним из основных
способов сварки плавлением. Если в первые годы освоения сварку под флюсом
применяли только при изготовлении сварных конструкций из низкоуглеродистых
сталей, то сейчас успешно сваривают низколегированные, легированные и высоколегированные
стали различных классов, сплавы на никелевой основе. Освоена сварка под флюсом
титана и его сплавов. Под флюсом сваривают медь и ее сплавы. По флюсу, а в
последние годы и под флюсом сваривают алюминий и его сплавы. Изделия,
полученные сваркой под флюсом, надежно работают при высоких температурах и в
условиях глубокого холода, в агрессивных средах, в вакууме и в условиях высоких
давлений.
Наиболее выгодно использовать механизированную
сварку под флюсом при производстве однотипных сварных конструкций, имеющих
протяженные швы и удобных для удержания флюса. Экономически целесообразнее
сваривать под флюсом металл толщиной от 1,5 - 2,0 до 60мм. Нецелесообразно
сваривать конструкции с короткими швами.
Изучить: 1. Для чего служит флюс?
2. Как
осуществляется сварка под флюсом?
3. Какие
классы автоматов для сварки под флюсом вы знаете?
03.02.2022
группа: 412
Предмет: Техника и технология частично механизированной сварки (наплавка) плавлением в защитном газе.
Тема урока: Наплавочные материалы: электродные проволоки сплошного сечения, холоднокатаные электродные ленты, порошковые проволоки.
Получение наплавленного слоя с особыми свойствами,
как правило, связано с использованием сплавов со значительным количеством
легирующих элементов.
Для наплавки применяются проволоки сплошного сечения
и порошковые, ленты холоднокатаные, порошковые и спеченные порошки, покрытые
электроды, литые прутки, гибкие шнуры, флюсы плавленые и керамические и другие
материалы.
При дуговой наплавке плавящимся или неплавящимся
электродом в среде защитных инертных газов и плазменной наплавке химический
состав наплавленного металла по всем основным легирующим элементам примерно
соответствует химическому составу электродного материала.
При наплавке в среде защитных газов легирование
наплавленного металла достигается в основном выбором соответствующего
присадочного металла (электродная проволока сплошного сечения, порошковая и
др.) или применением дополнительных наплавочных материалов (паст, перед сваркой
наносимых на кромки, или присадочных прутков, порошков, засыпаемых на
поверхность перед сваркой или вдуваемых в сварочную ванну, дополнительных
проволок, прутков, укладываемых на поверхность или подаваемых в сварочную
ванну, и др.).
Наплавка электродами, имеющими специальные покрытия,
позволяет обеспечить довольно значительное легирование через составляющие
электродного покрытия (обычно вводимые в покрытия в виде порошков металлов,
сплавов или углеродистых составляющих) или посредством выбора состава металлического
стержня электрода.
Переход легирующих элементов из стержня и покрытия
электрода зависит от свойств элемента (его сродства к кислороду, температуры
испарения и др.), от композиции электродного покрытия и металла стержня
электрода, а также от коэффициента массы покрытия. Варьируя составы
электродного стержня и покрытия, можно получить множество составов
наплавленного металла, легированных различными элементами и, следовательно,
обладающими различными свойствами в исходном состоянии после наплавки или после
последующей термообработки.
При наплавке под флюсом легирование осуществляется,
как правило, с использованием следующих материалов.
1. Углеродистая или легированная электродная
проволока сплошного сечения, металлическая холоднокатаная, литая или
спрессованная из порошков ленты и нелегирующие или слаболегирующим,
слабоокислительные плавленые, а также керамические флюсы (хотя иногда для наплавки
углеродистых и низколегированных сталей используют высококремнистые,
высокомарганцовистые флюсы, приводящие к окислению ряда легирующих элементов
при наплавке).
2. Порошковая проволока (порошковая лента) при тех
же флюсах. Порошковая проволока может содержать до ~ 40 % легирующих
металлических составляющих от общей массы проволоки. В ленты сложной формы
может быть введено до 70 % легирующих металлических составляющих.
3. Легирующие флюсы, в основном керамические,
содержащие легирующие металлические добавки, и флюсы-смеси.
4. Порошки, предварительно засыпаемые на
наплавляемую поверхность или используемые в процессе наплавки, а также
легированные прутки, укладываемые на наплавляемую поверхность и др.
Применение в качестве плавящегося электрода ленты
весьма целесообразно. В качестве наплавочных применяют обычно ленты
холоднокатаные толщиной 0,4 – 1 мм и шириной 20 – 100 мм, а также ленты,
получаемые прокаткой залитого в охлаждаемые валки жидкого металла (например,
чугуна) и спрессованные холодной прокаткой из порошков и дополнительно спеченные
– металлокерамические.
Весьма разнообразные составы наплавленного металла
могут быть получены посредством порошковых проволок и лент, изготовляемых из
низкоуглеродистой ленты и сердечника, состоящего из смеси металлических
порошков или смеси металлических порошков и газо- и шлакообразующих
компонентов.
Керамические флюсы обычно используют при наплавке
низкоуглеродистой и низколегированной проволокой. Так, керамический флюс АНК-18
(~ 6,5 % СаСО3; ~ 27 % CaF2; ~ 28 % MgO; ~ 18 %Аl2O3; ~ 2,5 Na2O +K2O; ~ 6 %
Cr; ~ 2,5 % Mn; ~ 0,16 % С; ~ 2 % Al; ~ 0,25 Ti; ~ 0,25 % Si и 3,5 % Fe) при
использовании нелегированной проволоки марки Св-08А при оптимальных режимах
обеспечивает получение наплавленного металла состава 0,15 – 0,25 % С; 0,2 – 0,4
% Si; 1 – 1,8 % Mn; 3 – 5 % Cr; S <0,04 %; P <0,03 % и имеющего твердость
HRC
35 – 45.
Изучить: 1. Получение
наплавленного слоя с особыми свойствами.
2. Применение
в качестве плавящегося электрода ленты.
3. Составы наплавленного металла.
группа: 412
Предмет: Техника и технология частично механизированной сварки (наплавка) плавлением в защитном газе.
Тема урока: Активные защитные газы, смеси газов.
Инертные
Не вступают в химическое взаимодействие с металлами и практически не растворяются в металлах
Аргон (Ar) - бесцветный, без запаха, негорючий, неядовитый газ, почти в 1,5 раза тяжелее воздуха. В металлах нерастворим как в жидком, так и в твердом состояниях. Выпускается (ГОСТ 10157-79) двух сортов: высшего и первого.
В газе высшего сорта содержится 99,993 % аргона, не
более 0,006 % азота и не более 0,0007 % кислорода. Рекомендуется для сварки
ответственных металлоконструкций из активных и редких металлов и сплавов,
цветных металлов.
В газе первого сорта содержится 99,98 % аргона, до
0,01 % азота и не более 0,002 % кислорода. Рекомендуется для сварки стали и
чистого алюминия.
Гелий (Не) - бесцветный газ, без запаха,
неядовитый, значительно легче воздуха и аргона. Выпускается (ГОСТ 20461-75)
двух сортов: высокой чистоты (до 99,985 %) и технический (99,8%).
Используется реже, чем аргон, из-за его дефицитности и
высокой стоимости. Однако при одном и том же значении тока дуга в гелии
выделяет в 1,5 - 2 раза больше энергии, чем в аргоне. Это способствует более
глубокому проплавлению металла и значительному увеличению скорости сварки.
Гелий применяют при сварке химически чистых и активных
материалов, а также сплавов на основе алюминия и магния.
Азот (N2) - газ без цвета, запаха п
вкуса, неядовитый. Используется только для сварки меди и ее сплавов, по
отношению к которым азот является инертным газом. Выпускается (ГОСТ 9293-74)
четырех сортов: высшего - 99,9% азота; 1-го - 99,5%; 2-го - 99,0%; 3-го -
97,0%.
Активные
Защищают
зону сварки от воздуха, но сами растворяются в жидком металле либо вступают с
ним в химическое взаимодействие
Кислород (О2) - газ без цвета, запаха и
вкуса. Негорючий, но активно поддерживающий горение. Технический газообразный
кислород (ГОСТ5583-78) выпускается трех сортов: 1-й сорт - 99,7% кислорода; 2-й
- 99,5%; 3-й - 99,2%. Применяется только как добавка к инертным и активным
газам.
Углекислый
газ (СО2) -
бесцветный, со слабым запахом, с резко выраженными окислительными свойствами,
хорошо растворяется в воде. Тяжелее воздуха в 1,5 раза, может скапливаться в
плохо проветриваемых помещениях, в колодцах, приямках. Выпускается (ГОСТ 8050-85)
трех сортов: высший-99,8% СО2, 1-й-99,5% и 2-й-98,8%. Двуокись
углерода 2-го сорта применять не рекомендуется. Для снижения влажности СО2 рекомендуется
установить баллон вентилем вниз и через 1-2 ч открыть вентиль на 8-10 с для
удаления воды. Перед сваркой из нормально установленного баллона выпускают
небольшое количество газа, чтобы удалить попавший внутрь воздух.
В углекислом газе сваривают чугун, низко- и
среднеуглеродистые, низколегированные конструкционные коррозионностойкие стали.
Газовые смеси
Сварочные
смеси служат для улучшения процесса сварки и качества сварного шва
Смесь аргона
и гелия. Оптимальный
состав: 50% + 50% или 40% аргона и 60% гелия. Пригоден для сварки алюминиевых и
титановых сплавов.
Смесь аргона
и кислорода при
содержании кислорода 1-5% стабилизирует процесс сварки, увеличивает жидко
текучесть сварочной ванны, перенос электродного металла становится
мелкокапельным. Смесь рекомендуется для сварки углеродистых и нержавеющих
сталей.
Смесь аргона
и углекислого газа. Рациональное
соотношение - 75-80% аргона и 20-25% углекислого газа. При этом обеспечиваются
минимальное разбрызгивание, качественное формирование шва, увеличение
производительности, хорошие свойства сварного соединения. Используется при
сварке низкоуглеродистых и низколегированных конструкционных сталей.
Смесь
углекислого газа и кислорода. Оптимальный состав: 60-80% углекислого газа и
20-40% кислорода. Повышает окислительные свойства защитной среды и температуру
жидкого металла. При этой смеси используют электродные проволоки с повышенным
содержанием раскислителей, например Св-08Г2СЦ. Шов формируется несколько лучше,
чем при сварке в чистом углекислом газе. Смесь применяют для сварки
углеродистых, легированных и некоторых высоколегированных конструкционных
сталей.
Смесь аргона, углекислого газа и
кислорода - трехкомпонентная смесь обеспечивает
высокую стабильность процесса и позволяет избежать пористости швов. Оптимальный
состав: 75% аргона, 20% углекислого газа и 5% кислорода. Применяется при сварке
углеродистых, нержавеющих и высоколегированных конструкционных сталей.
конструкционных
сталей.
Изучить:
1. Инертные газы.
2. Активные
газы.
3. Газовые смеси.
01.02.2022
группа: 412
Предмет: Техника и технология ручной дуговой сварки (наплавка, резка) неплавящимися электродами в защитном газе.
Тема урока: Техника и технология сварки углеродистых и низколегированных сталей. Выбор режимов сварки.
Аргонодуговую сварку углеродистой стали неплавящимся
электродам.
Данную технологию широко применяют для сварных соединений, к качеству
которых предъявляют строгие требования. Соединение заготовок осуществляется с
использованием присадочных прутков с повышенным содержанием кремния, который
снижает коэффициент поверхностного натяжения сварочной ванны, снижая
вероятность образования пор. Кроме того, при комбинированном многопроходном
соединении толстостенных конструкций аргонодуговую сварку используют для
получения корневого слоя.
Температура плавления углеродистой стали составляет
1535°С. Наиболее часто аргонодуговой сваркой неплавящимся электродом сваривают
стали, используемые в теплоэнергетике
Углеродистые и низколегированные стали
Марка стали |
Свариваемость |
Технологические особенности сварки |
|
Сталь 10, Сталь 20, 15ГС |
Хорошая |
Присадок Св-08Г2С, Св-08ГС |
Зачистка кромок до металлического
блеска |
12МХ, 15ХМ |
Присадок Св-08НХ, Св-08ХМ |
||
15Г2С |
Удовлетворительная |
Присадок Св-08Г2С, Св-08ГС |
|
12X1МФ, 15Х1М1Ф, 12Х2М1, 12Х2МФСР,
12Х2МФБ |
Присадок Св-08ХМФА, Св-08ХГСМФА |
ТРУДНОСТИ
ПPИ СВАРКИ. Основная
- трудно избежать образования пор из-за недостаточного раскисления основного
металла. Средством борьбы с порообразованием служит снижение доли основного
металла в наплавленном металле шва
Подготовка к
сварке. Для
разделки сталей, а также подготовки кромок используют газовую, плазменную или
воздушно-дуговую резку. После нее участки нагрева металла зачищают резцовым или
абразивным инструментом до удаления следов термообработки. Непосредственно
перед сборкой стыка кромки зачищают на ширину 20 мм до металлического блеска и
обезжиривают.
Стыки собирают в сборочных кондукторах либо с помощью
прихваток, которые выполняют с полным проваром и их переплавкой при наложении
основного шва. Прихватки с недопустимыми дефектами следует удалять механическим
способом. На потолочные участки шва прихватки накладывать не рекомендуется,
поскольку там они труднее поддаются переплавке при выполнении основного шва. На
сталях 10 и 20 прихватки выполняют только с помощью присадочной проволоки. Ее
поверхность должна быть чистой, без окалины, ржавчины и грязи. Очищать
проволоку можно как механическим способом, гак и химическим травлением в 5%-ном
растворе соляной кислоты.
Высота прихваток, мм |
2-3 |
3-4 |
Толщина кромок свариваемых изделий, мм |
до 10 |
св. 10 |
1-5 - очередность установки прихваток А, Б - выводные
планки для начала и окончания сварки
Выбор
параметров режима. Сварку
ведут на постоянном токе прямой полярности. Сварочный ток назначают: при
однопроходной сварке - в зависимости от толщины конструкции, а при
многопроходной - исходя из высоты шва. Высота шва (валика) при ручной
аргонодуговой сварке должна составлять 2-2,5 мм. Ориентировочно сварочный ток
выбирают из расчета 30-35 А на 1 мм диаметра вольфрамового электрода.
Напряжение на дуге должно быть минимально возможным,
что соответствует сварке короткой дугой.
Скорость сварки выбирают с учетом гарантированного проплавления
кромок и формирования требуемой выпуклости сварного шва.
Техника
сварки. При
выполнении первого (корневого) шва возможна сварка без присадочной проволоки,
но при этом все прихватки должны быть проплавлены. Нельзя сваривать без
присадочной проволоки конструкционные углеродистые стали марок 10 и 20, так как
в металле шва могут появиться поры. Сварку ведут углом вперед. Присадочную
проволоку подают навстречу движению горелки, причем угол между ними должен
составлять 90°. Следует избегать резких движений проволокой - они приведут к
разбрызгиванию присадочного металла или окислению конца проволоки.
Присадок должен всегда находиться в зоне защиты
аргоном.
Корневой шов сваривают без поперечных колебаний. При
наложении последующих слоев горелкой совершают колебательные движения,
амплитуда которых зависит от формы разделки кромок.
Кратер шва при отсутствии системы плавного снижения сварочного тока заваривают путем введения в кратер капли присадочного металла, одновременно плавно увеличивая дугу до ее естественного обрыва. Газовую защиту убирают, отводя горелку через 10-15 с после обрыва дуги.
Изучить: 1. Подготовка к выполнению сварочных работ.
2. Выбор параметров режима.
3. Техника
выполнения сварочных работ.
01.02.2022
группа: 412
Предмет: Техника и технология ручной дуговой сварки (наплавка, резка) неплавящимися электродами в защитном газе.
Тема урока: Приварка подкладного кольца к трубе аргонодуговой сваркой.
Аргонодуговая сварка труб
Дуговую сварку с защитой дуги инертным
газом (аргоном или гелием) применяют для производства тонкостенных труб (с
прямым швом) диаметром 15—426 мм и толщиной стенки 0,2—5 мм из
высоколегированных сталей аустенитного класса, а также из никеля и его сплавов,
магния, циркония и др. Наибольшее распространение такая сварка получила для
выпуска труб диаметром от 6 до 71 мм с толщиной стенки от 0,4 до 3,0 мм.
Существенным преимуществом метода
аргонодуговой сварки является возможность сварки труб из высоколегированных
сталей, а недостатком — сравнительно низкие скорости сварки: 0,5—1,5 м/мин.
В качестве исходной заготовки при этом
методе сварки труб применяют ленту в рулонах. Оборудование для подготовки и
формовки заготовки принципиально не отличается от описанного выше для сварки
труб сопротивлением и радиочастотной.
Аргонодуговая сварка труб может
производиться на тех же трубоэлектросварочных агрегатах, что и радиочастотная
сварка, и сварка сопротивлением. Заменяют лишь радиочастотный ламповый
генератор или сварочный трансформатор на соответствующее устройство для дуговой
сварки. При этом соответственно снижается и скорость привода установкой
специальных редукторов.
Рис. 187. Схема
аргонодуговой сварки прямошовных труб: 1 — смотровое окно; 2 — вольфрамовый
электрод; 3 — сварочная горелка; 4 — уплотняющая прокладка; 5 — свариваемая
труба; 6 — уплотнительное кольцо; 7 — полугерметичная камера; 8 —
приспособление для поддува газа; 9 — опорно-сварочные валки; 10 — верхняя
крышка камеры; 11 — баллон с газом
Схема аргонодуговой сварки прямошовных
труб показана на рис. 187. Трубная заготовка из формовочного стана поступает к
сварочному стану. Между кромками трубной заготовки и не плавящимся электродом
из вольфрама возбуждается электрическая дуга. Происходит расплавление кромок
заготовки. Обжимаясь в опорно-сварочных валках, кромки свариваются.
Применяемый внутренний поддув зоны сварки позволяет значительно уменьшить величину
внутреннего грата. Небольшая толщина стенки (1,5—3,0 мм) и необходимое
сварочное давление дают возможность вести процесс без применения присадочного
материала.
Применение аргона в качестве защитного
газа обеспечивает более устойчивое горение сварочной дуги, лучшую защиту
сварного соединения и меньшее провисание металла шва по сравнению с гелием, так
как потенциал ионизации гелия выше, а плотность меньше, чем у аргона. Поэтому
применение аргона для сварки труб из нержавеющей стали, титана и др. более
целесообразно. Аргон подается в камеру через сопло сварочной головки под
избыточным давлением 19,6—49 кн/м² (0,2—0,5 am). Внутрь трубы аргон подается
под избыточным давлением 29,2—98,1 кн/м² (0,3—1,0 ат).
При производстве труб диаметром до 100 мм
применяют вольфрамовый электрод одного диаметра, равный 4 мм. При аргонодуговой
сварке используют постоянный ток напряжением 12—15 в и силой 150—200 а (это
зависит от размера свариваемых труб). Для получения постоянного тока применяют
сварочный трансформатор и преобразователь постоянного тока. Расход аргона при
сварке со скоростью до 1 м/мин составляет 15—30 л/мин. На стане предусмотрена
регулировка электрода как по высоте, так и поперек оси сварки.
Особое внимание при аргонодуговой сварке
труб уделяют чистоте кромок. Кроме этого, при производстве труб из цветных
металлов (титан, ниобий и т. д.), а также из высоколегированных сталей особенно
следят за хорошей чистотой поверхности трубы. В связи с этим для уменьшения
налипания металла валки последних клетей формовочного стана иногда выполняют
составными. Участки валка, где имеется наибольшая вероятность налипания,
изготовляют из текстолита или пластмассы. Наружный грат на трубе,
образовавшийся после сварки, зачищают в потоке иглофрезой. После зачистки грата
и охлаждения трубу калибруют на калибровочном стане и разрезают на мерные длины
резцовым отрезным устройством.
При аргонодуговой сварке предел прочности
металла шва обычно на 10—20% выше, чем основного металла, а относительное
удлинение ниже на 10—30%.
Трубы, сваренные этим способом, в основном
предназначены для химической промышленности. Поэтому после сварки их подвергают
холодной прокатке и волочению, последующей термической обработке для полного
выравнивания свойств шва и основного металла. Это повышает коррозионную стойкость
шва.
Аргонодуговая сварка в сравнении с другими
известными способами сварки труб из легированных сталей имеет следующие
преимущества:
1.
полная защита металла и электрода от окисляющего воздействия кислорода
воздуха;
2.
возможность работы без специальных электродных покрытий, флюсов и
последующей очистки шва от флюсов и шлаков;
3.
устойчивость горения дуги, что облегчает осуществление непрерывного
процесса сварки;
4.
высокие механические свойства и коррозийная стойкость сварного шва, а также
хороший внешний вид;
5.
безопасность напряжения сварочного тока как при холостом ходе, так и при
горении дуги.
2. Применение аргона в качестве защитного газа.
3. Преимущества аргонодуговой сварки.
9.09.2021
МДК 01.01 Основы технологии сварки и сварочного оборудования
Тема: Тепловое действия дуги. Нагрев изделия и коэффициент полезного действия.
Тепло которое передается от дуги к сварному изделию называют эффективной тепловой мощностью, которая рассчитывается по формуле: qеф=0,24×Iсв×Uд×ηе. ηе — эффективный коэффициент полезного действия нагревания изделия дугой. Погонная энергия сварочной дуги.
Энергия мощных потоков заряженных частиц, бомбардирующих катод и анод, превращается в тепловую энергию электрической дуги. Суммарное количество теплоты Q (Дж), выделяе
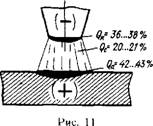
Мое дугой на катоде QK, аноде QB и в столбе дуги Qc, определяется по формуле
Q = / Uat,
Где / — сварочный ток, А; £/д — напряжение дуги, В; t — время горения дуги, с.
При питании дуги постоянным током (рис. 11) наибольшее количество теплоты выделяется в зоне анода. Это объясняется тем, что анод подвергается более мощной бомбардировке заряженными частицами, чем катод, а при столкновении частиц в столбе дуги выделяется меньшая доля общего количества теплоты.
При сварке угольным электродом температура в катодной зоне достигает 3200° С, в анодной — 3900°С, а в столбе дуги среднее значение температуры составляет 6000° С. При сварке металлическим электродом температура катодной зоны составляет около 2400° С, а анодной зоны — 2600° С.
Разная темп-ература катодной и анодной зон и разное количество теплоты, выделяющейся в этих зонах, используются при решении технологических задач. При сварке деталей, требующих большого подвода теплоты для прогрева кромок, применяют прямую полярность, при которой анод (плюсовая клемма источника тока) подсоединяют к детали, а катод (минусовая клемма источника тока) — к электроду. При сварке тонкостенных изделий, тонколистовых конструкций, а также сталей, не допускающих перегрева (нержавеющие, жаропрочные, высокоуглеродистые и др.), применяют сварку постоянным током обратной полярности. В этом случае катод подсоединяют к свариваемой детали, а анод — к электроду. При этом не только обеспечивается меньший нагрев свариваемой детали, но и ускоряется процесс расплавления электродного материала за счет более высокой температуры анодной зоны и большего подвода теплоты. Полярность клемм источника постоянного тока определяют с помощью раствора поваренной соли (половина чайной ложки соли на стакан воды). Если в такой раствор опустить провода от клемм источника тока, то у отрицательного провода будет происходить бурное выделение пузырьков водорода.
При питании дуги переменным током различие температур катодной и анодной зон и распределение теплоты сглаживаются вследствие периодической смены катодного и анодного пятна с частотой, равной частоте тока.
Практика показывает, что в среднем при ручной сварке только 60...70% теплоты дуги используется на нагревание и плавление металла. Остальная часть теплоты рассеивается в окружающую среду через излучение и конвекцию.
Количество теплоты, используемое на нагрев и плавку свариваемого металла в единицу времени, называется Эффективной тепловой мощностью дуги Q3 (Дж). Она равна полной тепловой мощности дуги, умноженной на эффективный коэффициент полезного действия г] нагрева металла дугой:
Q3 = / t/дТ)-
Величина г] зависит от способа сварки, материала электрода, состава электродного покрытия и других факторов. При ручной дуговой сварке электродом с тонким покрытием или угольным электродом г] составляет 0,5...0,6, а при качественных электродах — 0,7...0,85. При аргонодуговой сварке потери теплоты значительны (г) = 0,5...0,6). Наиболее. полно используется теплота при сварке под флюсом (т| = 0,85...0,93).
Для характеристики теплового режима процесса сварки принято определять погонную энергию дуги, т. е. количество теплоты, вводимое в металл на единицу длины однопроходного шва, измеряемое в Дж/м. Погонная энергия Qn равна отношению эффективной тепловой мощности Q3 К скорости сварки v:
Qn = Q3/v = / U^/v.
Потери теплоты при ручной дуговой сварке составляют примерно 25%, из которых 20% уходят в окружающую среду через излучение и конвекцию паров и газов, а 5% — на угар и разбрызгивание свариваемого металла. При автоматической сварке под флюсом потери составляют только 17%, из которых 16% расходуются на плавление флюса и 1 % на угар и разбрызгивание.
8.09.2021
МДК 01.01 Основы технологии сварки и сварочного оборудования Тема:Сварочная дуга: определение,физическая сущность, виды устойчивого горения.
Существует несколько видов электрического разряда:
- Тлеющий разряд. Возникает в низком давлении, применяется в люминесцентных лампах и плазменных экранах;
- Искровой разряд. Возникает, когда давление равно атмосферному, отличается прерывистой формой. Искровому разряду соответствует молния, также применяется для зажигания двигателей внутреннего сгорания;
- Дуговой разряд. Применяет при сварке и для освещения. Отличается непрерывистой формой, возникает при атмосферном давлении;
- Коронный. Возникает, когда тело электрода шероховато и неоднородно, второй электрод может отсутствовать, то есть возникает струя. Применяется для очистки газов от пыли;
Природа и строение
Природа сварочной дуги не так уж и сложна, как может показаться на первый взгляд. Электрический ток, проходя через катод, затем проникает в ионизированный газ, происходит разряд с ярким свечением и очень высокой температурой, поэтому температура электрической дуги может достигать 7000 – 10000 градусов. После этого ток перетекает на обрабатываемый свариваемый материал. Так как температура настолько высока дуга выделяет вредное для человеческого организма ультрафиолетовое и инфракрасное излучения, оно может навредить глазам или оставить световые ожоги на коже, поэтому при проведении сварочного процесса необходима надлежащая защита.
Разновидности
Виды сварочной дуги отличаются схемой подвода сварочного тока и средой, в которой они возникают, наиболее распространенными вариантами являются:
- Прямое действие. При таком способе сварочный располагается параллельно свариваемой металлической конструкции и дуга возникает под углом девяносто градусов по отношению к электроду и металлу;
- Сварочная дуга косвенного действия. Возникает, когда используется два электрода, которые располагаются под углом 40-60 градусов к поверхности свариваемой детали, дуга возникает между электродами и сваривает металл;
Также существует классификация в зависимости от атмосферы, в которой они возникают:
- Открытый тип. Дуга данного типа горит на воздухе и вокруг нее образовывается газовая фаза, содержащая пары свариваемого материала, электродов и их покрытий;
- Закрытый тип. Горение такой дуги происходит под слоем флюса, в газовую фазу, образовавшуюся вокруг дуги входят пары металла, электрода и флюса;
- Дуга с подачей газов. В горящую дугу подаются сжатые газы – гелий, аргон, углекислый газ, водород и другие различные смеси газов, подаются они для того, чтобы не окислялся свариваемый металл, их подача способствует восстановительной или нейтральной среде. В газовую фазу вокруг дуги входят – подающийся газ, пары металла и электрода;
Также различают по длительности действия – стационарная (для долгого применения) и импульсная (для однократного), по материалу используемого электрода – угольные, вольфрамовые – неплавящиеся электроды и металлические – плавящиеся. Самый распространенный плавящийся электрод – стальной. На сегодняшний день наиболее часто применяется сварка с неплавящимся электродом. Таким образом, виды сварочных дуг разнообразны.
Условия горения
При стандартных условиях, то есть температуре в 25 градусов и давлении в 1 атмосферу газы не способны проводить электрический ток. Для того, чтобы образовалась дуга необходимо, чтобы газы между электродами были ионизированы, то есть имели в своем составе различные заряженные частицы – электроны или ионы (катионы или анионы). Процесс образования ионизированного газа будет называться ионизацией, а работа, которую необходимо затратить на отрыв электрона у атомной частицы для образования электрона и иона – работой ионизации, которая измеряется в электрон-вольтах и называется потенциалом ионизации. Какую именно энергию необходимо затратить для отрыва электрона от атома зависит от природы газовой фазы, значения могут быть от 3,5 до 25 эВ. Самый маленький потенциал ионизации имеют металлы щелочной и щелочно-земельной группы – калий, кальций и, соответственно, их химический соединения. Такими соединениями покрывают электроды, для того, чтобы они способствовали устойчивому существованию и горению сварочной дуги.
Также для возникновения и горения дуги необходима постоянная температура на катод, которая зависит от природы катода, его диаметра, размера и температуры окружающей среды. Температура электрической дуги поэтому должна быть постоянной и не колебаться, благодаря огромным значениям силы тока температура может достигать 7 тысяч градусов, таким образом, сваркой можно присоединять абсолютно все материалы. Постоянная температура обеспечивается с помощью исправного источника питания, поэтому его выбор при конструировании сварочного аппарата очень важен, он оказывает влияние на свойства дуги.
Возникновение
Она возникает при быстром замыкании, то есть когда электрод соприкасается с поверхность свариваемого материала, из-за колоссальной температуры поверхность материала расплавляется, а между электродом и поверхность образуется небольшая полоса из расплавившегося материала. К моменту расхождения электрода и свариваемого материала образуется шейка из материала, которая моментально разрывается и испаряется из-за высокого значений плотности тока. Газ ионизируется и возникает электрическая дуга. Возбудить ее можно с помощью касания или чирканья.
Особенности
Она имеет следующие особенности по сравнению с другими электрическими зарядами:
- Высокая плотность тока, которая достигает нескольких тысяч ампер на квадратный сантиметр, благодаря чему достигается очень высокая температура;
- Неравномерность распределения электрического поля в пространстве между электродами. Вблизи электродов падение напряжения очень велико, когда в столбе – наоборот;
- Огромная температура, которая достигает самых больших значений в столбе из-за высокой плотности тока. При увеличении длины столба температура уменьшается, а при сужении – наоборот увеличивается;
- С помощью сварочных дуг можно получать самые различные вольт-амперные характеристики – зависимости падения напряжения от плотности тока при постоянной длине, то есть установившемся горении. На данный момент существует три вольтамперные характеристики.
Первая – падающая, когда при увеличении силы и ,соответственно, плотности тока, напряжение падает. Вторая- жесткая, когда изменение силы тока никак не влияет на значение величины напряжения итретья – возрастающая, когда при увеличении силы тока напряжение также увеличивается.
Таким образом, сварочную дугу можно назвать самым лучшим и надежным способом скрепления металлических конструкций. Сварочный процесс оказывает большое влияние на сегодняшнюю промышленность, потому что только высокая температура сварочной дуги способна скреплять большинство металлов. Для получения качественных и надежных швов необходимо правильно и верно учитывать все характеристики дуги, следить за всеми значениями, благодаря этому процедура пройдет быстро и наиболее эффективно. Также необходимо учитывать свойства дуги: плотность тока, температуру и напряжение.
Выполнить практическое задание
На формате А4 выполнить сборочный чертеж сварного изделия
Сделать вывод от проделанной работы.
Рисунок 1 Образец готовой работы
6.09.2021
Тема: Сварные соединения: определение,основные виды их достоинства и недостатки.Сварные швы
Достоинства сварных соединений:• Возможность получения изделий больших размеров (корпуса судов и летательных аппаратов, железнодорожные вагоны, кузова автомобилей, трубопроводы, резервуары, фермы, мосты и др.). • Снижение массы по сравнению с литыми деталями до 30…50%, с клепанными – до 20%. Этого достигают благодаря в основном снижению толщин стенок и припусков на механическую обработку, а также отсутствию ослаб-ляющих отверстий и накладок при наклепе. • Снижение стоимости изготовления сложных деталей в условиях единичного и мелкосерийного производства. • Малая трудоемкость, невысокая стоимость оборудования, возможность автоматизации.
Недостатки сварных соединений:• Вероятность возникновения при сварке плавлением различных дефектов швов, снижающих прочность соединения при переменных нагрузках. • Низкая прочность швов при электроконтактной сварке вследствие неправильного выбора параметров техно-логического процесса. • Необходимость проведения для всех сварных швов визуального контроля, а для сварных изделий ответственного назначения неразрушающего инструментального или выборочно разрушающего контроля. • Возникновение остаточных напряжений (вследствие термических деформаций от неравномерного нагрева) снижает прочность и вызывает необходимость проведения в ряде случаев механической обработки после старения (изменение свойств металла во времени вследствие внутренних процессов). • Местный нагрев вызывает в зоне термического влияния вблизи шва изменение механических свойств метал-ла.
По технологии изготовления различают: 1) электродуговая (нагрев происходит пропусканием электрического тока между электродом и материалом ,материал участвует в образовании шва, материал электрода защищает шов от окисления) 2) автоматическая (под слоем флюса, для деталей большой длины) 3) газовая (в углекислом газе, для сваривания деталей из углеродистых и низколегированных сталей, в среде аргона и гелия для высоко легированных сталей плавящимся или вольфрамовым электродом) 4) электрошлаковая (для сварки деталей неограниченной толщины) 5) сварка электронным лучом (в вакуумных камерах, диффузионная сварка легированных сталей, алюминиевых сплавов, неметаллов) 6) контактная сварка.
Тип сварного соединения определяет взаимное расположение свариваемых элементов. Различают: стыковые, угловые, тавровые, нахлесточные и торцовые сварные соединения.
Стыковое соединение- сварное соединение двух элементов, примыкающих друг к другу торцовыми поверхностями и расположенных в одной плоскости или на одной поверхности (рис. 1.2). Поверхности элементов могут быть несколько смещены при соединении листов разной толщины (см. рис. 1.2, б).
Рис. 1.2. Стыковые соединения
Угловое соединение- сварное соединение двух элементов, расположенных под углом и сваренных в месте примыкания их краев (рис. 1.3).
Рис. 1.3. Угловые соединения
Тавровое соединение- сварное соединение, в котором торец одного элемента примыкает под углом и приварен к боковой поверхности другого элемента (рис. 1.4).
Рис. 1.4. Тавровые соединения
Нахлесточное соединение- сварное соединение, в котором сваренные элементы расположены параллельно и частично перекрывают друг друга (рис. 1.5, а, б). Отсутствие опасности прожогов при сварке облегчает применение высокопроизводительных режимов сварки. Применение нахлесточных соединений облегчает сборку и сварку швов, выполняемых при монтаже конструкций (монтажных швов).
Сварка представляет собой способ соединения деталей в неразъемную конструкцию. При этом остается след - сварной шов. Он выглядит по-разному в зависимости от многих факторов - материала деталей, способа сварки, примененного оборудования. Соединение деталей, осуществленное сваркой, называется сварочное соединение. Несмотря на то, что сварные соединения и швы относятся к одному производственному процессу, не следует смешивать эти понятия. Соединение - это неразъемная конструкция из двух металлических деталей, а сварочный шов - это след, оставленный после соединения.
К шву и соединению предъявляются конкретные требования, закрепленные в нормативных документах. Сварщик и руководитель сварочных работ обязаны иметь четкое представление, что такое сварной шов, как он должен выглядеть и каким требованиям удовлетворять.
Элементы конструкции шва
Конструктивные элементы сварного шва определены ГОСТом 2601. Нормативные документы дают определение, что такое сварочный шов, его геометрические параметры, перечисляют имеющиеся типы сварочных швов.
К таким элементам относятся форма и размер кромок после их подготовки.
Классификация сварочных швов
Имеются многочисленные типы и виды сварных соединений и сварных швов. Это вызвало потребность в их четкой классификации. Она разработана в зависимости от многих факторов. Классификация учитывает технологические особенности швов, их пространственное положение, размеры. Достоинством такого дифференцирования является применение обозначений на каждый тип сварного шва.
Существует много различных позиций, по которым имеется классификация, включающая существующие виды сварки и типы сварных соединений.
Положение шва в пространстве
Немаловажную роль играет расположение шва в пространстве.
Нижнее положение является самым выигрышным. Шов при этом получается прочным и надежным. При верхнем, который иначе называют потолочном, положении, сварщику приходится принимать неестественную позу. Долго сохранять ее весьма трудно. А ведь одним из условий получения качественного шва является непрерывность процесса.
Для повышения точности следует использовать короткую дугу, а ширину шва делать не превышающей диаметр электрода. Для выполнения потолочного шва требуется не только получение профильного образования, но и приобретение практических навыков при более благоприятных условиях.
При выполнении швов во всех положениях существует проблема стекания вниз расплавленного металла. Нижнее положение при этом является самым выигрышном. Потолочное и нижнее положения относятся к горизонтальным. Стекание металла, являющееся чрезмерным, уменьшают, снизив температуру нагрева. Это можно сделать, увеличив скорость передвижения электрода, или регулярно прерывать дугу, давая возможность остыть металлу.
Вертикальный шов часто встречается в конструкциях, но самым простым вариантом не является. Если шов расположен вертикально, то вниз устремляться будет не сварочная ванна целиком, а только отдельные капельки. Если сварка осуществляется по направлению сверху вниз, то эти капельки начнут быстро застывать, образуя своеобразную преграду. Поэтому вести сварку при вертикальном способе следует снизу вверх. Свариваемые детали при вертикальном положении должны быть надежно зафиксированы.
Протяженность шва
Сварочные швы и соединения разделяются по их протяженности. По этому признаку шов бывает сплошным и прерывистым. При выполнении прерывистого шва в нем предусмотрены определенные интервалы, имеющие постоянный размер. Сварные швы прерывистого характера бывают различными. Они так же, как непрерывные, могут быть односторонними и двусторонними.
Такая градация отражается на обозначении шва в чертежах. При этом вводится такое понятие, как шаг шва.
Форма поверхности
Виды сварных швов разделяются по форме, которая имеет их наружная поверхность.
Каждый вид имеет свои преимущества. Играет роль, какую нагрузку выдерживает сварной шов. Когда предстоят статические нагрузки, то целесообразно применять выпуклый шов. Он имеет несколько слоев, что ведет к дополнительному расходу электродов и удорожанию сварочного процесса.
Если предстоит сварка тонких металлических листов, то лучше применять вогнутую форму. Если сварное изделие при эксплуатации будет подвергаться динамическим нагрузкам, то следует выполнять плоские швы или вогнутой формы. Такой выбор объясняется тем, что не будет большого перепада между поверхностями шва и основного материала.
Соединения
Сварные соединения разделяются на различные виды.
Виды сварных соединений:
- Стыковые. Детали располагаются в одной и той же плоскости.
- Угловые. Детали, подлежащие соединению, располагают под необходимым углом. Наиболее распространенным является прямой угол.
- Тавровые. Торец одной детали располагают перпендикулярно или под небольшим углом по отношению к основной поверхности второй детали.
- Нахлесточные. Положение деталей в пространстве - параллельное. При этом одна деталь частично налегает на другую.
- Торцевые. Воедино сваривают два торца элементов.
Сварной стыковой шов применяется для сварки трубопроводов, различных труб и металлических листов. Сварке подлежат торцовые поверхности. Сварка встык требует проведение подготовительных работ, которые заключаются в тщательной подгонке торцевых поверхностей друг к другу. Для обеспечения точности может применяться предварительный подварочный шов. Сварку встык можно осуществлять как на весу, так и на подкладке - стальной или медной. При стыковых соединениях возможны различные виды скосов кромок или сварка без них.
К преимуществам такого способа относится уменьшенный расход вспомогательного материала, в частности, электродов. Одинаковая толщина элементов не является обязательным требованием. Но при этом электрод следует направлять к более толстой детали. Это обеспечит ее более сильный нагрев, а тонкую деталь убережет от прожогов.
Угловые швы находят применение для соединения частей различных емкостей и резервуаров. Для получения качественного углового соединения рекомендуется установка деталей "лодочкой".
1.09.2021
Тема: Сварка давлением: сущность,основные виды, их особенности
В России и за рубежом получили широкое развитие разнообразные способы сварки в твердой фазе: термокомпрессионная, диффузионная, трением, ультразвуковая, клинопрессовая, индукционная, холодная, взрывом, магнитно-импульсная и др. Этому способствовали, с одной стороны, разработка теоретических основ сварки в твердой фазе (1965—1972 гг.) и, с другой стороны, быстрый прогресс электронной техники, точного приборостроения и средств автоматизации.
Способами сварки в твердой фазе (рис. 1) можно соединять практически любые металлические сплавы в однородном и разнородном сочетаниях, металлы с полупроводниками и керамиками, пластмассы и т. д. Чем выше степень локализации пластической деформации в зоне соединения, тем эффективнее способы сварки в твердой фазе обеспечивают точность размеров изделий, сохранение механических и специальных свойств свариваемых материалов и тем легче они позволяют соединять хрупкие материалы, особенно в разнородных сочетаниях.
При любых способах сварки в твердом состоянии соединение образуется в результате деформационного или термодеформационного воздействия на соединяемые материалы в зоне контакта. Независимо от характера и интенсивности этого воздействия природа образования соединения едина. Различия заключаются в кинетике протекания Отдельных стадий процесса, которая определяется условиями нагрева, характером и интенсивностью деформации материалов, степенью локализации деформации и особенностями развития релаксационных процессов в приконтактной зоне.
С позиций теории твердофазных топохимических реакций процесс образования соединения при всех способах сварки в твердой фазе протекает в три основные стадии.
1. Образование физического контакта, т. е. сближение атомов соединяемых материалов на расстояние, при котором возникает физическое взаимодействие (обусловленное дисперсионными силами типа Ван-дер-Ваальса), или расстояние, при котором возможно слабое химическое взаимодействие. Это осуществляется за счет пластической деформации обоих (при соединении одноименных или близких по сопротивляемости пластическому деформированию) или более мягкого из соединяемых материалов. Расчеты кинетики стадии образования физического контакта разработаны для процессов сварки с низкоинтенсивным силовым воздействием типа термокомпрессионной и диффузионной, для которых эта стадия достаточно продолжительна. Эти расчеты основаны на анализе смятия микровыступов на поверхностях соединяемых материалов за счет ползучести с учетом степени чистоты механической обработки поверхностей и изменения истинного напряжения по мере деформации микровыступов.
2. Активация контактных поверхностей (образование активных центров). При сварке одноименных материалов активация контактных поверхностей происходит одновременно с образованием физического контакта в процессе их сближения при смятии отдельных микровыступов за счет пластической деформации. При сварке разноименных материалов на этой стадии для образования соединения необходимо дополнительное время для образования активных центров на поверхности более твердою из соединяемых материалов.
Теория активных центров предусматривает, с одной стороны, дискретность процесса образования очагов взаимодействия (активных центров), а с другой стороны, коллективность взаимодействия атомов в поле активных центров.
В общем случае активными центрами или очагами взаимодействия являются поля упругих искажений кристаллической решетки, образующиеся на поверхностях соединяемых материалов в процессе упругопластической деформации. Однако для образования активных центров совсем не обязательно, чтобы приповерхностные слои обеих соединяемых поверхностей подвергались пластической деформации. Например, при соединении разнородных материалов с резко различной сопротивляемостью пластической деформации, таких как алюминий и кремний, в условиях термокомпрессионной и ультразвуковой сварки поверхность кремния при определенных параметрах режима не имеет следов пластической деформации в виде дислокаций и полос скольжения. В этом случае активными центрами на кремнии являются чисто упругие искажения, возникающие либо вследствие царапания деформационными микровыступами алюминия, либо в результате воздействия ультразвукового поля. При сварке одноименных металлов и сплавов, а также разнородных материалов с не слишком большой разницей в механических свойствах активные центры образуются, как правило, в местах ьыхода дислокаций и их скоплений в зону контакта. Исследования экзоэлектронной эмиссии с поверхности твердых тел в процессе их пластической деформации показывают, что интенсивность эмиссии электронов в существенной мере зависит не только от уровня микронапряжений в поле упругих искажений, но и от плотности потока вакансий, для которых места выхода дислокаций служат интенсивными стоками. Это подтверждает мнение о значительной роли точечных дефектов в процессе активации контактных поверхностей при сварке в твердой фазе, особенно на релаксационной стадии взаимодействия.
Поверхности твердых тел в атмосферных условиях, как правило, инертны, так как валентности их атомов насыщены связью с атомами окружающей среды. Даже в отсутствие окисных пленок, например, в условиях диффузионной сварки в вакууме, когда они у большинства металлов диссоциируют или растворяются, на поверхностях имеется хемосорбированный слой. Несмотря на ионную природу, связь между адсорбированным кислородом и атомами металла на его поверхности сильнее связи кислорода с металлом в окисле того же стехиометрического состава. Так как величина теплоты адсорбции в большинстве случаев выше теплоты образования окисла, связь металл—кислород в комплексе хемосорбции энергетически более стабильна, чем связь металл—кислород в окисле. Это различие в стабильности оказывается решающим при оценке роли активных центров в процессе образования соединения при сварке в твердом состоянии. Даже при разрушении твердых тел в глубоком вакууме комплексы хемосорбции образуются за весьма короткое время вследствие сегрегации примесных атомов на поверхности путем диффузии из прилегающих объемов тела. В этом смысле понятие ювенильных поверхностей весьма условно. Акт активации поверхностных атомов можно представить как процесс разрыва насыщенных связей, приводящий к появлению неспаренных электронов (радикалов), способных участвовать в химическом взаимодействии.
Следовательно, для развития в зоне контакта соединяемых материалов процессов электронного взаимодействия требуется определенная величина энергии для активации поверхностей. Такая энергия может сообщаться в виде теплоты (термическая активация), упругопластической деформации (механическая активация), электронного, ионного и других видов облучения (радиационная активация). При сварке металлов с металлоидами химическими соединениями металлов, в частности окислами, а также с полупроводниками или интерметаллидами, обладающими полупроводниковыми свойствами, квантовые процессы сводятся к образованию прочных связей в основном ковалентного типа. Когда соединяемые вещества обладают способностью к донорно-экцепторному взаимодействию, устанавливается координационно-ковалентная связь. Примерами таких веществ могут служить основные окислы (доноры) и кислые окислы (акцепторы). При непосредственном соединении металлов с керамиками, в состав которых входят кислые окислы, координационно-ковалентная связь наиболее легко образуется в том случае, если на поверхности металла создан тонкий слой низших основных окислов, обладающих ярко выраженными донорными свойствами. Координационно-ковалентная связь не является единственным типом связи, обусловливающей образование прочного соединения металла с другими веществами. Возможно также образование парноэлектронной связи вследствие переключения (трансляции) валентных связей.
Длительность стадии активации принято оценивать на основе термофлуктуационных уравнений теории абсолютных скоростей реакций, учитывающих вклад в энергию активации процесса не только температуры, но и напряжений [28,9].
3. Объемное взаимодействие. Эта стадия наступает с момента образования активных центров на соединяемых поверхностях. В течение этой стадии происходит развитие взаимодействия соединяемых материалов на активных центрах как в плоскости контакта с образованием прочных химических связей, так и в объеме зоны контакта. В плоскости контакта этот процесс заканчивается слиянием дискретных очагов взаимодействия, а в объеме — релаксацией напряжений (в той степени, которая необходима для сохранения образовавшихся связей). Однако для обеспечения требуемой прочности соединения в целом часто необходимо дальнейшее развитие релаксационных процессов типа рекристаллизации или гетеродиффузии в допустимых пределах. При сварке одноименных металлов критерием окончания третьей стадии и образования качественного соединения может служить длительность, необходимая для образования общих зерен в зоне контакта за счет собирательной рекристаллизации или рекристаллизации обработки. При сварке разноименных материалов необходимость развития или ограничения гетеродиффузии определяется физико-химическими свойствами диффузионной зоны и образующихся в ней фаз.
Таким образом, при всех способах сварки в твердой фазе пластическая деформация является основным процессом, определяющим развитие первых двух стадий образования соединения — физического контакта и активации контактных поверхностей, причем длительность процесса образования прочных связей по всей площади взаимодействия определяется частотой выхода дислокации в зону физического контакта, т. е. не только необходимой для этого величиной накопленной деформации, но и ее скоростью.
Степень развития третьей стадии процесса (релаксация напряжений, рекристаллизация, гетеродиффузия) определяется главным образом температурой в зоне соединения, однако накопленная пластическая деформация и ее скорость могут также оказывать существенное влияние на интенсивность протекания релаксационных процессов и определять их механизм. Например, при сварке однородных металлов в режимах интенсивной пластической деформации при относительно невысоких температурах образование общих зерен в зоне соединения может происходить и по механизму рекристаллизации обработки, а при малоинтенсивной деформации и высоких температурах — только по механизму собирательной рекристаллизации. Скорость пластической деформации может менять механизм гетеродиффузии. Например в работе [4] было показано, что при ударной сварке разнородных металлов в твердом состоянии в вакууме со скоростью соударения порядка десятков метров в секунду скорости гетеродиффузии могут быть даже выше, чем в жидком состоянии, что было объяснено образованием высоких неравновесных концентраций дислоцированных атомов. Обычными механизмами диффузии по вакансиям этот факт объяснить нельзя. По своей физико-химической природе схватывание поверхностей твердых тел в условиях глубокого вакуума является частным случаем процесса образования соединения материалов при сварке в твердой фазе. В связи с определяющей ролью пластической деформации в процессе образования соединения (схватывания) металлов в твердом состоянии представляет особый интерес рассмотрение возможных причин активирующего влияния глубокого вакуума (наряду с температурой и приложенным давлением) как одного из факторов, облегчающих пластическую деформацию в металлах и ослабляющего прочность связей в окислах и химически адсорбированных слоях, существующих на соединяемых поверхностях. К этим причинам следует отнести резкое снижение температуры диссоциации и испарения окислов (для большинства металлов, за исключением алюминия, магния, тория и т. п., это происходит уже при вакууме около 10-8 мм рт. ст.); десорбцию примесей внедрения; изменение величины поверхностной энергии. Все это значительно облегчает условия гетерогенного зарождения дислокаций вблизи поверхности (снижение критического сопротивления сдвигу и энергии образования и движения дислокаций) и их выхода к поверхности (снижение сил зеркального изображения). В результате этого с увеличением степени вакуума температура и давление, необходимые для схватывания, значительно снижаются. Особого внимания заслуживает анализ влияния дегазации металла, так как снижение концентрации примесей внедрения существенно, но неодинаково интенсифицирует пластическую деформацию при известных ее механизмах (поперечное скольжение, пороговая ползучесть, непороговая или диффузионная ползучесть). В частности, вследствие десорбции газовых примесей и периодической блокировки ими дислокаций и последующей деблокировки наблюдается ступенчатое развитие деформации ползучести в зоне контакта [30].
С изложенных выше позиций теории трехстадийности процесса соединения легко объяснить наблюдаемые экспериментальные факты и явления. В частности, при сварке с высокоинтенсивным силовым воздействием (сварка взрывом, магнитно-импульсная сварка, холодная сварка и др.), ввиду того, что скорость и величина пластической деформации соединяемых материалов в приконтактной зоне велики, атомы в состоянии физического контакта вступают уже энергетически подготовленными для образования химических связей.
При магнитно-импульсной сварке и сварке взрывом в ряде случаев даже необходимо ограничивать величину и скорость пластической деформации в приконтактной зоне, так как образуются оплавленные участки металла. Возможность образования соединения и его прочность при сварке с высокоинтенсивным силовым воздействием часто определяются условиями релаксации напряжений в приконтактной зоне. При сварке с низкоинтенсивным силовым воздействием (диффузионная сварка, сварка давлением с подогревом, термокомпрессионная сварка) скорость пластической деформации материала мала, и для получения качественного соединения требуются десятки минут. В этом случае пластическую деформацию, наоборот, необходимо интенсифицировать, чтобы сделать процесс более производительным. Кинетический подход к анализу процесса образования соединения материалов в твердой фазе позволил наметить пути интенсификации способов сварки с низкоинтенсивным силовым воздействием и, наоборот, так ограничивать параметры импульсных способов сварки, чтобы не происходило образования оплавленных участков металла в зоне контакта. Эти пути дальнейшего совершенствования технологии сварки сочетаются с новыми подходами к разработке высокопроизводительного сварочного оборудования.
Сопоставление кинетики развития пластической деформации соединяемых материалов с кинетикой роста прочности соединений, полученных при сварке металлов различной природы в одноименном и разноименном сочетаниях, показывает, что наиболее интенсивный рост прочности соединения происходит за период активного деформирования и этап неустановившейся ползучести. На этапе установившейся ползучести интенсивность процессов развития физического контакта и образования химических (металлических) связей снижается в соответствии с уменьшением скорости деформации. Следовательно, если в процессе образования соединения любым способом инициировать интенсивную пластическую деформацию соединяемых материалов, то должен наблюдаться и интенсивный рост прочности соединения. При сварке давлением с подогревом с ограниченной пластической деформацией, т. е. в условиях диффузионной сварки, интенсифицировать развитие деформации соединяемых материалов можно путем скачкообразного увеличения температуры или давления или путем импульсного воздействия давления.
Одним из наиболее существенных недостатков сварки давлением с подогревом, например диффузионной, является длительность процесса, обусловленная медленным развитием деформации по схеме ползучести вследствие интенсивного развития деформационного упрочнения металла в приконтактном объеме. В связи с этим перспективным является новый способ сварки с циклическим приложением давления, позволяющий использовать наиболее эффективные стадии развития пластической деформации (стадии активной деформации и неустановившейся ползучести). Эффект циклического воздействия сварочного давления при высокой температуре (>= 0,5 Tпл, см. рис. 1) обусловлен тем, что в течение разгрузки и паузы интенсивно протекают процессы возврата, т. е. устраняются барьеры, препятствующие дальнейшему развитию пластической деформации в приконтактном объеме. Каждое последующее нагружение вновь инициирует активную пластическую деформацию. При этом появляется возможность существенного снижения температуры процесса, что способствует повышению свойств соединения как за счет наиболее совершенной тонкой структуры металла, так и за счет ограничения возможности образования промежуточных хрупких фаз.
Другим, также перспективным способом интенсификации процесса сварки давлением с подогревом является циклическое повышение температуры сварки, способствующее ускорению процесса возврата и рекристаллизации.
Широкие возможности для сварки металлов в твердой фазе открывает использование явления сверхпластичности. При этом сварку металлов, претерпевающих фазовые превращения (например, титана, железа, циркония или их сплавов), осуществляют в области температур фазовых превращений и при скоростях деформации 10-3—10-4 c-1, обеспечивающих сверхпластичность. Сварку сплавов с гетерофазной структурой ведут при скоростях деформации этого порядка при соответствующих температурах. Сверхпластичность позволяет снизить в несколько раз, а иногда на порядок, требуемые усилия и особенно резко длительность процесса сварки (на два порядка) [16].
Для некоторых конструкций и широкого класса однородных и разнородных материалов (металлы с металлами, с полупроводниками и керамикой, керамика с керамикой и т. д.) перспективно использовать промежуточные прокладки из материалов, обладающих высокими и сверхпластичными свойствами при выбранных режимах сварки. Здесь эффект достигается за счет локализации пластической деформации и интенсификации сил контактного трения. Кроме того, эти прокладки могут служить в качестве барьерных слоев, предупреждающих неблагоприятный характер физико-химического взаимодействия соединяемых материалов. Существенному снижению температуры и давления при сварке способствует помещение в зону контакта тонкодисперсных активных порошков металлов благодаря их высокой поверхностной энергии. При известных r настоящее время способах сварки давлением с подогревом для упрочнения сварного соединения необходимо проведение последующей термической или термопластической обработки. Однако рациональное ведение сварки с резким увеличением скорости деформации на конечном этапе процесса до значений, при которых происходит эффективное скоростное деформационное упрочнение, позволяет непосредственно в процессе сварки осуществлять субструктурное упрочнение и обеспечивать высокий уровень сопротивляемости хрупкому разрушению сварных соединений.
Для соединения в твердой фазе труднодеформируемых хрупких материалов процесс сварки давлением целесообразно осуществлять по схеме гидроэкструзии, т. е. в условиях воздействия на свариваемые материалы всестороннего сжатия, достаточного по своей величине для перевода соединяемых материалов в пластическое состояние.
Существующие стандартные установки для сварки в твердой фазе давлением с подогревом имеют системы создания сварочного давления, которые не учитывают скоростного фактора приложения нагрузки. В них скорость нагружения устанавливается независимо от релаксационных характеристик свариваемого материала и целиком определяется характеристикой только механизма нагружения. Однако на процесс соединения в твердой фазе основное влияние оказывают величина сопротивления деформации свариваемых материалов и их релаксационные свойства, определяющие интенсивность процессов возврата. Поэтому установки для сварки в твердой фазе давлением с подогревом должны содержать узлы, обеспечивающие установление и автоматическое регулирование параметров процесса в зависимости от сопротивления пластической деформации и релаксационных свойств соединяемых материалов. Уже созданы опытные образцы установок, которые снабжены высокоточными системами измерения сопротивления и степени пластической деформации свариваемых деталей, и главное — механизмами создания сварочного давления, регулирующими в процессе сварки в широком диапазоне либо скорость нагружения при циклическом приложении нагрузки, либо скорость вынужденной деформации в соответствии с релаксационными характеристиками свариваемых материалов. На этих установках, в частности, можно осуществлять сварку в режиме сверхпластичности, а также формировать механические свойства сварных соединений на основе новейших достижений термомеханической обработки.
Для термокомпрессионной и ультразвуковой сварки в микроэлектронике разработаны соответствующие установки с программированным нагружением и автоматическим контролем качества сварных соединений. В последние годы для изготовления алюминиево-стальных трубных переходников широко используется клинопрессовый (теплопрессовый) способ сварки. Этот способ сварки заключается в нагреве соединяемых деталей на воздухе или в защитной среде и последующем впрессовывании стальной детали в алюминиевую. При этом рабочая часть стальной детали, как правило, затачивается на некоторый угол. Последующей механической обработкой сварных заготовок получают алюминиево-стальные переходники разнообразной формы и размеров. Такие переходники позволяют широко внедрять в конструкциях летательных аппаратов легкие алюминиевые трубопроводы, так как они обладают всеми преимуществами как алюминиевых, так и стальных конструкций (высокая удельная прочность стали и коррозионная стойкость сплавов алюминия и возможность осуществления сварки и многоразового монтажа при сохранении герметичности изделий из стали). Благодаря высокой степени локализации пластической деформации в приконтактной зоне этот перспективный способ сварки позволяет получать прочное соединение при нагреве свариваемых материалов до температур ниже температур рекристаллизации более твердого материала. В последнее время показано, что этим способом можно сваривать также и сталь со сплавами титана и меди. В этом отношении способ клинопрессовой сварки имеет ряд неоспоримых преимуществ перед сваркой трением [8]. В последнее время процессы соединения разнородных материалов в твердой фазе получили применение при изготовлении композиционных материалов, например слоистых и с волокнистым и сеточным упрочнением. К этим процессам относятся сварка взрывом, прокаткой, вакуумная диффузионная и термокомпрессионная сварка пакетов фольг из матричного материала и слоев сеток и волокон и ленточных полуфабрикатов, полученных в виде тонких листов, состоящих из рядов волокон, на которые методом плазменного напыления нанесен матричный материал. В связи с этим одной из важнейших современных проблем становится сварка самих композиционных материалов.
Большие технологические возможности имеет сварка взрывом. Сваркой взрывом соединяют самые разнообразные (компактные и порошковые) материалы в однородном и разнородном сочетаниях, а также осуществляют сложное формоизменение [17].
Характерной особенностью сварки взрывом является многообразие схем ее осуществления в зависимости от природы соединяемых материалов, формы их существования (компактные или порошковые), конфигурации изделия и т. д. Основными дефектами при сварке взрывом являются дискретно расположенные вдоль границы соединения оплавленные участки, снижающие, например, коррозионную стойкость зоны соединения. Изложенные ранее представления о природе образования соединения металлов в твердом состоянии, а также существующие в настоящее время расчетные модели позволяют оценивать параметры процесса сварки взрывом, при которых сварное соединение характеризуется высокой прочностью и отсутствием локальных оплавленных участков металла. Эти расчеты основаны на учете скорости движения дислокаций, частоты их выхода в зону соединения, энергии, выносимой каждой дислокацией, и энергетического барьера в пределах отдельного активного центра, при достижении или превышении которого осуществляется элементарный акт взаимодействия (образование химических связей). Использование такого подхода позволяет существенно сократить объем экспериментальных исследований, а в ряде случаев прогнозировать выбор материалов конкретного изделия.
Среди способов сварки импульсным воздействием следует особо выделить магнитно-импульсную сварку — разновидность сварки взрывом. При магнитно-импульсной сварке соударение свариваемых деталей обеспечивается импульсным магнитным полем от разряда батарей конденсаторов. Длительности импульса и скорости соударения при этом методе сварки того же порядка, что и при сварке взрывом. Магнитно-импульсная сварка обладает тем преимуществом по сравнению со сваркой взрывом, что ее параметры более легко управляемы и ее применение возможно в любых цеховых условиях. Она особенно целесообразна в тех случаях, когда необходимо сохргнение структуры и механических свойств материала в зоне сварного соединения на уровне, близком к исходному. Этим методом можно сваривать, например, внахлестку трубы из разнородных материалов: алюминий — медь, алюминий — коррозионностойкая сталь, цирконий — нержавеющая сталь и т. п.
Тема:Сварка плавлением.
Сварка плавлением — это процесс соединения двух деталей или заготовок в результате кристаллизации общей сварочной ванны, полученной расплавлением соединяемых кромок. Этот процесс наиболее распространен в сварочной технике.
Нагреть металл соединяемых кромок изделия выше температуры плавления для образования сварочной ванны можно только в том случае, если источником энергии вводится в зону сварки теплоты гораздо больше, чем отводится за это же время процессами охлаждения.
Основная часть теплоты уходит на нагрев холодного изделия, так как теплопроводность металлов очень высокая. Кроме того, большое количество теплоты теряется излучением в окружающую среду.
Поэтому источник энергии при сварке плавлением должен быть большой мощности, высокой сосредоточенности, т. е. концентрировать выделяющуюся энергию на малой площади сварочной ванны и успевать расплавлять все новые и новые порции металла, обеспечивая этим определенную скорость сварки.
Из всех источников энергии, применяемых при сварке плавлением, наибольшей плотностью энергии обладает электронный луч (109 Вт/см2).
Однако наиболее широкое применение в качестве источников энергии для сварки плавлением получил дуговой электрический разряд, или электрическая дуга. Это связано с тем, что для возбуждения электронного луча требуется вакуум 10-4—10-5 мм рт. ст.; кроме этого, применение электронного луча для сварки связано с разработкой специальной аппаратуры, высоким напряжением (~20 кВ) и с необходимостью защиты обслуживающего персонала от опасного рентгеновского излучения.
Поэтому его используют для специальных целей, главным образом для сварки тугоплавких и химически активных металлов.
Пламя ацетилено-кислородной горелки находит более ограниченное применение, главным образом при ремонтных работах.
Итак, процесс сварки плавлением осуществляется источником энергии, движущимся по свариваемым кромкам с заданной скоростью (рис. 7).
Рис. 7. Схема сварки плавлением.
Если бы он был неподвижным, то форма сварочной ванны была бы симметричной, а ее сечение круглым. Так как источник энергии движется, то форма сварочной ванны оказывается несимметричной и имеет вид вытянутого овала. Размеры и форма сварочной ванны зависят от мощности источника и от скорости его перемещения, а также от теплофизических свойств металла.
При сварке листовых конструкций из пластически деформированного металла (проката) зона сварки существенно отличается по структуре и свойствам от основного металла. Наличие неоднородностей металла вызывает, в свою очередь, деформацию при короблении сварного соединения.
Введение большого количества энергии при сварке для образования сварного шва вызывает существенную неоднородность в металле сварного соединения — как результат воздействия теплового поля.
Рис. 8. Структура металла шва и околошовной зоны после сварки плавлением.
В сварном соединении резко различаются три области (рис. 8):
а) основной металл, имеющий в результате прокатки и термической обработки однородную мелкозернистую кристаллическую структуру;
б) зона термического влияния (околошовная зона), в которой металл находился некоторое время при высокой температуре, доходящей на линии сплавления до температуры плавления металла; в этих условиях может резко изменяться структура металла, особенно структура заливающихся сталей; увеличивается размер кристаллических зерен, прорастающих в процессе кристаллизации ванны за линию сплавления; по ширине зоны термического влияния структура металла тоже неоднородна в соответствии с температурным полем при сварке;
в) сварной шов — металл шва представляет собой литую структуру, но имеет характерные особенности.
Кристаллизация сварочной ванны начинается от поверхности сплавления, состоящей из оплавленных кристаллов, которые прорастают в еще жидкую сварочную ванну, как только ее температура достигнет точки плавления. Такая встречная кристаллизация с двух поверхностей сплавления (оплавленные кромки) оттесняет примеси в центр сварочной ванны, создавая неоднородность состава металла шва. Правда, эта неоднородность сглаживается в результате диффузии, идущей при высоких температурах с большой скоростью; в целом структура металла шва оказывается неблагоприятной.
Однако, регулируя процесс кристаллизации изменением скорости охлаждения и направлением отвода теплоты, можно значительно улучшить литую структуру металла шва. Академик Н. Н. Рыкалин создал стройную теорию тепловых процессов при сварке, позволяющую заранее определить оптимальные режимы сварки изделий и регулировать процессы кристаллизации в зоне сварки.
Нагрев металла при сварке до температур, превышающих температуру его плавления, вызывает окисление металла шва и изменение его химического состава. Как будет показано при рассмотрении отдельных способов сварки, существуют два основных пути сохранения требуемого качества металла шва и защиты его от окисления:
1) защита металла сварочной ванны шлаком и введение в процессе сварки легирующих компонентов, повышающих качество металла шва и предохраняющих его от окисления;
2) защита зоны сварки от воздушной атмосферы путем создания защитной атмосферы из инертных газов (аргона, гелия) или из активных газов, таких, как углекислый газ (С02), а также путем создания вакуума.
Сварка – процесс получения неразъемного соединения частей изделия путем местного сплавления или пластической деформации металла, в результате чего возникает прочное сцепление металлов, основанное на межатомном взаимодействии.
Сварочная дуга - длительный мощный электрический разряд.
Сущность процесса – При сварке плавлением кромки соединяемых деталей и дополнительный (присадочный) металл, применяемый для заполнения зазора между ними, нагреваются до расплавления. После перемешивания основного и дополнительного металлов получается общая сварочная ванна. В результате охлаждения и затвердевания этой ванны образуется прочное соединение металлических деталей. Процесс образования сварного соединения происходит в данном случае без воздействия давления.
Все существующие сварочные процессы можно разделить на две основные группы — сварку давлением и сварку плавлением. По виду энергии, необходимой для образования сварного соединения, и условиям введения ее в металл сварка подразделяется на дуговую, газовую, термитную, электрошлаковую, электронно-лучевую, контактную, трением, ультразвуковую и другие виды. По степени автоматизации сварка подразделяется на ручную, полуавтоматическую и автоматическую.
Для получения неразъемных соединений раньше преимущественно использовалась клепка. Процесс клепки связан с большими затратами металла. Сварка позволяет экономить от 10 до 20% металла по сравнению с клепкой, до 30% по сравнению со стальным литьем и до 50% по сравнению с чугунным литьем.
Сварное изделие проще в изготовлении и и дешевле, чем клепаное. Сварные швы, по сравнению с клепаными, имеют более высокую плотность, прочность и надежность. При использовании сварки уменьшаются затраты труда на изготовление металлоконструкций, улучшаются условия труда в металлообрабатывающих цехах.
Применение сварки позволяет использовать самые разнообразные профили металла. Для сжатых стержней в клепаных изделиях часто применяют уголки.
Сваркой можно получить расположение уголков, дающие трубчатообразный профиль. Благодаря своим преимуществам сварка металлов нашла широкое применение во всех отраслях народного хозяйства.
Сущность способа.
К электроду и свариваемому изделию для образования и поддержания сварочной дуги от источников сварочного тока подводится постоянный или переменный сварочный ток. Сварочная дуга (1, см. рис) горит между металлическим стержнем электрода (2) и основным металлом (3) Под действием тепла дуги металл дуги электрода, покрытие электрода и основной металл расплавляются, образуя сварочную ванну (4). Капли жидкого металла (5) с торца расплавленного электродного стержня переносятся в ванну через дуговой промежуток. Вместе со стержнем плавится покрытие электрода (6), образуя вокруг дуги газовою защиту (7) и жидкую шлаковую ванну (8). По мере движения дуги, металл сварочной ванны затвердевает, образуется сварочный шов(9) и шлаковая корка(10) на поверхности шва.
Глубина, на которую расплавляется основной металл, называется глубиной проплавления. Она зависит от режима сварки (силы сварочного тока и диаметра электрода), пространственного положения сварки, скорости перемещения дуги по поверхности изделия (торцу электрода и дуге сообщают поступательное движение вдоль направления сварки и поперечные колебания), от конструкции сварного соединения, формы и размеров разделки свариваемых кромок и т. п. Размеры сварочной ванны зависят от режима сварки и обычно находятся в пределах: глубина до 7 мм, ширина 8-15 мм, длина 10-30 мм. Доля участия основного металла в формировании металла шва обычно составляет 15-35%.
Расстояние от активного пятна на расплавленной поверхности электрода до другого активного пятна дуги на поверхности сварочной ванны называется длиной дуги. Расплавляющееся покрытие электрода образует вокруг дуги и над поверхностью сварочной ванны газовую атмосферу, которая, оттесняя воздух из зоны сварки, препятствует взаимодействиям его с расплавленным металлом. В газовой атмосфере присутствуют также пары основного и электродного металлов и легирующих элементов. Шлак, покрывая капли электродного металла и поверхность расплавленного металла сварочной ванны, способствует предохранению их от контакта с воздухом и участвует в металлургических взаимодействиях с расплавленным металлом.
Кристаллизация металла сварочной ванны по мере удаления дуги приводит к образованию шва, соединяющего свариваемые детали. При случайных обрывах дуги или при смене электродов кристаллизация металла сварочной ванны приводит к образованию сварочного кратера (углублению в шве, по форме напоминающему наружную поверхность сварочной ванны). Затвердевающий шлак образует на поверхности шва шлаковую корку.
Ввиду того, что от токоподвода в электрододержателе сварочный ток протекает по металлическому стержню электрода, стержень разогревается. Этот разогрев тем больше, чем дольше протекание по стержню сварочного тока и чем больше величина последнего. Перед началом сварки металлический стержень имеет температуру окружающего воздуха, а к концу расплавления электрода температура повышается до 500-600° С (при содержании в покрытии органических веществ - не выше 250° С). Это приводит к тому, что скорость расплавления электрода (количество расплавленного электродного металла) в начале и конце различна. Изменяется и глубина проплавления основного металла ввиду изменения условий теплопередачи от дуги к основному металлу через прослойку жидкого металла в сварочной ванне. В результате изменяется соотношение долей электродного и основного металлов, участвующих в образовании металла шва, а значит, и состав и свойства металла шва, выполненного одним электродом. Это - один из недостатков ручной дуговой сварки покрытыми электродами.
2. Сварные соединения
Сварное соединение - неразъемное соединение, выполненное сваркой. Сварное соединение (рис. 1.1) включает три образующиеся в результате сварки характерные зоны металла в изделии: зону сварного шва 1, зону сплавления 2, зону термического влияния 3, а также часть основного металла 4, прилегающую к зоне термического влияния.
зоне термического влияния.
Рис. 1.1. Сварное соединение
Сварной шов - участок сварного соединения, образовавшийся в результате кристаллизации расплавленного металла.
Металл шва - сплав, образованный расплавленным основным и наплавленным металлами или только переплавленным основным металлом.
Основной металл - металл подвергающихся сварке соединяемых частей.
Зона сплавления - зона, где находятся частично оплавленные зерна металла на границе основного металла и металла шва. Эта зона нагрева ниже температуры плавления. Нерасплавленные зерна в этой зоне разъединяются жидкими прослойками, связанными с жидким металлом сварочной ванны и в эти прослойки имеют возможность проникать элементы, введенные в ванну с дополнительным металлом или сварочными материалами. Поэтому химический состав этой зоны отличен от химического состава основного металла.
Зона термического влияния - участок основного металла, не подвергшийся расплавлению, структура и свойства которого изменились в результате нагрева при сварке, наплавке или резке.
Тип сварного соединения определяет взаимное расположение свариваемых элементов. Различают: стыковые, угловые, тавровые, нахлесточные и торцовые сварные соединения.
Стыковое соединение - сварное соединение двух элементов, примыкающих друг к другу торцовыми поверхностями и расположенных в одной плоскости или на одной поверхности (рис. 1.2). Поверхности элементов могут быть несколько смещены при соединении листов разной толщины (см. рис. 1.2, б).
Рис. 1.2. Стыковые соединения
Угловое соединение - сварное соединение двух элементов, расположенных под углом и сваренных в месте примыкания их краев (рис. 1.3).
Рис. 1.3. Угловые соединения
Тавровое соединение - сварное соединение, в котором торец одного элемента примыкает под углом и приварен к боковой поверхности другого элемента (рис. 1.4).
Рис. 1.4. Тавровые соединения
Нахлесточное соединение - сварное соединение, в котором сваренные элементы расположены параллельно и частично перекрывают друг друга (рис. 1.5, а, б). Отсутствие опасности прожогов при сварке облегчает применение высокопроизводительных режимов сварки. Применение нахлесточных соединений облегчает сборку и сварку швов, выполняемых при монтаже конструкций (монтажных швов).
Торцовое соединение - сварное соединение, в котором боковые поверхности сваренных элементов примыкают друг к другу (рис. 1.5, е).
Рис. 1.5. Нахлесточные (а, б) и торцовое соединения (в)
3. Сварные швы (типы)
Сварной шов - участок сварного соединения, образовавшийся в результате кристаллизации расплавленного металла.
Сварные швы подразделяют по разным признакам: по типу шва, по протяженности, по способу выполнения, по пространственному положению и по форме разделки кромок.
По типу сварные швы делят на стыковые, угловые и прорезные.
Стыковой шов - сварной шов стыкового соединения. Угловой шов - сварной шов углового, нахлестанного или таврового соединений. Прорезной шов (рис. 1.6) получается в результате полного проплавления верхнего, а иногда и последующих листов, и частичного проплавления нижнего листа (детали). Частным случаем прорезного шва является точечный или пробочный шов (электрозаклепка - при дуговой сварке) (рис. 1.6, г). Прорезные швы при приварке толстого листа (рис. 1.6, д) могут выполняться по заранее выполненным отверстиям в верхнем листе (при точечном шве) или прорези (при непрерывном шве).
Различают следующие характеристики сварного шва: ширину, выпуклость, вогнутость и корень шва.
Рис. 1.6. Прорезные швы
Ширина шва е - расстояние между видимыми линиями сплавления сварного шва (см. рис. 1.2, а). Выпуклость шва g определяется расстоянием между плоскостью, проходящей через видимые линии границы сварного шва с основным металлом и поверхностью сварного шва, измеренным в месте наибольшей выпуклости (см. рис. 1.2, а; 1.4, а). Вогнутость шва T определяется расстоянием между плоскостью, проходящей через видимые линии границы шва с основным металлом и поверхностью шва, измеренным в месте наибольшей вогнутости (см. рис. 1.2, в; 1.3, в). Вогнутость корня стыкового шва является дефектом обратной стороны одностороннего шва. Корень шва - часть сварного шва, наиболее удаленная от его лицевой поверхности (см. рис. 1.2, б; 1.4, а). По существу это обратная сторона шва, в которой различают ширину е1 и высоту g1 обратного валика (см. рис. 1.2, а).
Угловой шов имеет следующие размерные характеристики: катет, толщину, расчетную высоту. Катет углового шва к определяется кратчайшим расстоянием от поверхности одной из свариваемых частей до границы углового шва на поверхности второй свариваемой части (см. рис. 1.3, в; 1.4, а). Катет задается в качестве параметра режима, который нужно выдерживать при сварке. Толщина углового шва а - наибольшее расстояние от поверхности углового шва до точки максимального проплавления основного металла (см. рис. 1.4, а). Для оценки прочности сварного соединения используют расчетную высоту углового шва - р (см. рис. 1.4, а). Для угловых швов более благоприятна вогнутая форма поверхности шва с плавным переходом к основному металлу (см. рис. 1.3, в).
По протяженности сварные швы подразделяют на непрерывные и прерывистые. Стыковые сварные швы, как правило, выполняют непрерывными. Угловые швы могут быть непрерывными (рис. 1.7, а) и прерывистыми (рис. 1.7, б), с шахматным (рис. 1.7, в) и цепным (рис. 1.7, г) расположением отрезков шва. Угловые швы могут быть выполнены и точечными швами (рис. 1.7, б, д).
Рис. 1.7. Угловые швы тавровых соединений
По способу выполнения различают сварку: одностороннюю и двустороннюю, однослойную и многослойную. Одностороннюю сварку стыкового сварного соединения выполняют со сквозным проплавлением кромок на подкладке или без подкладки (на весу). Двустороннюю сварку выполняют с зачисткой (удалением) корня шва (механической обработкой) перед сваркой обратной стороны сварного соединения или без зачистки корня шва. При двусторонней сварке зачастую приходится кантовать изделие или вести сварку в трудном потолочном положении.
Многослойный шов применяют при сварке металла большой толщины, а также для уменьшения зоны термического влияния. Под слоем сварного шва (I—IV на рис. 1.8) понимают часть металла сварного шва, которая состоит из одного или нескольких валиков (1-5 на рис. 1.8), располагающихся на одном уровне поперечного сечения шва. Валик - металл сварного шва, наплавленный за один проход. Под проходом при сварке подразумевается однократное перемещение в одном направлении источника тепла при сварке или наплавке.
Рис. 1.8. Многослойный шов
По пространственному положению с учетом требований международных стандартов различают следующие сварные швы: горизонтальные (на вертикальной плоскости), вертикальные, потолочные и швы, сваренные в нижнем положении (рис. 1.9, 1.10). На рисунках даны русские и в скобках международные обозначения. Схемы сварки, стыков труб с горизонтальной, вертикальной или наклоненной осью показаны на рис. 1.10.
Рис. 1.9. Положение шва при сварке стыковых (а) и тавровых (б) соединений листов:
HI - нижнее; Н2 - нижнее тавровых соединений; B1 - вертикальное (сварка низу вверх); B2 - вертикальное (сварка сверху вниз); Г - горизонтальное; П1 - потолочное; П2 - потолочное тавровых соединений
Рис. 1.10. Положение шва при сварке стыковых (а) и угловых (б) соединений труб:
HI - нижнее при горизонтальном расположении осей труб (трубы), свариваемых (привариваемой) с поворотом; Н2 - нижнее при вертикальном расположении оси трубы, привариваемой без поворота или с поворотом; В1 - переменное при горизонтальном расположении осей труб (трубы), свариваемых (привариваемой) без поворота "на подъем"; В2 - переменное при горизонтальном расположении осей труб (трубы), свариваемых (привариваемой) без поворота "на спуск"; Г - горизонтальное при вертикальном расположении осей труб, свариваемых без поворота или с поворотом; Н45 - переменное при наклонном расположении осей труб (трубы), свариваемых (привариваемой) без поворота; П2 - потолочное при вертикальном расположении оси трубы, привариваемой без поворота или с поворотом
Комментариев нет:
Отправить комментарий